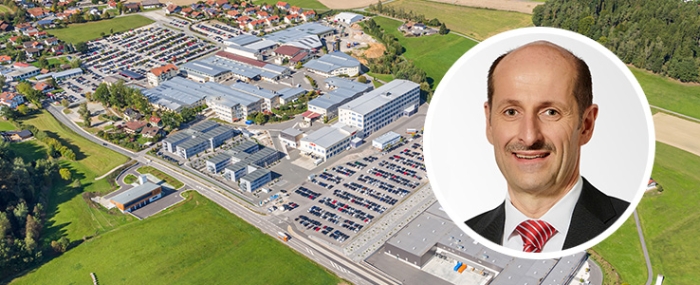
© Medienproduktion Holzer / German Popp
Electronics Production |
Evertiq's industry pulse report – Zollner
Zollner can soon look back at two very successful, but difficult years. The company was able to stay agile and rely on a well organised structure which ultimately led to them being able to use the word "successful" – while also talking about a pandemic that shut down industries and a global component shortage.
As we’re drawing closer and closer to 2022, we’re leaving another peculiar, or rather difficult, year behind us. As we celebrated the change from 2019 to 2020 we had seen the first reports about a new unknown virus that was spreading in China. It didn’t take long before we had a full pandemic on our hands, and it hit 2020 hard. It shut down the world and the year was like no other.
When 2021 came around we were still fighting the pandemic. Some part of the world were doing better than others and most industries were at least operational again. Today the pandemic is still lingering and has overstayed its welcome, not that it ever was welcomed, but adding to this fight we now also have to deal with a global shortage of semiconductors.
In this article series, Evertiq has reached out to a number of European EMS providers to see how the challenges from the last two years have affected everyday operations. First up is Markus Aschenbrenner, Member of the Board of Management at Zollner Elektronik AG.
Given the fact that we have battled the pandemic for close to two years now, what lessons have been learned and what changes have been made in your company?
"The pandemic gave us confirmation that we are on the right path: Zollner Elektronik AG promoted and advanced digitalization early on in production. That paid off in the past months. We were able to profit from a constant good overview of our current production situation thanks to that digitalization, and we continue to ramp that up. We also see great potential in the digitalization of planning and procurement. The entire supply chain needs to become much more transparent. Customers also profit from this, who receive a better overview of their inventory levels in a multi-stage supply chain," Markus Aschenbrenner tells Evertiq.
As soon as we entered 2021, it became very clear that the pandemic isn’t the only problem weighing down on the industry, the shortage of components have greatly affected our industry and adjacent ones, how is your company working to overcome the issues of tight supply?
"Our good, balanced inventory levels from 2020 contributed to the fact that we were able to produce for our customers in the first half year of 2021 without any production downtime. In the meantime, bottlenecks have led to unplanned adjustments to production and retooling. With that, some expenditures in production have significantly increased."
"We attempt to structure our production as flexibly as possible and adapt to material availability. Because we have tethered very many items, we additionally transmit all demand requirements to our suppliers with a horizon of 12 to 24 months. Particularly great success comes from our strategy to rely on direct business with component manufacturers. Using this approach creates a certain amount of leeway in this tense supply situation."
As a European manufacturer, what is your opinion on the fact that the European electronics industry is still very much dependent on Asia in terms of semiconductor supply?
"At Zollner, we pursue a “local-for local” strategy in order to offer short delivery times and first class customer service. It is for this reason that we founded our plant in China in 2004 and built production sites close to our core markets. Accordingly, we of course welcome the fact that new semiconductor factories will be established in Europe over the next few years and with that a “local-for-local” strategy can also bring stability to this supply chain. However, to make Europe interesting for component manufacturers, it will require great, collective European effort. The European Union must specify provisions - similar to how it’s done in China and somewhat in the USA," Markus Aschenbrenner explains.
And as a follow up on this, has the pandemic highlighted the need for closer and smaller supply chains in your opinion?
"Yes, and not only to make the supply chain more resilient. Even in the sense of sustainability, short transport routes are gaining ever more significance for European companies. The higher production costs, compared with Asia, can be lowered with an increase in automation and digitalization of business and production processes, such that Europe will be able to compete with low wage countries in the future."
What is the general feeling now that we are drawing close to the end of 2021 and approaching 2022?
"Behind Zollner are now two very successful but also difficult years, which were shadowed by the pandemic and the material crisis. In 2022 we will have to be prepared for further unsettled times in the component market. I reckon some demands will be taken out of the supply chain. When that will be, and what the impacts will be, is still open. What is certain is that the demand for electronics will continue to increase, and that component suppliers will need to increase their capacities accordingly. This crisis will accelerate the transformation to more “local-for-local’. We have noticed that customers also wish to increase their European value added portion and are prepared to rethink their price strategies. Along with the material situation, the availability of employees will also influence electronics industry growth. In the future, companies will need ever more employees at the global level. Zollner Elektronik AG has been training future talent continuously since the founding of the company. The success of past years has shown us that we have set upon the right course and are very well equipped to meet the challenges facing us," Markus Aschenbrenner concludes.