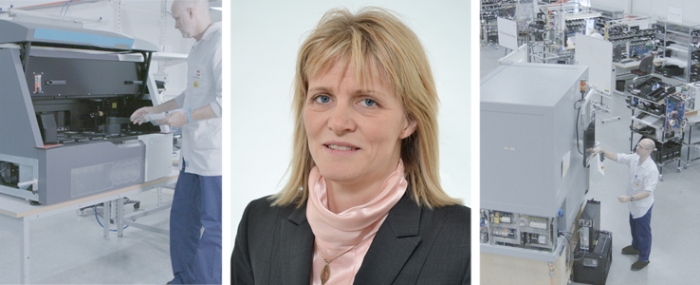
© Sanmina
Electronics Production |
Reasons to outsource manufacturing
When it comes to orchestrating all of the complexities associated with the manufacturing of a product, should innovators and businesses build a product themselves or outsource production? Lets look at the benefits in choosing an EMS to handle your manufacturing.
By Charlotta Linnell
At the heart of most organizations, there are innovators that can change an entire industry with a fresh idea or a unique offering. They enjoy the independence that comes with building their business and handling all operational aspects on their own. But when it comes to orchestrating all of the complexities associated with the manufacturing of a product, should businesses build a product themselves or outsource production? This is a question that many business leaders ask themselves and the answer is not a simple one.
The best approach is to take a step back and determine the core competency of the organization. Is it an algorithm, a unique chemistry or the innovative design of a product? Is it marketing, logistics, manufacturing, or something else? Not even the largest companies do everything themselves, so why should any other business? If it’s in an organization’s DNA to handle all of the complexities of manufacturing, including building a supply chain, setting up production lines and designing a quality management system (QMS) and an IT infrastructure, then forging a path on their own is the right choice.
But if product innovation, marketing, or some other area is the core competency, then focusing on those strengths and engaging a credible partner that already has the infrastructure, resources and experts in place to handle manufacturing is the best choice.
Outsourcing Advantages
The benefits of outsourcing depends on what infrastructure has already been established and what still needs to be put in place for each company. Overall, there are four main advantages:
1. Variable versus fixed costs. To build and drive a manufacturing facility requires a great deal of investment and capital expenditure. If a company invests in high-end manufacturing equipment, that investment will need to be written off, even if demand and volumes decrease, which will eat up margins. It’s more difficult to distribute the capital costs of owning a production line, unless a company has extremely high and stable product volumes. Rather than getting stuck paying fixed costs for facilities, staff, equipment, sourcing and inventory, companies that choose to outsource build flexibility into their cost model and pay variable costs for manufacturing, only when products are required. This can erase millions of dollars from a company’s balance sheet and frees up working capital that can be applied to new product development or other core competencies of the business.
2. Flexibility of resources. To share resources through an outsourcing model enables companies to tap the rich experience from engineering, quality and component commodity teams without the burden of having to manage all of the staff. Because EMS providers operate across many different markets, they have an expansive base of knowledge that can improve the design, cost and time to market of new products.
Sharing resources is especially important during turbulent times, in order to maintain margins when volumes decrease. EMS providers serve many different companies that typically don’t have the same highs and lows in their demand cycles, ensuring that resources won’t suddenly become depleted. This provides flexibility for either allocating or pulling back on workforce and production lines for various projects, based on changing business needs.
3. Sophisticated infrastructure for optimized production. By choosing to outsource, companies can rely on an EMS provider with an existing and sophisticated infrastructure that is battle-tested to meet a myriad of manufacturing requirements and regulations. Key infrastructure aspects include a centralized QMS and IT system that share integrated production data, regulatory requirements, best practices, audit results and customer feedback to proactively drive improvements in manufacturing and product quality.
EMS providers that leverage a cloud-based manufacturing execution system (MES) are able to automatically track data from all of the manufacturing equipment on the factory floor via the cloud so that staff can monitor production performance in real time. The system enforces pre-programmed rules to reduce errors and optimize production. The purchasing system used by an experienced EMS provider seamlessly provides processes for everything from evaluating suppliers, escalating material shortages, managing component suppliers and ensuring the placement of skilled staff.
4. Knowledgeable teams. Sourcing teams at leading EMS providers have deep industry connections and product knowledge to propose alternative supply chain options and low-cost materials or components. An EMS provider with global spend shares costs across multiple regions and has better pricing, better logistics for ordering and receiving, and better local support across different locations.
Top EMS provider also offer the ability to leverage a team of design experts that can provide a second opinion on an existing design or take on entirely new design projects on behalf of the company. Leveraging their cross-industry experience, they can provide a different perspective that could improve the design, cost or quality of a product.
Making the Right Choice
To outsource production is an important decision that is not entirely without risk. The majority of potential issues, however, can be prevented by proactively sharing concerns up front with a selected outsourcing partner. With several decades of experience working across multiple industries and different types of businesses, EMS providers are adept at working with new customers to find the right solutions.
Businesses that choose to outsource free themselves from the complexities of production and can tap a variety of sophisticated services from EMS providers that can improve the quality, cost, design and time to market of a product. Contrary to relinquishing control, outsourcing enables them to drive the strategic direction of their business and empowers them to focus on all of the things they love to do, based on their core competencies.
About the author: Charlotta Linnell is Business Development Manager at Sanmina, with more than 20 years of experience working with original equipment manufacturers (OEMs) and electronic manufacturing services (EMS) companies in the Nordic region. Charlotta has a strong track record for providing component sourcing, supply chain design and manufacturing solutions that support the development of complex products and systems for the medical, industrial and telecommunications industries.
About the author: Charlotta Linnell is Business Development Manager at Sanmina, with more than 20 years of experience working with original equipment manufacturers (OEMs) and electronic manufacturing services (EMS) companies in the Nordic region. Charlotta has a strong track record for providing component sourcing, supply chain design and manufacturing solutions that support the development of complex products and systems for the medical, industrial and telecommunications industries.