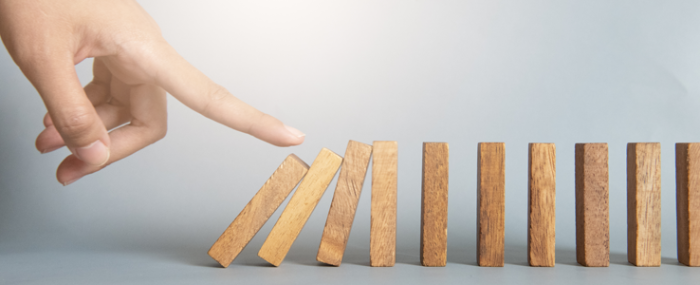
What happened to my chip supply?
The pandemic did indeed send massive ripples through supply chains around the globe – but it was never the start of the semiconductor crisis, the semiconductor supply chain was on shaky legs long before COVID-19 shut down entire countries and trade.
Before moving on, lets actually look at the definition of the word “Shortage”. Shortage is defined by Oxford Language as "a state or situation in which something needed cannot be obtained in sufficient amounts."
With the above stated definition in mind, there are arguments to be made that this shortage actually started some time ago. This current shortage entails, not only a lack of production capacity for 12-inch wafers fabricated with mature process technologies, but also 8-inch wafers in particular. And as TrendForce points out, the shortage of 8-inch wafer production capacity began to simmer in back during the second half of 2019 already. This has happened mainly due to structural changes in the semiconductor industry, with 5G smartphones and power management IC's used in new energy vehicles as two examples of such demand.
At the same time, the consumption of semiconductor production capacity has also increased multiplicatively in recent years as a result of these structural changes; And TrendForce expects demand for semiconductor capacity from emerging applications will continue to rise in the coming years.
Foundries such as TSMC, UMC and SMIC are however increasing their investments in mature process technologies, and TrendForce expects the industry’s total 8-inch wafer capacity to grow at a 3-5% CAGR from 2019 to 2023, and 12-inch wafer capacity is expected to grow at an 11-13% CAGR across the same period.
But lets get back to the series of events that got us here. We have cleared out the first part, a lack of production capacity. The second part – which might actually be the first part depending on how you chose to look at it – is trade wars. The US – China trade war and the Japan – South Korea trade added to the troubles and created concern over how geopolitical conflicts could affect manufacturing and distribution. In more practical terms the trade wars led to increased lead times, higher prices and restricted the flow of raw materials.
The US – China trade war can be divided into phases, and as reported by The Wall Street Journal, the first wave of tariffs that had a direct impact on semiconductor manufacturing hit Chinese imports back in 2018. These tariffs targeted raw materials for chips, such as silicon, reactor tubes and holders designed for semiconductor wafer production. And in a domino-effect kind of way, the tariffs that hit these raw materials are also one of the main factors that led to the 200mm wafer shortage in Q3 2019 – which we still see today. In 2019 Japan began implementing export restrictions on raw materials used to make chips on South Korea.
And then we have 2020 and the pandemic. Where industries shutdown, lockdowns happened and semiconductor manufactures shifted production from one sector to an other. But that was not all, logistics and transportation was also a nightmare, so even when production actually got back up to speed, shipping the products was a problem on its own.
The automotive industry took a hard hit in Europe, and with a industry of that size on on hold many semiconductor companies shifted their attention to a sector that was very much alive and kicking, and actually thriving. The fact that more people than ever before were working from home had led to a surge in the consumer electronics sector. Recovery within the automotive industry is still ongoing and slow. It’s hindered by the shortages in 200mm wafers as well as some substrates necessary for automotive semiconductors.
Adding fuel to the flames we also have to add in the effects of a number of other events that struck the industry and has affected supply. A fire broke out at Asahi Kasei Microsystem’s (AKM) semiconductor factory in Nobeoka, Miyazaki prefecture, Japan on October 20, 2020. The fire has completely shut down production and took three days to put out.
The severe winter weather that struck Austin, Texas in February this year caused issues for several semiconductor manufacturers in the city, as Austin Energy decided to cut the power to the companies. Samsung, NPX and Infineon were all affected by the loss of power which forced the sites to stand idle.
A month later Renesas Naka fab shut down its 300mm line as the N3 building – which houses the 300mm line – caught fire. The fire was extinguished on the same day on March 19, 2021. It took the Japanese company 100 days to get back on track at the Naka fab following the fire.
A few days later there was a fire at Taiwanese semiconductor manufacturer Panjit International's Gangshan fab. The Gangshan fab has three independent buildings, Building A, B, and C, the fire only hit in the electrical room of the top floor of Building C, and according to the company the affected electrical room only supplies power to a small area. Therefore, the impact stemming from the fire was thankfully very limited.
We also have to add the effects of the drought in Taiwan which delayed market recovery and worsened the shortages in Q2 2021. And as Fusion WorldWide points out, besides the drought, Taiwan was also dealing with another wave of Covid-19 while also dealing with geopolitical tensions. The real problem with the drought is when you consider the fact that Taiwan is responsible for 63% of the global semiconductor market share, according to data from The European Institute for Asian Studies (EIAS). Almost 75% of the global semiconductor manufacturing capacity is concentrated in East Asia; so when large-scale Covid-19 outbreaks started to be reported on during the second quarter of 2021, there were resons to be concerned.
In September, a power outage in Dresden, Germany, temporarily impacted the operations at Infineon’s, Bosch’s and GlobalFoundries’ facilities there. But the bigger issue relating to power would be China’s power rationing, which has affected production at several locations.
And now we’re here and there’s no sign of an end to the troubles. However, all is not gloom and doom, several big names have announced major investment to increase capacity, the only issue is that we won’t see the effects of this until 2023.
If you are curious about the developments of the current semiconductor situation, you should come Evertiq Expo Tampere where Dennis Dahlgren will adress the topic from the stage.