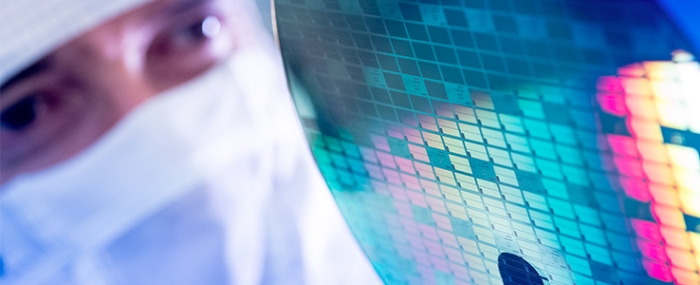
© Bosch
Business |
Bosch is betting on SiC for electromobility
Nowadays, all cars feature semiconductors; there is generally more than 50 of them in every vehicle that rolls of the production line.
The German giant is now aiming to take electromobility forward with its newly developed silicon carbide (SiC) microchips. Bosch is betting that in the future, the chips made of this material will set the pace in the power electronics – the command center for electric and hybrid vehicles.
Compared to the silicon chips used to date, SiC semiconductors have better electrical conductivity; enabling higher switching frequencies while also ensuring that much less energy is dissipated in the form of heat.
Bosch manufactures the new generation of semiconductor chips at its Reutlingen plant, 25 miles south of Stuttgart. At this plant, the company has been turning out several million microchips every day for decades.
According to the company the switch to SiC-based semiconductors can provide many advantages. In power electronics, they ensure that 50% less energy is lost in the form of heat. This saving translates into more efficient power electronics and more energy for the electric motor and therefore for the battery range. Motorists can drive 6% further on a single battery charge, Bosch writes in a press release
Another reason that the new technology also offers further potentials is the much lower heat losses of the chips, combined with their ability to work at much higher operating temperatures, mean that manufacturers can cut back on the expensive cooling of the powertrain components. The company will be using the SiC semiconductors in its own power electronics in the future.
“Thanks to our deep understanding of systems in e-mobility, the benefits of silicon carbide technology flow directly into the development of components and systems,” says Harald Kroeger, member of the Bosch board of management, in the press release. “Our semiconductor know-how helps us not only to develop new automotive functions and IoT applications but also to continuously improve the chips themselves.”
In June 2018, Bosch laid the cornerstone for its semiconductor factory in Dresden. Its manufacturing operations will use wafers with a diameter of 300 millimeters. This means significantly more chips from a wafer, and correspondingly greater economies of scale than with semiconductors based on 150- and 200-millimeter technology. Bosch produces the latter in Reutlingen, where it will also manufacture the new SiC chips.
“Semiconductors are a core component of all electrical systems. They are also turning data into a coveted raw material of the future. As they are becoming increasingly important in our fields of activity, we want to continuously expand our manufacturing operations,” Kroeger says.
In its wafer fab in Dresden, Bosch is investing around a billion euros – the largest single investment in the company’s history. In the factory, facilities are currently being installed in the clean room areas. The first associates are due to start work in the spring of 2020.