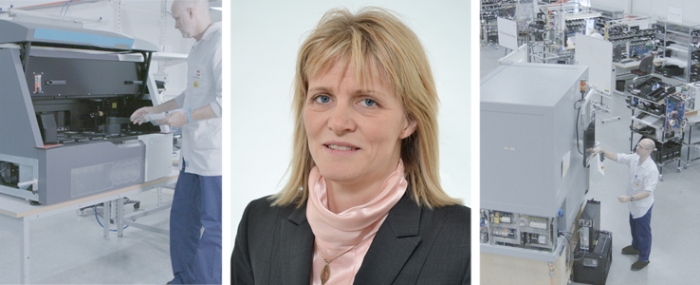
© Sanmina
Electronics Production |
Manufacturing trends to watch in 2022
If the past year has taught us anything, it’s that unpredictability is part of the ‘new normal’ for the manufacturing industry. But what's to come as we enter 2022?
By Charlotta Linnell, Business Development Manager, Sanmina
The past year offered continued supply chain challenges, COVID outbreaks, travel restrictions, material shortages and extreme weather events all impacted business continuity. This has pushed the industry to re-evaluate current practices and take a broader, long term view on how to operate moving forward. Some of the big trends we can expect to see in the new year include a shift to more regional supply chains and automation, a bigger focus on sustainable operations and prioritization of green initiatives.
Growth in Regional Supply Chains
The global supply chain crisis is expected to remain through at least the first half of 2022 as material shortages, COVID-related shutdowns and clogged ports continue. Low-cost manufacturing strategies that heavily outsourced activity to Asia are being questioned, as OEMs look to shorten supply chains by bringing certain aspects of manufacturing closer to home.
By embracing a more regional approach, OEMs aim to lower risk and complexity, improve quality and increase control over operations for the long term, leaving behind the previous mindset that only prioritized cost. ‘Made in Sweden’ or ‘Made in Europe’ slogans are becoming key marketing differentiators, not only because they improve the manufacturer’s bottom line but also because they generate a source of pride by stimulating local economies, generating jobs and reducing transportation that lessens environmental impact. These key factors have made it more attractive to move manufacturing closer to the end market.
‘Design for Automation’ (DFA) Methodologies
As more OEMs move to a regional manufacturing model, they must also consider how to design products that are suitable for automation and robotics during production processes. Incorporating a higher degree of automation will offset higher local labor costs. Automating simple assembly steps increases efficiency while reducing assembly time, throughput time and errors, which ensures better quality.
Machine learning (ML) technologies can be applied to capture valuable histories of manufacturing data that helps manufacturers better predict product quality and machine failures. As these technologies collect more data, the predictions continuously improve in their accuracy, helping manufacturers save money and reduce the negative effect of lost production output.
Increased Focus on Sustainable Operations
Incorporating more extensive risk management and forecasting analysis into the development of products is becoming a major focus, as unexpected events and fragile supply chains continue to impact operations. OEMs that have already embraced a more sustainable approach, including an updated and robust supply chain program, will better navigate next year’s ongoing challenges.
Strengthening forecast management processes and thoroughly analyzing the origin of every item on a bill of materials (BOM) for each product also makes it less likely that drastic last minute changes will be required. Designing a BOM and approved vendor list (AVL) with parts, that to the best of their knowledge, don’t have supply chain constraints, will be the best way to maintain a reliable supply.
Putting the Environment First
Leading OEMs are increasingly requesting that environmentally-friendly raw materials such as alternative plastics are incorporated into new products. Demand for higher quality products that have longer life spans is also becoming a core part of green initiatives to reduce waste. During the repair of existing products, manufacturers are also requiring more failure analysis data so they can improve reliability of new product designs to reduce turnover in the future.
When it comes to the afterlife of older products, manufacturers are placing more focus on how materials will either be re-used or disposed of to reduce environmental hazards. Manufacturers equipped with comprehensive quality programs, sustaining engineering capabilities and plans for repair, refurbishment and recycling will gain a competitive edge, as green initiatives become a key differentiator.
Electrification and the Use of Renewable Energy
The continued electrification of cars and other products will lead to increased energy demands and the need for more comprehensive renewable energy solutions. Manufacturers will see increased interest and investment for the development of components and systems required for green energy products and power storage.
Embracing Change
While it’s been another challenging year for manufacturing, it’s also presented opportunities to improve risk management programmes, manufacturing operations and the supply chain. Embracing environmental challenges in manufacturing practices, rather than fighting against them, will make organisations better prepared for 2022. The manufacturers that embrace all of these changes can create a more dynamic and flexible approach to their operations and supply chain structures. This mindset will reduce risk, streamline operations and create a clear path for continued success in the new year.
About the author:Charlotta Linnell is Business Development Manager at Sanmina, with more than 20 years of experience working with original equipment manufacturers (OEMs) and electronic manufacturing services (EMS) companies in the Nordic region. She has a strong track record of providing component sourcing, supply chain design and manufacturing solutions that support the development of complex products and systems for the medical, industrial and telecommunications industries. Charlotta is also chairwoman of the board at IUC Z-GROUP that supports manufacturing companies in the Jämtland Region as they develop digitalization and automation practices.
About the author:Charlotta Linnell is Business Development Manager at Sanmina, with more than 20 years of experience working with original equipment manufacturers (OEMs) and electronic manufacturing services (EMS) companies in the Nordic region. She has a strong track record of providing component sourcing, supply chain design and manufacturing solutions that support the development of complex products and systems for the medical, industrial and telecommunications industries. Charlotta is also chairwoman of the board at IUC Z-GROUP that supports manufacturing companies in the Jämtland Region as they develop digitalization and automation practices.