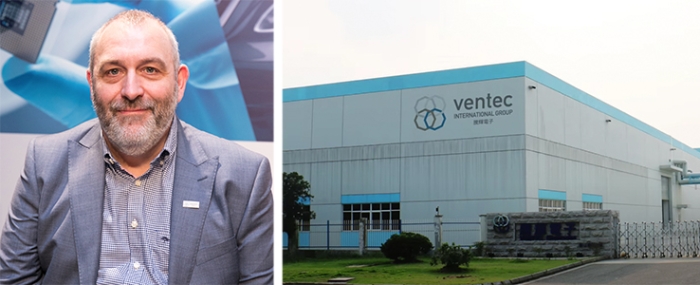
© Ventec International Group
Analysis |
Is This The Perfect Storm?
As we reach the end of a difficult year managing the many challenges caused by the COVID-19 pandemic, another series of challenges is rapidly coming into focus for EMEA and North American PCB manufacturers and their supply base.
By Mark Goodwin
Increased demand, static capacity, and industrial accidents have all come together to cause longer lead-times, reduced availability, and upward price pressure for key raw materials. These factors are likely to have a mix of long, medium and short-term effects on the outlook for CCL & PP prices, but the pressure is building for significant and, in the case of copper foil, sustained price rises that would start coming into effect in early 2021.
Demand for copper foil is increasing from both PCB and battery production for e-mobility leading to an upward price pressure for copper foils as post lockdown pent-up demand starts to exceed capacity. Lead-times are stretching and prices increasing particularly for heavy copper foils (2oz / 70 micron and above) as capacity is repurposed to maximize SQM output for light weight foils to increase capacity for lithium battery production.
Copper Foil Capacity Utilisation 2020 YE (T/Year)
Source: Ventec International Group
With the forecast growth for battery demand, long lead-times, and high investments costs to increase copper foil manufacturing capacity, this situation is unlikely to ease given the policy statements and green agendas of most governments for the coming 5-10 years. The lithium battery forecasts for China alone, for example, give a strong indication of the impact on supply & demand, and price pressure for copper foils in the coming 10 years.
China Market Lithium Battery Demand for EV Cars
Remark: Every Gwh will consume 900Tons of copper foil. Source: Ventec International Group (data sources incl. Co-tech Development Corp. & Taiwan Copper Foil Manufacturing Association)
The trends are already evident in the pricing data for raw copper. Since March of this year, prices have continued to rise rapidly and have now even significantly exceeded pre-pandemic lockdown highs.
Similar conclusions were made in a recent report from Goldman Sachs who predict a sustained bull market for copper: “a bull market for copper is now fully underway with prices up 50% from the 2020 lows, reaching their highest level since 2017. This current price strength is not an irrational aberration, rather we view it as the first leg of a structural bull market in copper.”
Goldman Sachs analysts raised their 12-month forecast for copper to US$9,500 per metric ton, up from a previous estimate of US$7,500. The Wall Street bank said it now expects a sustained, higher average price for 2021 and 2022. It has estimated copper prices will average around US$8,625 next year, before climbing to an average of US$9,175 in 2022. By the first half of 2022, Goldman Sachs analysts said, it is “highly probable” copper would test the existing record highs of US$10,170 set in 2011.
Demand for aluminum in insulated metal substrates (IMS) and metal backed printed circuit boards (MPCB) continues be driven by the demand for thermal management solutions for high powered LED general & automotive lighting applications, as well as power conversion applications associated with e-mobility charging infrastructure and green energy generation, and all the competing industrial and consumer applications. As demand from these sectors starts to pick-up pace, post pandemic lockdown prices are starting to rise above their pre pandemic levels, introducing price pressures to the supply chain.
High demand for epoxy resins for green energy applications (wind turbine blades) in China, coupled with recent industrial accidents at volume resin manufacturing facilities in China & Korea has led to shortages and significant (60%) price hikes for CCL manufacturers in the last two months. The impact is mostly felt in standard (130-135oC) Tg FR4 laminates & PP production costs and has already fed through to December 2020 price increases of 15-20% at the factory gate. These increases will be felt in Europe and the USA from early Q1 2021 as inventories in these markets are replenished with higher cost stock. Upward price pressure has also been building for Mid and High Tg phenolic cured FR4’s since the end of August 2020. The cumulative effect to date is around 15-20%, which will equate to 5-10% increases for CCL & PP in early Q1 2021.
High growth in consumer and green energy applications is also pushing up glass yarn and glass fabric prices and limiting availability, particularly for heavy weight fabrics such as 7628 and 2116. Glass fabric manufacturers tend to follow the demand for those materials which have lower quality demands and command higher market prices, than those demanded by the PCB industry. The CCL manufacturers expect that this trend will cause laminate shortages, particularly for rigid materials. High year-end enquiries and order levels in Asia are always a solid precursor of both availability limitations, and significant price increases in early 2021. This has already been confirmed by market price increase warnings issued by the global market leaders in rigid CCL production.
Supply chain logistics are another cause of concern as demand picks up post pandemic lockdown. There are significant capacity constraints affecting the availability of both sea & air freight. Market data shows that air freight demand is close to returning to 2019 levels, but the available capacity is down by 24% due to the lack of passenger flights. Price levels are down from the early pandemic highs of 4-5X pre pandemic rates. However, the price trend is upwards from summer 2020 levels of 1.5X pre pandemic rates and currently sitting at 2-2.5X pre pandemic rates due to very high seasonal demand. They are expected to remain high in 2021 and until a significant increase in passenger air traffic increases available cargo capacity.
For sea freight demand is high due to a post pandemic lockdown rebound in demand, leading to two major issues: a shortage of both dry and refrigerated containers, and a high differential in pricing on Asia to Europe / UK and Asia to USA shipping routes. This differential towards more profitable USA routes is driving up prices for container traffic between Asia and Europe/UK, and freight rates to the USA are already very high.
Source: Ventec International Group
Any comments on logistic pressures would of course not be complete without some mention of BREXIT. Congestion at UK ports is already building prior to the UKs departure from the EU at the end of December 2020. This is leading to non-negotiable congestion surcharges, which for now can be absorbed to some degree, but with other price pressures building, if they continue for the long term, they will need to be passed on to customers. Additionally, inland transportation costs are increasing as the number of available drivers and vehicles for moving containers from port has reduced as continental drivers return to mainland Europe ahead of the UKs 31st December 2020 departure from the EU.
Today more than ever, suppliers that own and control the complete supply chain of PCB materials including laminates, and prepregs from end to end, have a clear advantage. Maintaining carefully managed inventory in various locations worldwide gives the flexibility to adapt to these unforeseen events outside normal control, such as pandemics or industrial accidents!
Building a supply chain capable of handling the challenges we all encounter - those we can control and those we cannot - is ultimately dependent on the quality of dialog between supplier and customer. The more we can work together, and establish those close, strong, and enduring relationships to the benefit of all parties involved, the easier it will be to navigate these challenging times.
About the author: Mark Goodwin, COO EMEA & Americas, © Ventec International Group
CCL & PCB | Lithium Battery | Total | |
2020 YE Capacity | 549600 | 283000 | 8326002020 |
YE Demand | 545000 | 255000 | 8000002020 |
YE Utilisation | 99.16% | 90.11% | 96.08% |
2020 | 2025 | 2030 | |
Requirement (Gwh) | 62.4 | 322.1 | 1097.3 |
Copper Foil Requirement (T/Year) | 56,160 | 289,890 | 987,570 |
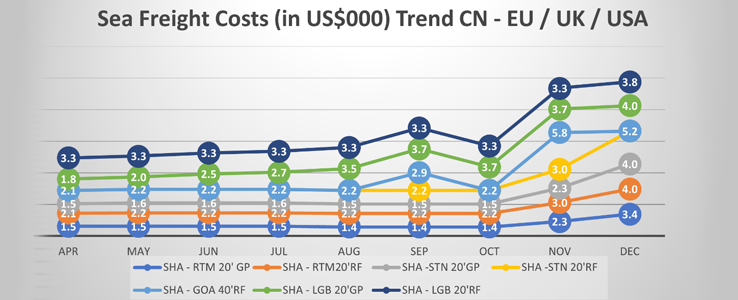
About the author: Mark Goodwin, COO EMEA & Americas, © Ventec International Group