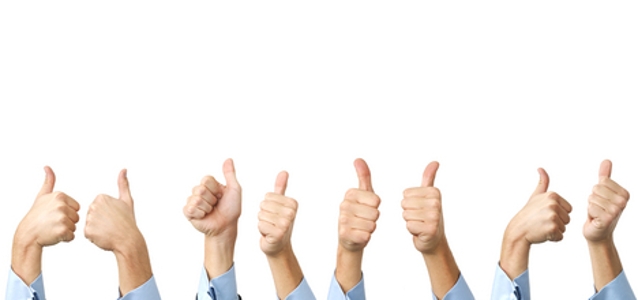
© yuri-arcurs-dreamstime.com
Electronics Production |
BTSR depends on Juki for efficiency
Italian EMS-provider BTSR International, based in Milan, has invested in Juki's storage management system ISM in an attempt to amp up the company's production efficiency.
Massimo Rossetti, quality manager of BTSR, specifies the situation as follows:
“Before we started to work with the ISM storage management system we (BTSR International S.p.A.) kept all SMT material in a separate raw material store. Our stock employees were responsible for the complete material flow. Because they were insufficiently trained in the handling of electronic components problems occurred again and again. After the implementation of two towers (with drying module) and a drying cabinet the SMT material was stored directly in the production area and was supervised by experienced electronic technicians. The clear effect was that fewer mistakes were made during the application and storage of virgin material.
Previously, to transfer the material to production it was packed into boxes. Once it arrived there the operators had to search exhaustively for each code and then sort the reels for setup.
Since the change to the ISM storage system the material is always ready on-site and search operations of any kind are omitted. Furthermore one perceives that the software was developed with large practical experience of the electronic market. During production planning the software gives us a reliable predication whether all needed components for all planned production lots are available. A clearly presented report is swiftly issued for any missing components.
With the installation of the ISM storage system in the narrowest of spaces we could reduce our SMT storage area by 70 %. We could place the whole SMT stock in the production area and create a lot of space in our raw material stock area. Furthermore we have completely dissolved our transit stock (setup preparation) in the production area.
We also recommend the application of the ISM humidity sensor. At the beginning we declined it, because we had no humidity sensitive components in use. During our summer vacation in August 2012 our air condition in the production area failed because of a malfunction. Over this period the air humidity increased enormously. After production restarted we noticed that 10-15 % of our LED (class 3) failed at test. Therefore we upgraded our ISM storage system with the optional drying units. Afterwards we had no more component failures.
Even from the marketing point of view the application of the new intelligent storage system has a very positive effect. Since we’re an internationally operating company many customers visit us. Because of the clean storage and the well structured material flow our customers can immediately see that we assemble high quality products.
At the time we decided in favour of the ISM for the following reasons:
The storage systems are especially conceived and appropriate for SMT material
- High reduction of required storage space
- Upgrade possibility with drying units
- Many reference customer who have installed systems
- Component storage in boxes