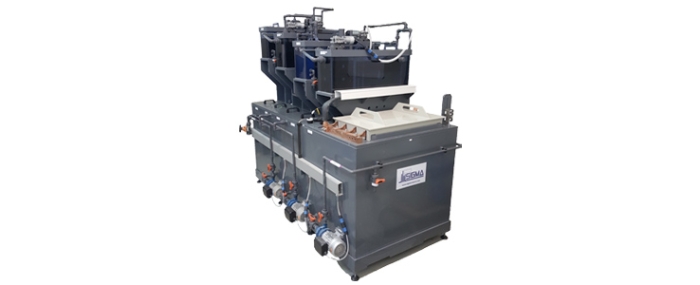
Swedish company wants to make PCB production greener
PCB’s are commonly green in colour, but the manufacturing process could become greener, and Swedish company Sigma MECER is looking to do just that.
Now this isn’t really something new, the company has a history that stretches back to 1978. From the late 70s until the early 2000s, Sigma produced and sold over 100 MECER recycling systems for alkaline etching. At the end of the 2000s, a new product line for recycling acidic etching was developed and has since been sold to a number of customers.
What it really comes down to is something many of us learned back in grade school, the three R’s – reduce, reuse, recycle. Sounds simple enough, but in reality, it’s a bit more complicated. However, Sigma MECER has solutions to tackle all of the R’s within the scope of PCB etching.
When approaching the three R’s, most people take them in order. They audit their operations and start to look at areas where they can reduce, whatever that might be. Reuse is often overlooked in favour of these more exciting technological development, but it is a step that can have major positive implications on a company’s business. Recycle is often left in the hands of the end user, and thus something that takes place after a product has left the manufacturer. However, there are of course instances where this can be recycled in the manufacturing process already.
Sigma MECER has a solution for PCB manufacturers that tackles all three R’s at once; an etchant regeneration system that enables closed-loop recycling of chemicals, rinse water and plating of pure copper sheets as a by-product. In a nutshell, the system decreases the need to refill etchants (reduce) via its regeneration system (reuse) and through the process, you end up with pure copper (recycle).
The system supports both alkaline and acidic etchant closed-loop regeneration. In an interview with Evertiq, Kristoffer Björklund, Supply Chain Manager at Sigma MECER, explains that in regards to acidic etching, the consumption of HCl is reduced by 95 % with the system, while alkaline etchant (Replenisher) is completely eliminated. This thus translates to a significant reduction of operational costs.
The copper that is etched from the panels is then recycled through an electrolysis plating where 99,995% copper purity is achieved. These copper sheets are then “harvested” bi-weekly and can be sold as anodic grade copper. However, the company says that they want to find a way where the recycled copper can be used for plating straight away – which could be a potential game changer when.
Additionally, the system allows for the reuse of the rinse water for the etching process by removing the copper content from it. This improves the overall environmental footprint of the entire process.
Opportunity abounds, as the system is scalable, the company explains. Also, the company is honing the processes that they already offer and keeps developing, but at the same time, Sigma MECER is testing new technologies to add to its offering.
As a Swedish company, the company has a strong footing in Europe – with Germany unsurprisingly as the main market – but there is a lot of movement on the other side of the Atlantic as well. Several projects in the US are currently in the works and the company is looking to expand its business in the Americas.
Kristoffer explains that the supply chain crisis that’s plagued the industry for the past two years has resulted in companies more seriously considering re-shoring. Something that means new manufacturing facilities and thus new potential projects for Sigma MECER.
He continues to say that the reasons why companies chose to invest in their solutions differ depending on the market. The European market is for instance more cost-focused and is looking to save money via recycling. In the US, and more specifically California the fact that the system saves rinsing water is a big selling point as the area periodically goes through water shortages. In general, newly constructed manufacturing operations tend to focus more and more on zero waste and zero emission – which only adds to the pitch of the company.
“We are actively targeting the European market and the US, and Asia as well. Though that market is still big and in a way a bit scary, but we are going there. But not right now,” Kristoffer tells Evertiq.
The company’s solutions have garnered some attention, and anyone interested in improving their environmental impact has probably come across the name. But, the company and the solution are still not household names. But with copper prices on the rise, maybe more PCB companies will look into how they can reduce, reuse, and recycle in their manufacturing process.