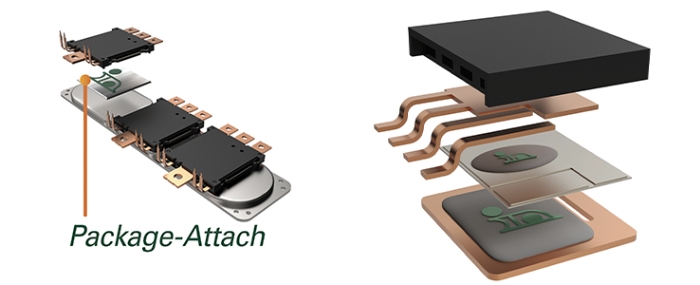
Indium Corporation addresses thermal challenges and reliability in power electronics
As compound semiconductors rise in prominence, Indium Corporation advances metal-based thermal solutions and robust materials for the automotive industry.
In the evolving landscape of power electronics, the increasing power densities in compound semiconductors present significant thermal management challenges. Evertiq reached out to Indium Corporation—a manufacturer, and supplier to the global PCB assembly electronics, semiconductor, and thermal management markets—to see how the industry is tackling these challenges.
As compound semiconductors gain more and more traction power densities continue to increase, this also means that thermal issues are bound to arise. How is Indium Corporation working to assist in solving these issues and improve thermal performance/management?
“The limitations of the bulk properties of traditional organic thermal interface materials are indeed a challenge as power densities increase, affecting both the thermal management capability and resiliency over time. At Indium Corporation, high-performance metal-based thermal interface materials are a core competency and an area we continue to focus our innovation on. Metal thermal interface materials inherently offer better thermal properties and do not degrade over time, offering a longer lifecycle,” says Joe Hertline, Product Manager – EMS/Power Electronics at Indium Corporation.
One example that Hertline mentions is Indalloy 301 LT, which is a soldering solution recently introduced to offer robust thermal performance while reducing the processing temperature needed in manufacturing. This technology is a viable alternative for power module package-attach thermal interface applications, increasing reliability and heat dissipation compared to traditional thermal interface materials, while preventing processing defects such as delamination and warpage.
How does the ongoing electrification of the automotive industry, and the expanded use of SiC and GaN, affect Indium Corporation in terms of both R&D and market opportunities?
“As these emerging power electronics devices strive to achieve higher performance and enable automotive electrification, new challenges are introduced which make the selection of assembly materials critical in order to ensure long-term stability. Higher junction temperatures, increased usage profiles, and longer service life expectations are driving requirements down to the material solutions for die-attach, die-top interconnect, and package-attach,” Hertline explains.
Hertline continues to say that Indium Corporation has focused its R&D efforts on advancing materials to specifically address these use cases, such as InFORCE MF sintering paste, Durafuse HT high-temperature lead-free solder paste, and InFORMS composite solder preform technology.
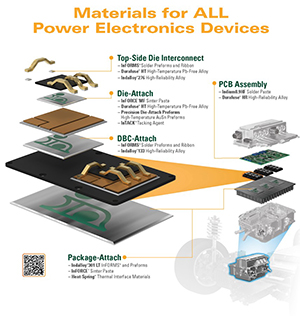
For a number of years, the number of electronic systems and components in our cars has continued to increase—and even more so due to the electrification of the industry. Miniaturisation, power electronics, and battery systems are all playing an increasingly important role. But with this, there are some reliability challenges—how is Indium Corporation working to assist in avoiding component failure and increasing the safety of today’s cars?
“Reliability enhancement is central to Indium Corporation’s roadmap strategy for automotive electrification and power electronics. Beyond the emergence of SiC and GaN, increased PCBA component density is also a key consideration. To address this need, we are introducing a new product, Durafuse HR, which is a mixed-alloy lead-free alloy technology specifically designed for extended reliability performance compared to industry-standard SAC alloys, and it can be used without changes to the manufacturing process.”
Hertline says that the company is also identifying innovative ways to leverage multiple technologies that allow the company to take performance to the next level.
“One example is the combination of complementary Indalloy 301 LT and InFORMS technologies, which together provide a superior package-attach material solution that prevents defects and premature failures within the power module while achieving robust thermal performance, mechanical resilience, and extended life.”