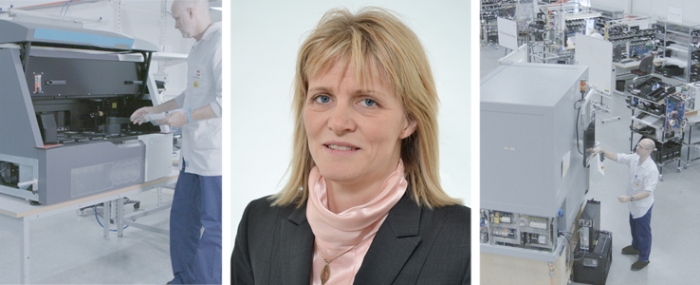
© Sanmina
Electronics Production |
Optimising sourcing strategies during COVID-19
If this pandemic has taught us anything, it is that a secure supply chain is paramount for a continuous business operation – maybe it's time to look over those sourcing strategies one more time.
By Charlotta Linnell
When the COVID-19 pandemic first emerged last winter, it had a profound impact on the supply chain. Regional lockdowns and grounded flights extended the delivery lead times of materials from 5 to 15 days. Freight capacity to deliver materials was cut in half. OEMs had to pay expensive premiums to get materials and products delivered on time. While it’s not the first crisis to affect the manufacturing industry, it is certainly one of the most major events due to its unpredictability, global reach and duration. As a result, many European companies are taking another look at their sourcing strategies to balance short-term cost savings with reduced risk over the long term, while improving the agility of their manufacturing programmes.
Re-Evaluating Best Practices
European governments and companies are examining strategies implemented ten years ago, which included low cost manufacturing in Asia, and are now considering the benefits that could be gained by manufacturing in Sweden or other European regions. In the electronics manufacturing sector, for example, the main cost during production is related to materials. With smart manufacturing approaches and well designed products, manufacturing closer to home doesn’t necessarily have to come at a higher cost and can provide additional benefits in terms of improved agility and control.
Aspects that OEMs should consider as they evaluate their business models include:
Total cost of ownership. In addition to product price, elements that must be factored into total cost include component lead times, manufacturing cycle times, how flexible a supplier is in delivering the parts within a lead time, lot size and transit time. Another important aspect of total cost of ownership is the price of working with a supplier in another region. Long distance relationships involve language, time zone and cultural barriers which can make immediate and clear communication more challenging. Travel is time consuming and costly. It was also one of the first activities to be put on hold during the pandemic. While it’s not impossible to overcome these challenges, switching to local alternatives can give companies more control during a crisis.
Risk mitigation practices. Because forecasts during a crisis like this pandemic can lack visibility, OEMs should consider sourcing for the long term versus just-in-time inventory models. Early on in the pandemic, many organisations around the world were rushing to obtain the same material at the same time due to lack of inventory. For some OEMs, reducing risk could mean holding a higher amount of inventory on their premise or moving manufacturing operations closer to home base, in order to increase flexibility. For others, paying a reasonable insurance premium that reduces risk over time could be the right approach.
Close and transparent collaboration. OEMs that work closely with partners, suppliers and customers are better equipped to navigate unforeseen events. During emergencies, an EMS provider can tap into strong supplier relationships to obtain materials more quickly, while continuing to meet production requirements. Some EMS providers are also working closely with customers on product design, freeing them from much of the legwork so that they can focus on product innovation. With this deeper level of involvement comes a responsibility for EMS providers to be transparent and open, sharing all documentation regarding product designs, product changes and manufacturing processes.
Virtual tours. Vital business practices such as factory tours and supplier selections can now move to the virtual arena, with live presentations and negotiations to efficiently conduct business when travel isn’t possible. Virtual meetings can be tailored to ensure the most relevant information is presented for key stakeholders that want a look inside a factory and allow the presenter to reach a broader audience of decision makers. While some face-to-face meetings will always be important, reducing the frequency of in-person visits also positively impacts the environment.
Digital platforms. EMS providers that leverage digital platforms such as a cloud-based manufacturing execution system (MES) can provide improved visibility, transparency and real time data on supply chain activities. In just a few clicks, stakeholders can view complete supply chain information, all the way down to raw materials. Having access to detailed production data - such as the particular tool used to build a product, test data or component traceability records - enables more informed communications with customers. Having access to one IT and quality management system also connects different regional factories, providing a bird’s eye view into inventory and production. If one region must shut down, production can be continued in another region.
Improving Agility and Control
COVID-19 is a significant event that will have a lasting impact on the way that manufacturers, suppliers and partners work together. It has presented an opportunity for OEMs to re-evaluate the old way of working and determine how the supply chain can work differently to most effectively meet sourcing challenges in the future. While the public sector is more reluctant to change, the private sector is eager to challenge the status quo that has dominated over the past decade and learn from recent mistakes, so as to not repeat them again. This doesn’t mean that all of today’s strategies are irrelevant, but evaluating them in advance of another potential global crisis is paramount. Moving forward, successful OEMs will be the ones that continuously optimize supplier relationships, resources and technology to support their immediate and long term requirements, ensuring agility and control during times of crisis.
About the author: Charlotta Linnell is Business Development Manager at Sanmina, with more than 20 years of experience working with original equipment manufacturers (OEMs) and electronic manufacturing services (EMS) companies in the Nordic region. Charlotta has a strong track record for providing component sourcing, supply chain design and manufacturing solutions that support the development of complex products and systems for the medical, industrial and telecommunications industries.
About the author: Charlotta Linnell is Business Development Manager at Sanmina, with more than 20 years of experience working with original equipment manufacturers (OEMs) and electronic manufacturing services (EMS) companies in the Nordic region. Charlotta has a strong track record for providing component sourcing, supply chain design and manufacturing solutions that support the development of complex products and systems for the medical, industrial and telecommunications industries.