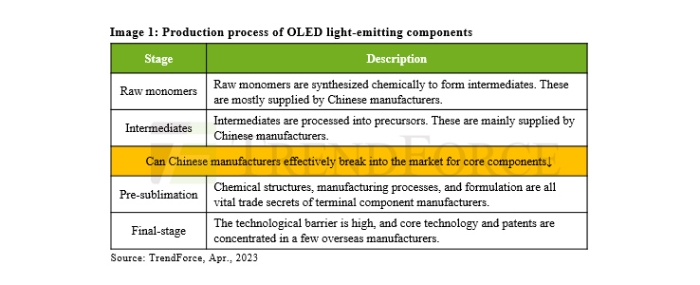
OLED materials projected to reach a valuation of $3B in 2025
TrendForce’s latest report, “AMOLED Technology and Market Status”, reveals that OLED, the next generation of digital displays, has not only taken hold of the smartphone market but is also beginning to make its move into other applications.
Organic OLED materials are the core of the industry supply chain, accounting for 23% of the cost of making smartphone panels. An increasing penetration rate has allowed the global value of OLED materials to be estimated at USD 2.23 billion in 2022, with a YoY growth rate of 30%. Production values are expected to reach US$3 billion by 2025, owing to the support of manufacturers.
OLED light-emitting components are either based on polymers or small-molecule materials. Polymers have poor solubility in organic solvents, which results in impure colour and poor film uniformity. However, when combined with printing technology, the high aperture ratio can fit more materials and compensate for the poor lifespan and efficiency of polymers. Small-molecule materials have purer colour and exhibit higher brightness, which can be applied to larger-generation OLED production. However, they are currently limited to developing FMM and vapour deposition machines.
OLED production begins with synthesising intermediates from raw monomers. Then, the intermediates are processed to become precursors before finally being sublimated and purified into terminal OLED materials. When raw monomers are synthesised chemically into intermediates, there’s a gross margin of about 10–20%. These are mainly supplied by Chinese manufacturing companies such as Jilin OLED Material, Ruilian New Materials, Aglaia Tech, and Shenzhen Mason. Terminal materials are produced via sublimation and purification and their structure will not change through subsequent production. Therefore, the chemical structure, processes, and formulas are essential to trade secrets for terminal material manufacturers. The purity of these materials after sublimation is expected to be very high, meaning that technological barriers are also very high, allowing for gross margins as high as 60–70%. The technology and patents are concentrated within a few foreign manufacturers. However, the booming market has led to an influx of upstream manufacturers, gradually breaking down past technological barriers. Some Chinese manufacturers have been able to achieve mass production of precursors and terminal materials, and are now actively competing in the supply chain and driving growth.
Apart from two electrodes, the structure of an OLED component consists of organic light-emitting materials, including the main host (light-emitting layer), guest material (dopant), and functional layers (with electron or hole transport properties). DuPont and LG Chemical are the major manufacturers of red OLEDs, while Samsung DSI and Merck mostly produce green OLEDs. UDC has a monopoly on red and green phosphorescent dopant materials due to patent barriers. Blue light-emitting materials used to be primarily supplied by Idemitsu Kosan and Merck. Recently, LG’s next generation OLED evo TV uses deuterium-based blue emitter materials—supplied by DuPont and LG Chemical—to improve blue light-emitting efficiency. Its precursors are supplied by Ruilian New Materials.
Besides established manufacturers like Tokuyama, Idemitsu Kosan, and LG, Chinese manufacturers are also beginning to enter into the market to supply functional layers, such as Laite’s Red Prime. Samsung and UDC are planning to commercialise blue phosphorescent materials in 2024 in order to address the lifetime issues of blue OLEDs. Many new technologies, such as South Korean materials manufacturer, Lordin’s, patented Zero Radius Intra-Molecular Energy Transfer (ZRIET) rely on the efficiency of energy transfer between the main host and dopant, which is highly dependent on the distance between them. When that distance approaches zero, the quantum efficiencies of the molecules will not be affected at all. Therefore, efficiency can be improved by controlling the speed of energy transfer between the internal molecules of the material. Lordin has synthesised a material that maintains the respective characteristics of the main and dopant materials as well as a high energy transfer rate, which is expected to produce OLEDs that will be four times more efficient.
TrendForce believes the next stage of mobile terminal products will shift from folding smartphones to smart wearables, IT, and automotive applications, which will place more stringent demand on OLED components. The layout of panel manufacturers is becoming clearer thanks to brand endorsements. LG, Samsung, and BOE are all aggressively competing for priority for the Tokki G8.7 evaporation machine to gain an advantage in expanding application. The accelerated commercialisation of blue phosphorescent materials and more innovative technologies, such as Samsung’s vertical evaporation developed with ULVAC, eLeap lithography, and printing processes to improve the aperture ratio will help push the expansion of OLEDs in the display industry. Meanwhile, costs will become more competitive as more Chinese manufacturers enter the market.
Vendor | Production | Customer |
Laite | R-Prime terminal materials | BOE, CSOT, EDO ... |
O´right | Functional layers & light-emitting materials | BOE, Visionox, testing EDO ... |
Ruilian New Materials | Functional layers & deuterium-based blue intermediates | Merck, DuPont, LGC, SDI |
Valiant | Monomers/Intermediates | Merck, DOW, LGC |
Aglaia Tech | Monomers/Intermediates | Merck |
Eternal Material Technology | Monomers/Intermediates | Investing in Visionox |
China Ray | Printing technology | Investing in TCL |
For more information visit TrendForce.