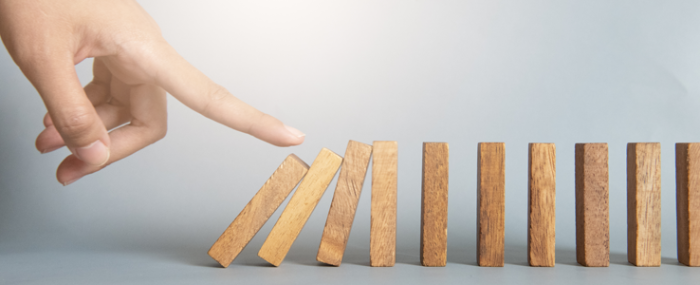
The continuation of the shortage situation
2022 has not even passed the halfway point and has already presented new – major – challenges for the electronics manufacturing supply chain. While the industry is doing all it can to alleviate current supply chain constraints – it still has to fight earthquakes, lockdowns and logistical headaches.
On January 3, 2022, a magnitude 6.0 earthquake occurred off the east coast of Taiwan. However, as most of the local DRAM and foundry fabs are located in the northern and central parts of the island, investigations showed that no notable damages to the equipment from the fabs has occurred.
There were already concerns brewing in the wider memory market about the supply side being affected by the COVID-19 lockdown in the Chinese city of Xi’an. Thankfully the earthquake did not add to these existing concerns.
On January 22, a series of major earthquakes that occurred off the coast of Kyushu, Japan forced Toshiba Electronic Devices & Storage Corporation to suspend operations at its semiconductor plant in Oita, southern Japan.
However, Toshiba wasn't the only electronics company affected by the earthquakes. Renesas soon confirmed that some equipment had halted operations.
While Toshiba confirmed damage to some production lines at its Oita operations – focuses on semiconductor production – Renesas, and its operations in the area, managed without any damage.
On January 26, Toshiba resumed production on the 150-mm wafer line at its Oita operations – but it would take until February 14 before the company could start the wafer input on the 200-mm line and to February 28, before full pre-earthquake production levels were restored at the company's Oita operations.
Russias invasion of Ukraine
Ukraine is a major supplier of raw material gases for semiconductors including neon, argon, krypton, and xenon. According to TrendForce, the country supplies nearly 70% of the world's neon gas capacity. And even though the proportion of neon gas used in semiconductor processes is not as high as in other industries, it is still a necessary resource. Many companies, including Micron, ASML and TSMC were quick to diversify their sourcing for noble gases.
Micron stated that its supply of Neon is primarily sourced and originates from various suppliers across the European Union, United States and Asia. An ASML spokesperson told Reuters that the company sources less than 20% of the gas from the region. Regardless, ASML would start looking for alternative sources for the amount of neon it uses. During a company earnings call, TSMC CEO C. C. Wei stated that the company’s strategy is to continuously develop multi-source supply solutions to build a well-diversified global supplier base.
“For specialty chemicals and gases, including neon and geon we source from multiple suppliers in different regions, and we have prepared a certain level of inventory stock on hand.”
What started as a conflict has developed into an ongoing war, affecting people and businesses. International economic sanctions have been launched against Russia and many companies has ceased local operations in the country and stopped all shipments to Russia.
“Russia’s invasion of Ukraine is a negative supply shock on already strained supply chains. It will take many months to fully determine the full effect it is having on the electronics industry,” said Shawn DuBravac, IPC chief economist, in a press release in May.
With the ongoing war, air freight has become a concern for many. The air space over Russia and Ukraine is shut off – which adds extra hours to any air freight, which requires more fuel per plane and therefore cannot hold as much transport capacity.
In early March, EMS provider Asteelflash provided an update of the rail/road trade lane from Asia to Europe, stating that The Silk Roads were at a complete standstill.
The company stated further that big rail consumers were shifting to sea freight – adding additional pressure on sea-based logistics operations.
Lockdown hits Shenzhen as covid infections increases
As we entered March a new – or old – issue arose. In a response to an increase of Covid-19 cases in the Chinese city of Shenzhen, the government – maintaining its strict zero-Covid policy – decided to shutdown the southern business centre of the city. At the same time, access to Shanghai was restricted by suspending bus services.
Citywide nucleic acid tests were launched as Shenzhen tired to curb developments. A notice by the Shenzhen COVID-19 Prevention and Control Command Office stated that employees of business – except those dealing with the supplies of essentials like water, electricity, fuel, gas, communications, food and public sanitation – would be required to work from home, or suspend production and operation activities. Initially, these measures were said to remain in place until March 20.
But it didn’t take long until the next major lockdown would occur in China. On March 28, Shanghai entered into a lockdown – this time, local authorities wanted to preserve international transport, but the city would be closed for at least ten days.
As Shenzhen reopened, warnings went out that the city’s three main container ports and air freight routes from Shenzhen – and Hong Kong – would be heavily congested.
Data from VesselsValue in late March showed an almost five fold increase in the number of ships waiting to load or discharge at Shanghai when compares back two and half weeks. S&P Global (IHS Markit) painted a similar picture in late April, stating that total congestion levels at Shanghai’s port has increased by about 30-40% since the start of March 2022. As of today, port congestions could be around for a while.
New earthquakes hit Japan and Taiwan
A powerful magnitude 7.3 earthquake occurred off the coast of Fukushima, Japan on the evening of March 16. Most of northeastern Japan is a production centre for global upstream semiconductor raw materials.
Renesas operates three factories close to the epicenter, its Naka Factory in Hitachinaka, Ibaraki Prefecture, its Takasaki Factory in Takasaki, Gunma Prefecture and its Yonezawa Factory in Yonezawa, Yamagata Prefecture. Renesas said in an update that production at its Naka factory was halted immediately.
Murata provided an update stating that some of the buildings and equipment of its operations have been damaged at that it had stated restoration work. The affected operations were Tome Murata Manufacturing in Tome, Miyagi Prefecture; Sendai Murata Manufacturing in Sendai, Miyagi, Miyagi Prefecture; as well as Koriyama Plant and Motomiya Plant of Tohoku Murata Manufacturing located on the Fukushima Prefecture.
Two days later, on March 18, Murata resumed operations at both the Koriyama Plant and Motomiya Plant. Tome Murata Manufacturing in Tome, Miyagi, expects to resumed some of the production on March 21. The company’s Sendai operations went back online on March 22.
Renesas Yonezawa factory resumed production for all processes on March 18. The company was was back to full pre-earthquake production capacity on March 23 at its Takasaki factory. And Renesas Naka factory reached full pre-earthquake production capacity on March 23.
On March 23, just as the companies in Japan reached full pre-earthquake production levels, a 6.6 magnitude earthquake struck southeastern Taiwan. The quake was soon after followed by another 6.1 magnitude quake, as reported by the Central Weather Bureau (CWB).
Evertiq reached out to several semiconductor manufactures with operations in Taiwan for a status update.
In an emailed statement to Evertiq, TSMC said that there had been no significant impact to production and no equipment or facility damage.
Semiconductor manufacturer UMC, told Evertiq that the earthquake had no material impact on the company's operations and that all personnel are safe and manufacturing remains normal.
Micron said in a statement to Evertiq that all of its team members had been accounted for and reported to be safe and that the company was evaluating the potential impact and would update customers as appropriate.
A logistical headache
April rolled in and due to another explosion in rising covid-19 cases, Shanghai kept its rolling lockdown policy since March and now Kunshan City – a major production hub for the electronics industry near Shanghai – also felt the effects.
TrendForce reported that limited manpower, logistics and suspended transportation options meant that neighboring OEMs and ODMs could only rely on onsite inventory to barely meet the needs of production lines, further exacerbating component mismatches.
The analysts at TrendForce also pointed to the issue that MCLL suppliers in China, including those located in Tianjin, Suzhou, Wuxi, and Guangdong, have yet to be locked down. However, inter-provincial logistics and transportation have clearly felt the escalation of inspection and supervision since the end of March, resulting in prolonged transportation timetables. However, the biggest problem for MLCC suppliers at this stage is they cannot deliver materials to Shanghai and Kunshan.
If you are curious about the developments of the current semiconductor situation, you should come to Evertiq Expo Berlin where Dennis Dahlgren will provide a timeline of events – from the start of te shortage situation, all the way to where we are today.