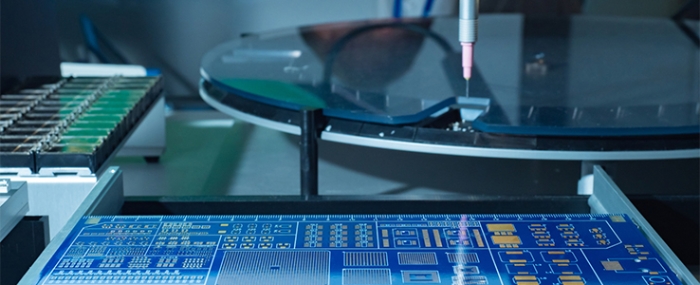
© AdobeStock
PCB |
Can early DFM speed up the production of your PCB?
When time is money and production lead times are already long. Make sure unnecessary EQs don't slow down the process additionally.
Author: Craig Haywood, Senior Technical Advisor at Elmatica
There are many, many steps in PCB manufacturing and each design needs evaluation during Design Review Checks (DRC’s) including copper distribution, stack up review, inc registration, annular ring compliance and drawing review.
This is the tooling time and if the design does not consider all the factors needed to manufacture the PCBs, this can lead to lots of EQ’s possibly meaning lots of delays to board delivery, and inevitable frustrations for customer and manufacturer.
So what can we do to prevent this?
A good start is DFM (Design for manufacture) as early as possible in the layout stage. Involve the experts to take advice on all topics that could be considered a risk and possibly improve the design. The reduction to EQ's is better for all parties and manufacturers will much rather have a clean data/drawing set that goes straight through DRC’s with minimal EQ’s raised. Check that drawings are up to date with latest information.
Elmatica has listed some examples below for your consideration.
Stack up – build, materials and laminate thickness
Does it need to be a specified build? Standard laminate thicknesses vary by manufacturer. What may be standard for one is non-stock for another. If you do not need specified dielectrics, leave this for the manufacturer to decide.
Likewise, does it need to be a specific material type, it is easier to add an IPC rating ie IPC 4101/99/126 to the material option, so the manufacturer is free to choose from available stock.
If it is a specified build try to keep laminate thickness the same/similar. Laminates will move differently during the bonding cycle, it is easier for a manufacturer to predict this movement if the laminates are all the same thickness.
Is it symmetrical preventing potential bow and twist concerns?
Ensure specified prepreg thicknesses are suitable for finished copper thickness i.e. plated layers or copper weights greater than 35um will usually need more prepreg to avoid delamination.
Keep the copper distribution balanced and avoid large copper free areas in the build that may lead to low pressure areas during bonding – reduce the risk of panel creasing or delamination. Manufacturers will ask if they can add copper where there is risk of low pressure.
Impedance control – are you in control of it?
Do you need test results that require coupons on manufacturing panels taking up manufacturing space? Or, if you have a specified build can you accept “impedance by design” and add this note to the drawing? Can you add a note to the drawing confirming the manufacturer is free to adjust tracks/gaps to meet impedance targets?
Author: © Elmatica's Senior Technical Advisor, Craig Haywood shares some of his advice.
Annular rings The design needs to match the drawing requirement so if you specify IPC 6012 Class 2 or 3 then the drill/pad combination needs to be suitable for the release criteria. Assuming the manufacturer has a registration tolerance of 100um, this then needs to be added to the remaining annular requirement eg 25um Class 2, 50um Class 3. Here’s an example based on drilled size of 300um;Craig Haywood
- Class 2 - Drill 300um, pad size should be 550um (125+125um)
- Class 3 – Drill 300um, pad size should be 600um (150+150um)
Author: © Elmatica's Senior Technical Advisor, Craig Haywood shares some of his advice.