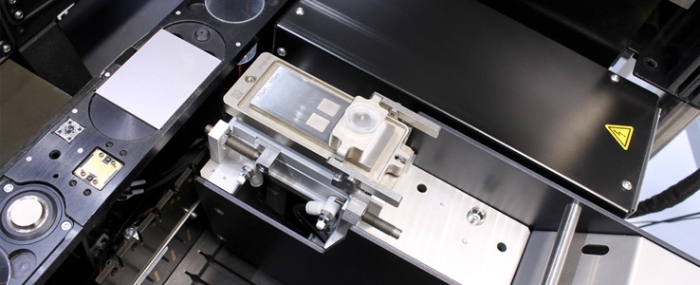
© Essemtec
Electronics Production |
Sensor specialist invests in Essemtec equpiment for Swiss site
The principle in sensor technology is to pack more and more intelligence in spaces that become progressively smaller. Balluff is specialist in high-quality sensor, identification and network solutions.
The Balluff production site in Switzerland evaluated assembly systems, that have to meet the highest SMT production technology challenges when mounting the sensors of today and tomorrow. Fluxing and dipping have become important criteria; Essemtec have supported Balluff in this process, the equipmenmnaker announced.
The pick and place systems at Balluff could not keep pace with the increasing demands. Until recently, the dipping process was addressed with a large-scale squeegee system. But this generated more and more quality problems with components and ball sizes that have become progressively smaller and smaller; so Balluff started a market evaluation.
The focus was on the flux system or rather the dipping station for intelligent micro controllers. Both stencil printers and spray fluxers are no longer eligible in this “micro ball attachment” process, with its high process accuracy demands. The following conditions were laid down:
Balluff decided that only a flex-squeegee system would meet these requirements. Essemtec, together with a partner company, developed a complementary system that can be integrated on a standard FOX pick and place machine. The hardware and software integration were implemented in co-operation with Balluff.
Balluff then decided upon a FOX from Essemtec, with its newly developed flux system. The clincher was that Essemtec presented the most coherent solution during the pre-project and that FOX is suited for such applications, Essemtec continued in its press release.
Technical | Process |
Mounting component types uBGA, FlipChip, CSP, QFN with the dipping method Ball diameter 0,2 mm +/- | Provider must deliver complete system including production safe process. |
Component height > 0.0 mm | |
Min. pitch > 0,3 mm | |
Several different components must be processed on the same circuit in relation to the dipping process. | Varying dipping depths must be run simultaneously. |
Balluff specific medium | Balluff certified |
Flux height of the ball: 1/4 - 2/3 of the ball diameter | Flux height must be +/- 5 μm exact |
The flux nests have to be exchangeable. The machine must automatically detect over a coding if the accurate board is used. | Process interlock |
The fluxer can be used like a feeder. The machine and the machine construction must be designed in a manner that no vibration is transferred to the flux feeder. | Easiest integration of the dipping process on a standard pick and place machine. |
The dipping nests must be clean and must be filled without medium washing outs. | Especially the milling resistance in connection with the flux process has to be examined and optimised within the squeegee process. |