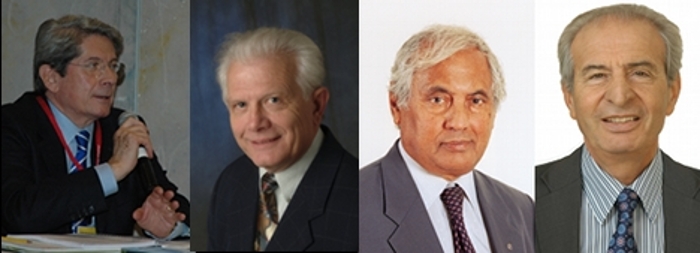
© Data4PCB
PCB |
Europe: Ready for Changes?
The question about the future that the European PCB industry may have and whether Europe is ready for a change prompted Bernard Bismuth from France, Michael Gasch from Germany, Augusto Meozzi from Italy and Rex Rozario O.B.E. from U.K. to write this paper and to try to find an answer.
All four of us have a long working experience in this industry. The PCB is a truly European product as it was invented here by Dr. P. Eisler with whom Rex Rozario O.B.E. worked for a number of years.
We call this paper: 'Europe: Ready for Change?'
Based on actual behaviour of all the actors (politicians, customers, companies, organizations etc.) we are afraid having to state that in 10 years time, the PCB Industry may disappear in Europe. This in turn will create a kind of avalanche effect and will influence many other segments of the electronics manufacturing supply chain.
If changes won’t come into effect fast then our view about the situation in which this industry is in would confirm our pessimism. The PCB has strategic importance as it is a critical component connecting all other electronic devices and has to be assessed as such.
The conclusion of our paper is that this subject is a clear 'Case Study' and example for all other European industries and it shows clearly that things must change in Europe rapidly. We also believe that it is the right time for writing this article as business improved in our industry in 2010 and thus we may gain more time to develop further possibilities and alternatives for preparing a better future.
The state of the European PCB industry:
We have to keep in mind the complete PCB supply chain as it represents about 50'000 people in 1'000 different companies. And these are only the jobs for those people working directly in this industry or supplying this industry. Experience shows that each industrial job in general creates two or three further jobs and, consequently, we are talking of more than 150'000 jobs directly related to our sector.
The complete supply chain embraces not only the manufacturing of PCB but includes the suppliers of consumables, equipment, chemical products, services, software and their subcontractors. Some of these actors still are based in Europe and remain there because they still find a sufficient number of customers and they are exporting their products out of Europe.
A quick panorama of this industry and of the suppliers is presented in the graph shown below:
Details about manufacturing of PCBs in Europe in our study are including not only Europe but as well the riparian countries to the Mediterranean Sea, like Northern Africa, Turkey and Israel, however, not including Russia and countries of ex Soviet Union. This manufacturing base consists of 400 manufacturing shops representing total revenues of around 2'200 million Euros in 2010, employing about 20'000 people for manufacturing and further 30'000 people in support.
About half of the total value is manufactured by about 100 companies based in D-A-CH (Germany, Austria and Switzerland), 150 companies in UK, Italy and France are sharing 25% of the value and another 150 manufacturers are based in the remaining countries and representing another quarter.
PCB manufacturing in all these territories is concentrating on high tech products (multilayer, flex and flex rigid boards) and on a higher diversity of products and smaller volumes.
In 2009 total sales out of own production (viz. excluding any imports) have dropped by 30% versus 2008 but in 2010 we should narrow the gap to 2008 again. The erratic ordering during 2010 in our industry was attributable to the fact that the PCB industry is too far down the supply chain. The nose-diving demand in key industries like the automotive sector had consequences above average to the PCB industry (at first clearance of all stocks and then rapid stock-piling and increase of quantities). This explains as well the closures of important manufacturers in Germany or Italy.
About 20% of all PCBs manufactured in Europe are used in the automotive industry. The industrial sector uses 35%, military and aeronautics account for 10%, communications for 15%, medical for 7%, and the remaining 13% either cannot be attributed to a certain segment or may be found in the consumer and office automation business.
© All images: Data4PCB
In 2009 there have been just 40 PCB manufacturers left in Europe with revenues in excess of 10 Million Euros per year. But these 40 companies represented about 2/3 of the total production value. Only a few of those top companies belong to a larger group and none to an OEM. Therefore, it becomes evident that this business is characterized by independent small and medium companies.
It also becomes apparent that manufacturers in some countries have a higher dependency to a certain industry than others (Germany to automotive, Switzerland to medical, Austria to telecommunications and France and UK to military and aeronautics).
The global market share of European production represents just 6% of all PCBs manufactured (10 years back it was about double that amount). USA today represents 8% of world production (once 25%) and the largest share of about 80% originates from Asia.
Several European PCB manufacturers are importing PCBs from Asia in addition to their own production. This often represents 15 to 20% of their sales figures.
The PCB-industry in Europe can be characterised as a parochial industry as its customers are found in a close circle of perhaps 100 or 200 km around the production site. Export is rare and almost exclusively in the hands of the few big players.
Investments in new companies producing bare boards have come to a halt, only the existing suppliers are increasing and modernising their factories. As a rule of thumb about 8 % of the annual turnover is necessary to remain abreast with the pace of technology. Despite that, only a few companies are able to shoulder this burden. But manufacturing new technologies with old equipment is possible for just a short time only.
Another peculiarity of the industry is that cooperation between companies so far is very rare as one manufacturer sees the other as competitor only. Therefore, cooperation to solve mutual challenges, to serve shared industries or customers normally does not occur. For this reason sometimes several solutions are presented to the market but none of those is able to survive as the critical mass is not reached.
Companies are managed by strong personalities which already have been facing difficult situations in the past. Unfortunately the strategy of many companies consists only to stay alive longer than the closest competitor.
PCB manufacturers are embedded in a supply chain reaching from the design offices to EMS providers. Should the manufacturing part disappear to a large extent, there are good chances that designers and EMS won’t have any base for their business left. This avalanche effect of course will cripple as well all the suppliers to the industry and the loss of industrial jobs in Europe will be much bigger.
This, in consequence, would affect the important manufacturers of equipment and consumables and they may transfer all their activities and research centres which so far served the European PCB industry to other locations. Some segments, like e.g. aeronautics or military are very sensitive to this problem but the damage of the supply chain would apply to the European industry in general.
Our goal is not only to gain support for our ideas outlined in this paper but to defend the interest of this industry and to have Brussels and our governments to support our industry. But also the end users have to understand the importance of the PCB as a critical and strategic component for their own future and competitiveness.
The PCB, a strategic and critical component of electronics
We have seen that business has migrated to the Far East but in case of need always the European manufacturers have been asked to (and have been able to) help. Meanwhile, it becomes apparent that the remaining supply-base in Europe may not be able to do so in future. Far Eastern suppliers this year clearly have shown that they prefer their own local and more profitable markets. They cancelled even long standing relationships with European customers because being too busy. So, the remaining European suppliers enjoyed a rapidly growing business which contributed to the fast recovery of 2010.
The purchasing policy of many companies should be revised as well. At least the total cost of ownership should be taken into consideration. The PCB is not the commodity as it is regarded by many purchasing officers. Quite to the contrary: it is a custom made component that connects all other components in the assembly and actually enables the finished electronic product to function properly. The extensive procedures for approval of a manufacturer are underlining the importance of this product that cannot and should not be compared with bulk products like steel bars.
Other advantages offered by a supplier being close-by are: assistance when developing a new product, efficient cooperation during NPI (new product introduction), speedy help in case of fluctuations in demand, fast help in case of need and attendance for the product until phase-out.
Technical advice based on expert knowledge during the concept-phase can save much more money than the cheap price in a low-cost country.
Designs have become more complex but more often than not they are less than perfect. Any responsible PCB manufacturer has to invest a lot of time to detect flaws and review the data received. Experience and expert knowledge of the staff is an invaluable asset for this purpose. Staff fluctuation in Europe is much less than in Asia thus guaranteeing continuity of a high level of quality.
The ideal group during the concept phase should be a three-member party: the OEM supplying the design, the PCB manufacturer and the EMS provider for the assembly. Such a group was common in those days when OEMs still had deep integration of most – if not all – process steps. Such a group of experts will come up and justify the terms ‘design for manufacturing’, ‘design for quality’ or ‘design for cost, just to name a few. Too often it is forgotten that during the design stage 80 % of all future cost incurred are determined.
All this is reflected in the price of a PCB; however, the value of this precision-product usually is not recognised. It is obvious that the ultimate target for any procurement officer is to obtain a favourable price. However, in many cases it is forgotten that price is only part of the truth but cost is the name of the game. Logistics, buffer stocks, financing, expenses for communication and quality are just a few of the additional items that usually are not considered – not talking about political and legal consequences which may influence the cost of sourcing.
Transfer of production to low cost countries is not only a mean to reduce cost; it is directly linked with the loss of know-how. The idea to move production elsewhere and keep design here is bound to fail as the support of production eventually will follow to the new location. And this in addition is linked with a further risk of losing intellectual property.
Logistics is another potential trap. The eruption of volcanoes in 2010 had their impact on air transport. Diseases like birds flu interrupted production, reduced demand during the financial crisis influenced cargo space available in containers and the frequency of ship schedules. These things all are well known but as long as nothing happens everybody is happy – the abrupt awakening comes only when the case arises and it will have dire consequences to the commercial success of a company.
Lower costs very often are linked with lower standards. Occupational safety, responsible use of resources, ecological awareness are self-evident to us – but in Asia? A company certified according to ISO 14000 should not be proud of this document if the difficult side of procuring the necessary components is transferred elsewhere.
Our industry – like others – has reached a cross-road: division of labour, globalisation, easy communication and logistics accelerated changes. Our industry has become a mature one. Therefore, it is inevitable that technology and know-how is developed in other regions. But we have to be aware that we are losing technology. Already certain technologies like the cell phone business have left Europe; others, like IC-substrates never came to Europe.
Another surprising aspect is that European companies shift their business to Asia while at the same time Asian companies come and invest in Europe in order to be closer to their customers and markets. What we now need is a new concept for the supply chain. Closing ranks, earlier exchange of information, reducing expenses and improving logistics will obtain much better results and create higher value for money than procurement around the globe. The good old rule to have at least two approved suppliers in different locations of the world was dropped and in many cases it backfired already.
The PCB industry is a 'Case Study' for European manufacturing
Many European industries are confronted with the same nature of problems. Therefore, our concern about the PCB industry at the same time may serve as a case study for all other European industries. We have to think about which products could remain in Europe and how to support this action on a European level.
There is no doubt that products with high labour content, high volume, long life cycle and little or no technical changes will always be manufactured at the most competitive and cheapest location available. This place, of course, can change at very short notice and it is clear that it most likely will not be in Europe. On the other hand, however, Europe remains engaged in manufacturing which involves:
• low volumes in a large variety of alternatives
• short-life cycles and fast changes in demand
• short time-to-market
• high transport costs but low labour costs
• frequent technical changes in demanding technology
• innovative products and new product introduction
• product requiring high security for clients like banks and the military
As long as this is the case, manufacturing companies in Europe (mainly SME) are able to accept the challenge – but only if they can meet this challenge in a position of cooperation and strength with their customers. In these cases the challenge is open for Europe to participate in this global contest. Certainly, all this will represent a potential of high value added and at the same time it is an efficient complement for larger companies as it secures necessary supplies. And this trend of down-sourcing from a large to a smaller unit will hardly go to the expense of jobs.
What general changes are necessary for the industry in European?
• Manufacturing in Europe remains the focus of our concern. Innovation in the manufacturing process must be associated with innovation in new products otherwise both parties will lose. Therefore, support for research and development should not be limited to "What to do" but has to be extended to "How to do it".
• To create additional jobs has to have the same positive recognition like the development of a new product.
• If we only sponsor industrial programs with large companies without at the same time promoting manufacturing in Europe, we will create big and beautiful empty shells without securing employment.
• “Fabless” in Europe is equal to “Jobless in Europe”. The social cost of “Fabless” become visible when a plant ceases production and the social cost are burdened to the community. These costs ought to be taken in account when sponsoring any programs.
• We only will be as good as our technical skills. But seeing the closure of factories discourages a lot young people going to technical professions or to study at universities. We aggressively and offensively have to support technology education.
• We will be able to maintain a strong industrial position if we sustain our capacity to create and develop strong supply chains. But it is a well known fact that any chain will only be as strong as its weakest link. Therefore, SMEs are essential and indispensable for the survival of large OEMs.
• We need specialists coming from SMEs to be involved in committees for the electronic and the PCB industry. We need one person in Brussels to represent the supply chain of our industry (from design via the PCB to assembly and their supporting suppliers), their organisations and associations.
• Taxation laws in all member states of the EU should be directed to support and sponsor the industry located in the community. Tax incentives should be granted to business ventures which manufacture new products.
• Likewise easy support and facilitated cooperation between SMEs are further requirements for our industry.
• And, finally, technical cooperation between SMEs, institutes, universities and OEMs on research programs should be facilitated and find better support in reducing the existing red tape.
Our conclusion is that it is high time to adopt a leading European role again. The alternative is that we will see that our PCB industry and many more industries linked to it are disappearing.
We need to create a different industrial Europe, different from what it is today. We have to participate in the challenges and to meet the promising aspects of the years to come.
We are inviting the readers of this article to participate in the discussion and to let us have your suggestions and ideas in order to create in all Europe the base and the spirit for the change needed. We have to start now, otherwise it might be too late. What are your comments and ideas to our question Europe: Ready for Changes?
-----
bdebconsulting@gmail.com / info@data4pcb.com / augustomeozzi@gmail.com


