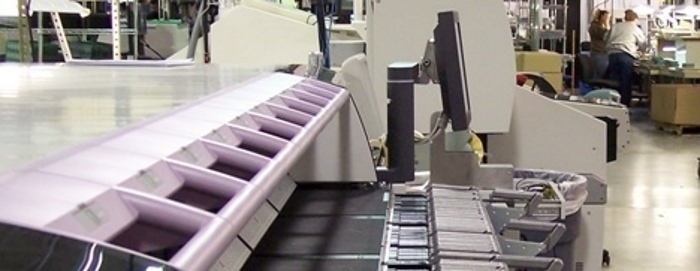
© Assembléon
Electronics Production |
'Why Assembléon's AX-501? It gave us a lot more machine for our money'
Not knowing what their customers will bring next is a fact of life for contract manufacturers, which means they must be supremely versatile. They must be able to place the smallest chip components through to the largest Quad Flat Packs and Ball Grid Arrays.
And they must be able to change production setups quickly for each new product. But, despite the range of circuits passing through, production variation needs to be kept to a minimum: processes have to produce working subassemblies time after time. Quality is at a premium because reputations depend on supplying products that work first time.
Contract manufacturer Z-AXIS (a subsidiary of Video Display Corporation) was established in 1989 to design and manufacture specialty monochrome and color CRT monitors to the medical, industrial and process control markets. It has reinvented itself into being a customer power supply company (Bear Power Supplies) and a high end circuit design and contract manufacture.
Z-AXIS now provides design, prototyping and manufacturing services for complex electronic products and electromechanical assemblies. It specializes in analog, mixed-signal, linear and power design and can design new products or customize existing ones. Growing demand prompted the company to expand its specialty power supply and electronic printed circuit board assembly in Ontario County, New York, USA.
An increasing number of customers are now coming with high-volume production needs. "Many of our product designs last year are now going into high-volume production, often thousands of boards per week," remarked Michael Allen, Z-AXIS' President. "We have installed Assembléon's AX-501 high-speed pick & place machine for those higher-volume jobs to meet customers' shipment release dates".
"Why Assembléon's AX-501? Basically, it gave us a lot more machine for our money" said Michael Allen. "I also like the basic parallel processing philosophy - the machine has 10 standard placement heads between them placing 60,000 chip components and ICs per hour with nice controlled actions. That is much better than a single head having to work at ultra high speeds for the same placement rate. It also means that we can easily expand the machine when we need to - the machine will take up to 20 compact heads, so when needed we can double our production volume from the same machine".
Quality is an absolute requirement
With regular customers like Carl Zeiss Meditec, GE, General Dynamics, L3 Communications, NASA and Raytheon, Z-AXIS concentrates on quality design and manufacture. It must therefore be able to place the latest components for highest board density and functional integration. At the moment, the smallest components Z-AXIS customers have requested have been 0201 chips, but the company is ready for 01005 devices.
Many assemblers are today avoiding 01005 types because of their reputation for poor end-product quality. That is however undeserved - it totally depends on the placement machine. Assembléon's AX-501 places them - along with all the other components - with quality levels better than 10 defects per million components. That has recently been upgraded (even for equipment in the field) to below 5 dpm.
Because so few components are misplaced or damaged, rework costs are a factor 3.5 lower for production lines using the AX-501. That makes a real difference in high-wage-cost areas like the USA and Western European countries, and can amount to hundreds of thousands of dollars a year. It also minimizes the number of defective products coming off the line, so preserving Z-AXIS' reputation for quality - and that is priceless.
Redesigning products can cut costs and add features
One service Z-AXIS provides to its customers is to redesign existing products, which can add features, reduce costs, overcome parts obsolescence, and more. Here, an advanced production line helps add real value. Board packing densities can be increased simply by reducing the size of chip components being placed (these often determine packing densities because boards can hold over a hundred of them). And several older ICs can often be integrated on a single new device.
Z-AXIS has placed QFPs up to 100 to 200 pins and BGAs with up to 400 balls. Both are well within the capabilities of the AX-501. The machine places components from trays and accepts all the major IC types and processes like bare dies, embedded and stacked dies, Package on Package and System in Package. It has up to 260 tape feeding positions. Standard board sizes are up to 515 x 390mm (20.28 x 15.35 inches) or optionally 800 x 457mm (31.5 x 18").
"Another plus for us is that the AX-501 is a very robust machine - we need a machine that is not finicky, and that has long term reliability" stresses Michael. That is essential to help contract manufacture maximize production, and parallel placement helps here, too. Low impact and static forces reduce wear on nozzles, which can easily maintain the same performance for years.
Maintenance and repair is in fact simple for the whole machine. Scheduled maintenance for 100k cph machines is only around 50 hours per year, compared with 300 hours per year (an extra 10 days) for the complex sequential placement machines common in the rest of the industry.
All images: © Assembléon


