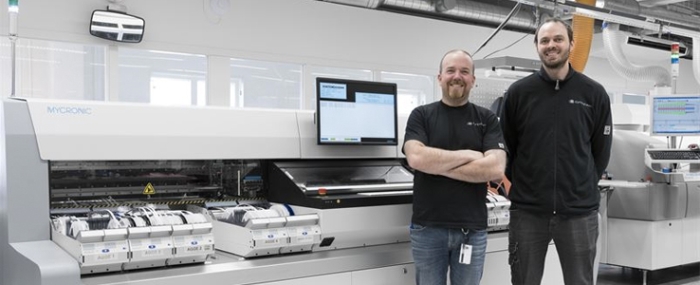
© Optronic
Electronics Production |
Optronic investing in latest technology from Mycronic
With the investment in a more modern surface mounting machine, Optronic has opted for more efficient manufacturing and higher quality. Two major gains with deciding power in the investment process.
“This will produce good results, so it clearly feels like a step in the right direction,” says Samuel Westermark, Production Manager for Electronics Production at Optronic.
In 2019 Optronic made some major investments that were quality enhancing for the PCB line. A premium model of screen printer from Ekra was ordered and installed – a combination machine with automated dispenser that yielded good results.
At the same time, a total renovation of the furnace was carried out which was also of great importance and now Optronic has made the next investment decision that will be of great benefit to the entire operation, a press release states.
A surface mounting machine, MY300, from Swedish manufacturer Mycronic has been delivered. With it, the oldest of the two current models we have installed will be retired after a long and faithful service.
“We are making the investment to continue to ensure the quality of our products and be as reliable as our customers expect us to be. Instead of waiting for the end of the older machine, we work proactively and thus secure our customers’ orders,” says Samuel Westermark.
“There will be no downtime with two mounting heads. This will produce good results with reduced run times, not least on those batches where we have higher volumes,” says Samuel Westermark.
One interesting detail is that Optronic - in turn - has also been a supplier to Mycronic as it manufactures all cameras for Mycronic surface mounting machines.
“Mycronic is a major manufacturer and in my opinion is the leader in the ‘pick and place’ machines segment; they have professional technicians and offer a very good service. This investment ensures that we can maintain high-quality PCB manufacturing for another decade,” says Samuel Westermark.
Since the new and the older machine are from the same manufacturer, integration will be seamless.
“When we get new components, we need to train the machines, and in the new process the process is automatic in a completely different way than we are used to, which makes us more efficient in prototype production. We are working hard to shorten lead times so the throughput time on the prototype will be faster,” says Samuel Westermark.
“It feels fantastic. Although it is a big investment, I feel that we get a lot for the money because it will be a boost for the older line as well – it can’t get much better than that.”