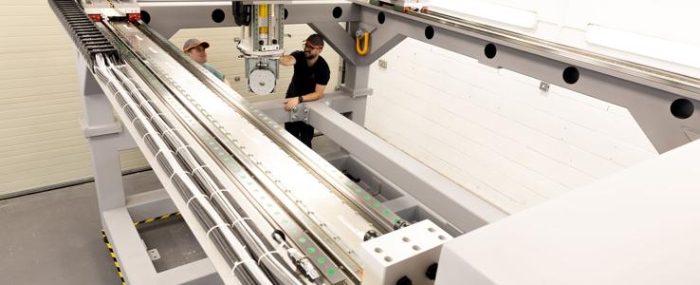
Q5D integrates its largest wire harness automation robot
British developer of tools for the robotic wiring harness manufacturing industry has announced that it has obtained the key components for its largest automated wire harness automation bot.
The Bristol-based developer has acquired the core frame structure and drives to build its largest automated robot to date. Q5D Technology is expected to begin the assembly of its largest wire harness automation bot to date, with the brand-new SQ25W bot expected to enter service in the late spring of 2025.
Once assembled, the machine will allow Tier 1 contractors and manufacturers in the auto manufacturing industry to slash wiring space, reduce costs, and mitigate errors on the assembly line. Another key benefit is that by incorporating more onshore manufacturing, the automotive industry can minimize its exposure to global supply chain issues in an increasingly volatile global economy.
Additionally, the robot will reduce the amount of factory space required for the manufacture of vehicles. It’s also expected that the exact cost reductions will be around $200 on the conservative side. This could translate into billions of dollars in savings for high-volume manufacturers worldwide.
The SQ25W is primarily designed to create larger wire harnesses for vehicles. Currently, vehicle headliners face significant space restrictions to accommodate everything from sensors and internal lighting to noise suppression technology and infotainment. By turning to this robot cell, the process becomes a drop-in replacement for existing designs, making the transition for auto manufacturers seamless.
Although the SQ25W isn’t a new technology, it significantly advances earlier models. It’s almost twice as fast as any previous model, with a positioning speed of four meters per second and a wire deposit speed of one meter per second.
According to Q5D Technology Chief Marketing Officer Simon Baggott, “We’ve been closely engaged with four of the world’s leading vehicle manufacturers and a similar number of their Tier 1 automotive suppliers over the last few years. The SQ25W has been designed in response to their needs. Automation, onshoring, and cost reduction are high on the agenda of these companies, and this new robot delivers all three and more.”
Prospective clients for the new robot can already assess the performance of the SQ25W at the company’s technical assessment center in Bristol, UK. With global supply chain disruptions and increasing import/export costs due to recent U.S. tariffs, innovations like the SQ25W are considered crucial to the future success of the UK’s auto manufacturing sector through onshoring.