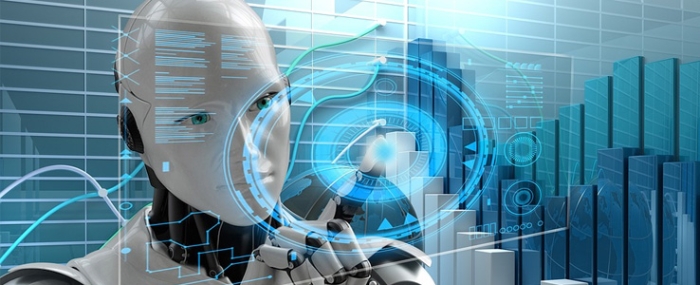
© Pixabay
General |
Putting artificial intelligence to work for industrial operations
By now, we are all familiar with the concept of Industry 4.0, a popular business model that enables manufacturers to become faster, more efficient, and more flexible to respond to inevitable market changes.
While traditional approaches to factory automation continue to be successful, they are often focused on specific production operations, leaving the critical operational level decision unaddressed or at best, open to interpretation. If we don’t get to it soon, someone else (or something else) will do it for us, and it may not be a human.
Will Industry 4.0 Make Further Investment in Automation Viable?
Author: Michael Ford, Sr. Director Emerging Industry Strategy at Aegis Software
Looking at the global Manufacturing industry’s model for product creation and distribution, we seem to spend more effort in today’s world on moving products around the globe than on actually manufacturing them. This amounts to a significant waste of financial and environmental resources. A futuristic model has been proposed where factories could supply their products on demand to a comparatively local market, causing money that was originally spent towards finished goods, shipping, and taxes and duties to instead be invested in automation and the local human workforce. As automation is gradually introduced, production costs would decrease over time as any tasks that require costly human resources are replaced. A compelling business plan that targets local manufacturing translates to factory capacity that will expand to meet increased demand. As expansion occurs, more human resources are required, creating an ideal balance for the humans involved, as they both retain their jobs, and can also enjoy more varied and more “skilled” responsibilities. With this win-win manufacturing model, it sounds like we have arrived at the “factory of the future”, right? Unfortunately, there’s a critical flaw in this plan, one that has remained elusive since the beginning of complex automation. The issue can be illustrated by looking at Surface Mount Technology (SMT) lines, where components are placed onto a printed circuit board. Though the task seems simple enough, the complex nature of programming and setting up materials on these types of machines has created some legendary challenges in the areas of productivity maintenance and equipment utilization, especially as manufacturers have increased their product mix. Conceptually-similar types of automation are now being applied to mainstream assembly manufacturing, and this provides some valuable lessons from which we can learn. When looking across an SMT shop-floor, your first impression tells you exactly what you need to know about the factory’s business operations. Each SMT machine has a light tower to indicate when the machine has stopped. Assuming these lights haven’t been disabled, you can simply count the number of red lights across the floor and compare this to the total number of machines for a reliable indication of the degree of product mix. In a high-mix scenario, SMT machines typically sit in their “setup” phase for up to 80% of the time, leaving only about 20% of the time to actually make product. This may seem a bit exaggerated, but in reality, in many cases, the added value is just half that. Clearly, the enemy of production automation is change. Over the years there have been some great technologies developed for these machines that reduce the time required for set-up and tear-down between products, but there are always hidden compromises. For example, rather than set up a unique set of materials for each consecutive product, you could set the materials common to each product in common locations which would reduce or eliminate the time needed for material setup; but the location of materials is also a significant factor in machine program optimization, which could severely impact the throughput performance since it has to travel further to pick up common components. Another example would be using removable carts of materials that can be slotted in and out of the machine, with setup changes taking place in a separate staging area. Unfortunately, the cost of the trolleys, feeders, and the significant impact of duplicate material requirements translates to a situation that’s more expensive than the down-time it’s trying to prevent. These are just two of the simpler trade-off scenarios related to material setup time and throughput efficiency. When you consider machines with multiple heads, stages or lanes, the situation becomes even more complex. The amount of engineering intensity that must be dedicated to the machine software to correct these issues has risen exponentially in recent years, with customized and complex algorithms from machine vendors attempting to handle whichever product combinations are thrown at them. This is reflective of a day-to-day challenge that many manufacturers face when trying to optimize their automation for highly-flexible environments. The situation gets worse. Because SMT production lines are driven by so many different processes, few vendors have true visibility into how the prior machines in the line or the next machines to follow will perform. The line will run only as fast as the slowest process, and bottlenecks will appear and change over time. You can see this effect more clearly when lines are being run continuously with a single high-volume product. Each machine on the line will likely be running at 50% - 95% of its capacity, with just the bottleneck machine running close to 100%, causing substantial inefficiencies. When running high volumes, manufacturers often run into issues when trying to determine how often the line is actually shut down. The rate of completion on any continuous production line will never quite meet the rate needed for the next process and final delivery to the customer. Over-producing creates an excess of intermediate goods or finished goods stock, which can be expensive to retain and manage. The cheaper option here may be stopping the line periodically, even if it isn’t long enough to change the line over to build another product. The consequences of these critical decisions are often concealed from management analysis, as lines are typically measured based on performance versus schedule. If the schedule indicates that the machine won’t need to be used, or that changeover time must be allocated, this “lost opportunity time” is likely excluded from most production reports and statistics. When it comes to managing lines in very high-mix scenarios, taking all of these factors into account explains why the productivity figures that are formally reported are far greater than the real-world machine utilization, which importantly, means that actual performance and subsequent Return on Investment will not be achieved within the expected time (if in fact, at all). Together, all of these issues represent a highly-complex planning environment, which will eventually become mainstream across all areas of assembly as factory automation becomes more commonplace. It may come as a surprise to learn that in the vast majority of SMT factories, the majority of the planning is typically carried out in Excel. There is good reason for this, as traditional planning tools have two fundamental flaws. First, they do not have awareness of the shop-floor situation in real time, so they are blind to the current and historical status and performance. Second, these generic planning tools don’t have enough knowledge of the individual processes to reliably know the machines’ expected performance, given the exact products and mix of products that will be produced. Without this critical information, the average processing time per production unit and expected minimum processing time cannot be calculated accurately. Therefore, traditional planning systems are effectively blind and have their hands tied behind their backs. Time for a New Approach – The Digital Factory Whether natural or artificial, intelligence can only work when it’s based on available information. With the recent rise in IoT technologies, such as the IPC’s Connected Factory Exchange (CFX) standard, detailed, accurate, and timely information flows freely across all machines and processes in a factory. This includes the ability to communicate with a modern digitally-orientated MES software that can use this information for planning. In the case of the CFX specification, this results in complete visibility of current and historical performance that can be easily understood. Engineering information, including all tools and resources needed, and the complete digital product-process model can be exchanged. This unprecedented ability means that the software’s “eyes” can now be opened and its “hands” untied. In the new digital factory approach, the use of software is mandatory, as there’s far too much continuous information for any human being to process. Software geared for the digital factory takes this continuous data and converts it into actionable pieces of information. We are already seeing that the more advanced MES solutions on the market make use of data streams from the shop-floor, creating value by making the performance and status of the operation completely visible. This includes indications of constraints, and the potential effects and consequences of any considered change, such as when a new order arrives at a factory and a practical delivery commitment must be made. As more and more processes eventually adopt a common communication standard such as CFX across assembly, the more dependable and effective these software algorithms will become. Steps Towards the Birth of Manufacturing – Artificial Intelligence As the availability and quality of digital data progresses factory management software will undergo two main transitions. The first is to reach the critical mass of data so that decisions can now be made without human involvement. Until this point is reached, information is used by the software system to provide digital visibility into performance and opportunity, so that decision makers can make informed decisions more quickly, and take action a great deal sooner. The software considers far more options and variables in a much shorter timeframe than non-digital methods, which means that changes can be made often and with less modifications to the previous plan, which ensures that the operation continues to work in an optimum condition, with a smoother operational flow. In essence, it’s now possible to perform value-stream mapping for the whole factory in real-time. An important factor at this stage is the exchange of data between factory systems. In addition to reporting information such as machine status, progress and issues, the software should also interact with any factory level software, providing expected cycle times and product combinations that the factory-level software is considering. At the same time, there are now opportunities for the machine software to be enhanced to utilize information available from the factory level processes, allowing for more advanced optimization algorithms for programming. The next transition comes with the realization of real Artificial Intelligence (AI). In order to get to the stage where human involvement is no longer required for decision making, software algorithms will become increasingly dependable and refined. Each algorithm will work by attempting a variety of different potential solutions for a given problem and measuring each one against a scoring methodology to determine the probability of a successful outcome. With AI, the key difference is that the scoring mechanism itself can be automatically adjusted by the AI technology. AI has the ability to compare real-world effects and trends with expectations, then move on to incorporate additional information that may influence the unexpected effects and trends (that the original algorithms had not considered). In the real world of manufacturing, it is critical that the AI is given the benefit of recorded “experience”, accumulated through the development of the initial algorithms, at the time it starts. Then, the AI can kick off at least as well as the algorithms performed prior to the AI modification. In terms of the shop-floor experience, the transition to using AI is therefore not such a big step. Artificial Intelligence – The Digital End-Game As depicted in many popular Sci-Fi movies the introduction of an AI certainly won’t be the end of the story. Having now created a digitalized factory run by an AI, humans will continue to expand the scope and reach of the technology/technologies for even more benefits in their factory operation. This includes applications in their supply-chain, where materials orders, deliveries, and logistics are managed by the AI. It also includes quality management, where the circumstances that lead to a defect can be quickly assessed, so as to create an immediately effective form of active quality control. Artificial Intelligence may also be used to manage resources, including people. Rather than simply assigning production operators to a single repetitive task, the AI can dynamically manage their time to provide a far more flexible support model for the factory. For example, this may include some complex assembly, followed by quality control, then helping with a material issue, or performing machine maintenance. As AI can provide the scheduling and technical data associated with each task (most likely enabled through Augmented Reality technology) this contributes added skill, diversity, and creativity for production engineers and operators in their day-to-day jobs. In fact, all of this makes the AI-driven digital factory of the future, quite an interesting place to be.Michael Ford, Sr. Director Emerging Industry Strategy at © Aegis Software
Author: Michael Ford, Sr. Director Emerging Industry Strategy at Aegis Software