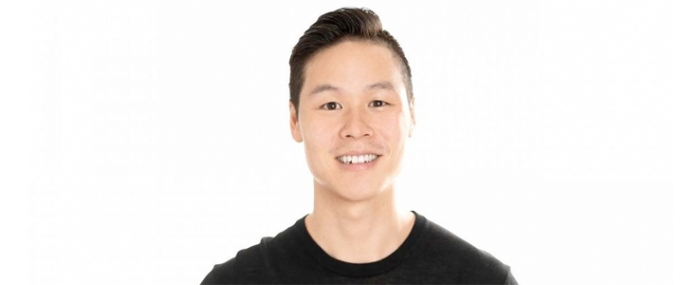
© Moov Technologies
General |
A more sustainable approach to semiconductor manufacturing
Reuse; that is the key to driving environmental sustainability in global semiconductor manufacturing, says Steven Zhou, CEO of Moov Technologies.
Author: Steven Zhou
Integrated Circuit manufacturing is a resource heavy endeavor, consuming massive amounts of energy, water, chemicals and gases, and noble metals. The world’s top semiconductor foundries and manufacturers have published aggressive targets for recycling initiatives, with 90-95% recycling of solid waste and near-zero hazardous chemical waste to landfills in 2020, according to David Wang, CEO of ACM Research. With ambitious goals for more environmentally friendly semiconductor manufacturing, the question remains: how will foundries and manufacturers achieve these goals?
As many of us learned in grade school, recycling is about the three R’s: reduce, reuse, recycle. For the semiconductor manufacturing industry, opportunity abounds to drive positive global impact through improvements on each of the three R’s. Some manufacturers are focusing on reducing waste and hazardous byproducts of semiconductor manufacturing by improving steps in the process. For example, Picosun recently announced improved Chemical Vapor Deposition (CVD) coating methods to reduce GLG emissions produced when cleaning deposition chambers.
Like “reduce”, the third R, “recycle”,” requires technological advancement to improve its application in semiconductor manufacturing as many of the inputs and outputs of the process are difficult, expensive, or hitherto impossible to recycle. That said, exciting progress has been made, such as Stanford University researchers’ success in creating degrable semiconductors, and Rice University researchers’ recent breakthrough in turning Carbon into Graphene (a valuable carbon allotrope with potential applications spanning from flexible electronics to solar cells, water filtration, and you guessed it — semiconductors!).
But the “easiest” R for the semiconductor industry is one that is often overlooked in favor of these more exciting technological developments: reuse. That said, the industry has made valiant strides towards reuse. TSMC sets a strong example for manufacturers to follow by holding themselves accountable to specific and concrete recycling goals in their CSR report. For example, TSMC set ambitious goals for 2018: recycling rate (>95%), percentage of waste sent to landfills (<1%), in-house reuse rate of resources (>30%) and tracked progress against those goals transparently for shareholders and the community to see. Nikon, an early OEM to introduce buy-back in order to promote reuse of lithography equipment, started its reuse program in 2000. According to Nikon, by March 2018, the program led to the reduction of 3,600 tons of materials that would have otherwise been disposed through reuse.
Nikon’s efforts are laudable, but could be exponentially expanded through cross-OEM global reuse of all categories of manufacturing equipment. In roughly 12 months, transactions on Moov’s marketplace led to waste reduction through reuse equivalent to ~10% of what Nikon achieved in 18 years.
About the author: Steven Zhou is the CEO and co-founder of San Francisco-based Moov Technologies, a technology-driven marketplace and asset management platform that matches buyers and sellers of pre-owned semiconductor manufacturing equipment.
About the author: Steven Zhou is the CEO and co-founder of San Francisco-based Moov Technologies, a technology-driven marketplace and asset management platform that matches buyers and sellers of pre-owned semiconductor manufacturing equipment.