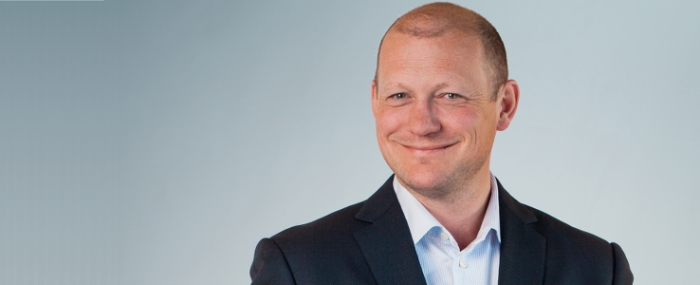
© elmatica
PCB |
Price development of PCBs from 2007 to 2017
This article will analyse the price development of Printed Circuit Boards (PCB) from the People's Republic of China (China) from 2007 to 2017, though the analysis is applicable for many non-standardized electronic components from China.
China is expected to be the main manufacturing country of PCB for the next five years and a separate paper will analyse the projected price development for 2017-2022.
A PCB is a unique customer specific commodity and in order to optimise data coherency and allow this analysis to address the major price trends of Chinese PCB manufacturing, the PCB technology selected for this analysis is 2-4-6 layers, volume production with standard material, stack up, solder mask and 35um copper thickness.
The two main cost drivers of PCB, namely labour and material costs will be addressed in this paper. An analysis of how these drivers has affected the profit margin of PCB manufacturers in China from 2007 to 2017 will be presented. The findings will be used in the next paper, which will predict the price development of PCB from China for the next five years.
Labour
The central government of China has steadily increased the level of minimum wage from 2007 to 2017 (please examine graph “China Minimum monthly wages”) and the increase has also been higher in financial pressure areas as e.g. Shenzhen and Shanghai. The increase in minimum wage affected the labour cost for trades and industries who require skilled labour at an higher extent. The wage level for experienced and educated operators in the PCB industry, has therefore been affected above average. The majority of the manufacturers are located in financial pressure areas and a significant part of their workforce are trained and educated operators so the total labour cost increase effect is significant.
In regard to manufacturing in Asian countries as India, Malaysia, Thailand and Vietnam this is not included in this paper, though their PCB production and investments are increasing. Their prices are currently not competitive, unless you place orders with minimum 1700 SQM as their cost competitive advantage is labour, compared to China. Cost of material is higher in these countries, as a significant part of their raw material is purchased from China, combined with increased handling and transportation costs, this practically ensures that their material costs are higher than Chinese manufacturers. The competitive advantage of reduced labour cost in relation to increased material costs are therefore currently financially viable for orders of minimum 1500 SQM with an estimated total PCB price reduction effect of 4-8%.
A strategy towards implementing automation to reduce labour intensive operations began in China in the early 2000. This was brought forward partly due to the one child policy, aging population, increasing wages and the government strategy towards building a stronger consumer based domestic market. The overall productivity effect of automation since 2000 is estimated to be in the area of 70 % (please examine graph “China Productivity Growth at 16-Year Low”) and this has decreased the overall effect of the wage increase. However, data indicates that the effect of this strategy is decreasing and we can hence expect that the overall labour cost of producing PCB will increase at a higher rate in the near future.
Material
The commodity price index depicts a price increase over the last 24 years (please see “Selected Commodity Price Index”), however this data does not encompass the substantial increase in commodities in 4 quarter 2016. The question is then, is this a temporary fluctuation and will this affect the price of finished goods? The key manufacturing entities in the market has reported that they have significantly been pressed on price over the last 5 years, to the extent that they are forced to pass the increased costs of material to the product owners in 2017. It is expected or at this stage it is evident that the price of copper foil due to material shortage will be the first material in PCB to increase in price and resin will most likely follow shortly thereafter.
What caused the copper foil shortage?
Copper foil is used to produce both Copper-Clad Laminate (CCL) and Lithium batteries. The global copper foil productivity is limited, but with the increasing demand from electrical vehicles, more and more copper foil are used to produce Lithium batteries and less is allocated for the CCL and the PCB industry as the quality demand is higher and the profit margins are lower in this industry. In recent years, the copper foil industry has also competed fiercely, this has resulted in diminishing return on investment and some copper foil manufacturer has been closed down, which results in a further decrease of supply and CCL manufacturers can now not keep up with the increasing demand.
The global copper foil manufacturing capacity is app. 480,000 tons per year (t/y), which is less than the current total demand 516,000 t/y, including CCL and PCB which is 25% of the total capacity. Some experts predict a sharp increase in the demand for electric vehicles due to pollution and technological breakthrough and this will further stress the supply situation for copper foil. By 2018, the demand of Lithium battery copper foil is estimated by some to increase by 200% - 300% and the copper foil industry is presently expanding output and productivity by 4% - 5% per year. It is evident that if this scenario becomes a reality the demand and price situation will be quite challenging.
Conclusion
Labour cost is increasing, automation is no longer providing the necessary productivity gains, material is scarce, material demand is growing and material supply is not increasing at an equivalent rate (please see graph “PCB production and Market price Index 2007-2017).
The profit gap (PCB market price - PCB Production Cost) for manufacturers in China for PCB technology with 2-4-6 layers, volume production with standard material and stack up, solder mask and 35um copper thickness has decreased substantially over the last two years, as labour and material costs has increased. The expected result is hence that prices will increase in 2017 and it is not evident when and at what price level the new equilibrium will be found.
-----
Author: Didrik Bech, CEO at © Elmatica
EDITOR'S NOTE_ The article continues after the slider.