The European RoHS (Reduction of Hazardous Substances) directive prohibits the use of lead, cadmium, mercury and chromium(IV) compounds in the production of printed circuit boards. This directive has been transposed into European law and will be binding as from 1 July 2006 for the production of electronic modules.
For the circuit board producer this means changing over from the classic hot air solder levelling (HASL) process to lead-free alternatives. From the technical viewpoint, the HASL process has so far failed to meet SMT and COB requirements for plane surfaces due to the uneven tin/lead surface.
These new requirements mean that it will be necessary to provide alternative surface finishes for circuit boards. These, as stated, will need to satisfy the requirements of the current environmental directives, be suitable for modern component insertion methods, yet also be stable under heat, so as to be compatible with lead-free solders and appropriate soldering processes.
Basically the following lead-free surface finishes may be considered for circuit boards:
- HASL, hot air solder levelling
- OSP, organic copper passivation
- Chemical nickel / immersion gold
- Chemical nickel / chemical palladium / immersion gold
- Immersion tin
- Immersion silver
- Electrodeposited tin
Trend: surface finishes for circuit boards
2003 | 2007 |
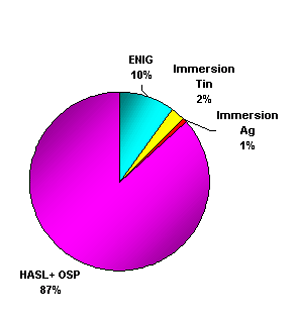 | 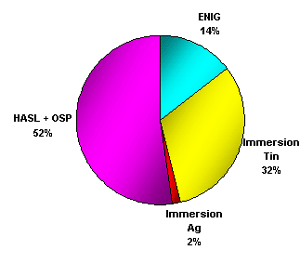 |
fig. 1 and 2:
Trend estimation - Europe, surface finishes for circuit boards
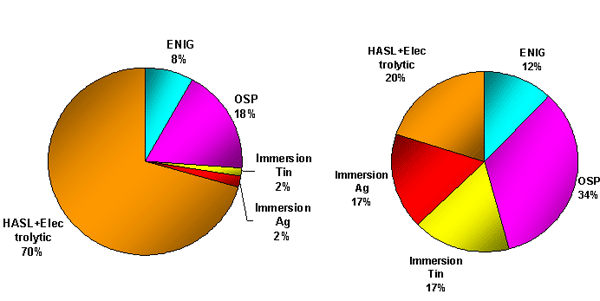
Fig. 3 and 4:
Trend estimation - worldwide, surface finishes for circuit boards
According to trend estimations, application of HASL and OSP surfaces in Europe will decline from approx. 87% (2003) to 52%. Immersion tin is expected to increase from 2% (2003) to 32% (2007). On a global scale, the distribution of surface finishes is forecast for 2007 as follows: HASL 20%; OSP 34%; Chem. Ni/Au 12%; Immersion Ag 17%; Immersion Sn 17%.
Of the possible surface finishes for circuit boards given in the overview, RUWEL AG can offer:
HASL, OSP, chem.Ni/Au, Immersion Sn and Immersion Ag, and also has experience with chemical nickel / chemical palladium / immersion gold. The process provides good surfaces that are solderable and bondable, but the high cost of electrodeposition and low market acceptance argue against its use. What argues against using the "electrodeposited tin process" is that, after etching, the conductor edges are not protected and that tin overhangs from the etching process can break off.
HASL - hot air solder levelling
After the HASL process the circuit boards are coated with molten solder on a tin/lead basis. The plant at the Geldern factory is equipped for using lead-free solder. However, uses of the HASL surface are limited due to the uneven distribution of the coating thickness. It is unsuitable for SMT and bonding methods.
OSP - copper with organic passivation
Continuous horizontal lines are available for coating with this process. OSP surfaces are not bondable. For temperature sensitivity reasons, multiple soldering should be carried out in a nitrogen atmosphere. It is suitable for lead-free soldering.
Chemical nickel / gold
This surface is suitable for Al-wire bonding and is also compatible with lead-free soldering. Coating is carried out in automatic basket plating lines.
Immersion silver
Due to low demand, we do not operate a plant for coating circuit boards with immersion silver. The process has been tested and shows good solderability also in regard to multiple soldering using the lead-free soldering technique.
Immersion tin
Tin as a lead-free surface finish for circuit boards is accepted by the electronics industry and classed as an alternative to the HASL process. Initial problems with whiskering have been tackled and solved. The tin surface is suitable for multiple soldering using lead-free technology. A minimum coating thickness of 1 µm Sn is required for the lead-free method. The coating is applied in continuous horizontal lines (see Fig. 6).
RUWEL can guarantee the solderability of immersion tin coatings after a one-year storage period provided the following criteria are met:
Storage conditions: temperature: 23°C ± 2°C; relative humidity: 50% ± 6% Coatig thickness: 1µm Packing: hermetically sealed vacuum packing
The storage conditions are in conformity with DIN 50014-23/50-2 (storage of circuit boards in a standard atmosphere).
Summary of properties, surface finishes
| Chem. TIN | Chem. SilVer |
Behaviour during soldering | Completely homogeneous bonding with Cu. | Homogeneous bonding with Cu, when coating thickness in specified range. |
Storage life of bare boards | 1 year, given initial coating thickness of 1µm. | 6 months. |
Corrosion resistance of bare boards | Very good, better than HAL, no hermetically sealed packing needed. | Moderate, boards tarnish in presence of sulphur compounds. Hermetically sealed packing required. |
Corrosion resistance of unsoldered surfaces after soldering | Very good, better than HAL, no tarnishing or spotting out. | Poor, unsoldered surfaces tarnish brown/black. |
Whiskering | Technologically non-critical level, but concentration of the anti-whiskering addition needs to be monitored. |
|
Electromigration | Not observed. | Stopped by organic additions in the silver coating. |
Behaviour during multiple soldering processes | Wetting rate remains high. Since surface forces change due to formation of tin/Cu phases, solder spreading decreases in follow-on processes. | Wetting rate decreases. |
Nitrogen in reflow soldering | Nitrogen not necessary when component surfaces and solder paste are suitable. | Reduces surface tarnishing, higher process reliability in case of multiple soldering. |
Solder resist | Good chemical preparation or mechanical brushing of the copper surface required. | Not so aggressive as chem. tin, more tolerant in case of solder resist processing. |