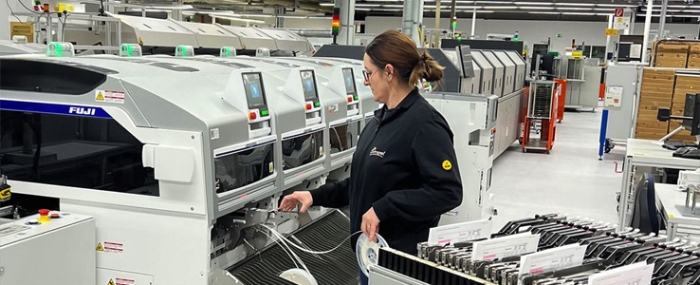
Limtronik upgrade production with new SMD line from Fuji
The EMS industry experiences high volatility due to shorter product life cycles, increased variations, and ongoing miniaturization of components. To tackle these challenges with enhanced flexibility and scalability, EMS provider Limtronik has actively expanded its production capacity by adding a new SMD line.
This line is based on NXT III placement systems and additional components by Fuji Europe Corporation GmbH. As a result, Limtronik has reduced changeover times, increased quality, and enhanced production flexibility.
“Electronic devices are becoming smaller, while performance, quality, and functionality continue to increase. The miniaturization of PCB structures and components requires placement accuracy of ±30 µm. At the same time, we need to remain highly flexible—sometimes producing small batches, other times handling large-volume orders,” says Gerd Ohl, Managing Director of Limtronik GmbH, in a press release.
With the new SMD line, Limtronik has increased its placement capacity. The line includes six new Fuji NXT III placement machines.
“This setup theoretically enables a placement performance of up to 122,500 components per hour. At the same time, there are sufficient feeder slots available to easily handle products with a large variety of components.” Gerd Ohl continues.
The NXT III is described as ideal for placing multifunctional and high-performance electronics, especially when a high-density arrangement of small components is required. The machine features a modular, scalable architecture and supports automated processes, allowing Limtronik to execute projects quickly, even under changing conditions.
In addition to the new SMD line, Limtronik operates three other lines with Fuji placement systems, all equipped with monitoring and traceability technology. A barcode scanner identifies incoming PCBs using their 2D codes before they enter the first placement module. This enables product-dependent, automatic program adjustments and process interlocking in case of deviations.