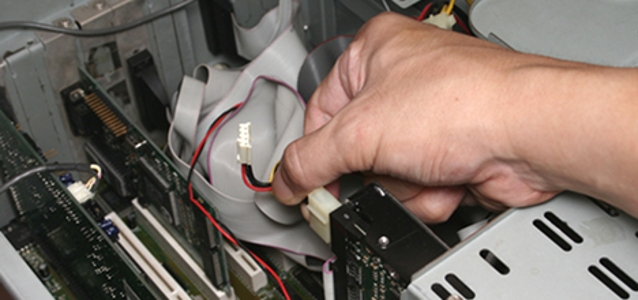
© photong dreamstime.com
Analysis |
Where is the printed thin film transistor technology now?
Today we have all manner of electronic components being printed including batteries, interconnects, energy harvesters, photovoltaics, antennas and memories.
In many cases the performance is not as high as their non-printed counterparts and therefore businesses are leveraging their other set of characteristics, including potential for low cost, large-area coverage and flexibility.
"Transistors are a vital piece of technology in the emerging toolkit of printed electronic components. They are critical because they enable logic and therefore data processing. In some ways, they are the linchpin that brings printed systems together.
However, transistors are complex. They are multilayer devices that require intricate patterning or layer-to-layer registration. Interfacial properties are also very critical and many parameters must match in order to achieve a high-quality conduction interface with a low density of defects.
In the remainder of this article we will assess the major market drivers for printed transistors and outline the latest status of the technology. We will finally argue that the technology push will not work in this arena, and that companies will need to start with simple product concepts."
Major market drivers for going printed
The primary market drivers for printed electronics are cost savings and large-area. The potential for cost savings stems from the fact that printing is an additive process. This means that the material is deposited only where it is required. Ideally there are only two steps between a bare substrate and a working functional layer on a substrate, and those are a direct printing process and a curing step. The primary material set required is only a functional ink. This is schematically shown in the figure below.
This is in stark contrast to photolithography-based subtractive methods used in the industry. A subtractive method consists of multiple steps and therefore has a very long value chain. In other words, there are numerous steps, materials and equipment pieces that are needed to produce one layer on a bare substrate.
The process also consumes materials that do not end up on the final devices. Examples include photoresists and etchants. Numerous equipment pieces are also required that would be made redundant when printing is used. For example, spin coaters, masks, photolithography machines, dry etchants, wet benches, etc would no longer be required.
It is therefore evident that printing has the potential to simplify the process flow, shorten the value chain and increase the material utilisation. All these factors can lead to cost savings compared to photolithography-based techniques, particularly when devices do not have a high surface coverage on the substrate. TFTs are one such device because they cover a small area per pixel in active matrix areas in order to maintain a high aperture ratio.
The value chain is long and the process consumers and wastes many materials along the way that are ultimately not needed.
The process steps are few therefore the value chain will be shortened and made more compact.
Product concepts should account for low performance
The performance of printed transistors is also below par today. Their mobility is limited to <0.1 cm2/Vs in most cases. Their lifetime and stability are poor and they often need expensive encapsulation layers. Indeed their performance may not yet be adequate today for the obvious target markets of large-sized display backplanes and RFID tags. Yield is still an issue, particularly because narrow feature size and high layer-to-layer registration are required. A low yield means that the potential cost savings are yet to translate into real ones.
Initially, the technology developers will have to design simple platform circuits factoring in the short comings of printed TFTs. The industry has done this once already- the circuits developed for TFTs had to take into account their drastically poorer performance compared to silicon chips. These simple circuits will have to be integrated into final products to generate a cash flow, however limited. The cash flow coupled with the accumulation of production experience will push the technology down the learning curve.
The state of the technology
Today there are numerous semiconductors that can be printed as the active channel of thin film transistors. It is now possible to print inks based on various nanostructures including Si, ZnO, graphene, carbon nanotubes, etc. There are also a variety of organic semiconductors which can be printed or solution processed. Some examples include PQT 12, P3HT, TIPS Pentacene, etc.
There is no clear winner or one-size-fits all solution yet. The basics of the technology base are however here and the details will settle as the technology matures.
The choice, however, is more limited when it comes to dielectrics. Carrier conduction takes place at the interface between the dielectric and the semiconductor; therefore it is the interfacial quality which ultimately determines the device performance. The dielectric also has a major impact on voltage requirements, device lifetime and power consumption. The lifetime is adversely affected by charge trapping into the dielectric and the power consumption by pinholes and defects. The voltage requirements also depend on the dielectric constant and thickness.
The state of technology for dielectric lags that of semiconductors. Today most articles reporting a printed transistor only have a printed semiconductor. Indeed the industry will initially adopt hybrid manufacturing approaches (non-printed dielectrics) due to these complexities.
Conclusions
The basics of the technology base for printed TFTs are here now, albeit with technical challenges and shortcomings. The industry has been characterised by a technology push. Indeed, IDTechEx knows more than 300 companies, organisations and university who are developing the technology base globally.
The critical challenge today lies in coming up with a roadmap of product concepts. This is of course an area in which there are no easy or off-the-shelf answers. Linear extrapolations of technology improvements will not do. It takes genius, creative thinking and good design.
It also takes money and a high risk appetite. Companies are likely to have to vertically integrate. This is because many technology developers are several steps away from the end user in the value chain, therefore it will be challenging to understand or create customer needs.
It will be even harder to cultivate a customer base and form a distribution channel, particularly in markets that are widely different to what they are accustomed to. The cost and profit margins are also likely to be small per sold item making the business math difficult to add up in the short term. This is why companies must take the long view.
The end benefit will be in having a technology for display backplanes with comparable performance to existing solutions but with a lower cost. The day this happens the backplane industry will be transformed and all its existing value chains will be disrupted. New players will emerge and old ones will be pushed out. The ultimate prize is enormous, but it takes courage and risk-taking to make the bet.
-----
Author: Dr Khasha Ghaffarzadeh, Technology Analyst, IDTechEx