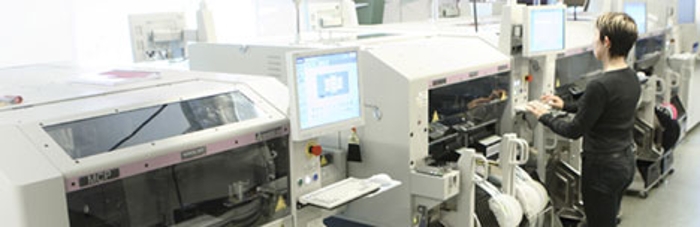
SMT & Inspection |
HPI electronics relies on Assembléon for quality production
Contract manufacturers face new challenges daily, never sure what new components or production volumes their OEM customers will present next. High quality is of course a given – prototypes particularly may come with only one set of components for assembly into a board that must work.
Costs must be kept at rock bottom, too, even when a consumer phone prototype is followed by a full production run of security equipment. Line setup must be fast and easy, and the production line has to work throughout as a single, integrated system.
HPI Electronics, located in Holbaek, Denmark, supplies a complete PCB and equipment design, prototyping and manufacturing service for OEMs. Applications cover consumer to telecoms, industrial, medical, automotive and security equipment. So, the EMS-provider has to deal with the broadest range of circuits – from analog to embedded systems and digital interfaces, power management systems, and wired and wireless communication.
That variety of equipment demands a tremendously wide range of components, from transformers and large connectors right down to micro-miniature 01005 chip components and 0.3 mm pitch CSP devices. The pick & place equipment must handle all these, but so too must the screen printer up front in the production line. Three quarters of manufacturing defects can come from faulty solder deposition. The different sizes of components need very different – and consistent – amounts of solder paste to ensure 100% reliable connections for several thousand joints on a PCB.
These were issues facing HPI when it recently upgraded its production facilities. It was faced with increasingly complex production requirements and ever wider component mixes. To handle the various high-quality requirements, the company decided on Assembléon’s MCP screen printer followed by a high-mix medium-volume pick & place line with an MC-1, MC-8 and MC-12 from Assembléon’s Modular Compact range.
“We already used Assembléon machines, so our staff is familiar with the user interface” said HPI’s CEO, Gert Nielsen. “The equipment is easy to set up and use, and gives us all the capacity we need with very low lifecycle costs. We already have experience of Assembléon’s excellent after-sales service. They have helped us to increase our business share over the last five years, and we felt our purchase will continue to give us a significant competitive advantage over at least the next five years.”
Higher yield and higher quality brings lower costs
The new pick & place machines are HPI’s third generation of Assembléon equipment, replacing the Orion, Emerald, Topaz and Opal – Assembléon’s previous mid-volume generation. HPI is in fact a long term Philips customer – starting off some fifteen years ago with the Philips CSM60.
HPI’s MC-12, MC-1 and MC-8 combine to give fully balanced production with a total of up to 69'000 components per hour (cph). The MC-12 is used for chip shooting, with the MC-1 as an IC shooter. These handle all the common packages including Quad Flat Packs, Ball Grid Arrays and Multi-Chip Modules. Alongside any remaining chips and ICs, the MC-8 places special and odd-form components like press-fit through-hole connectors with variable placement force up to 30N.
“As a contract manufacturer, we of course have many New Product Introductions” remarked Nielsen. “Offline and online software on the machines shortens the time from CAD to production. On–machine or scan teaching of PCBs without CAD data simplifies program generation. We find it easy to teach the system how to handle new components. From around 200 different components on a line, we are expanding that to 340 or more. Fast changeover is very important, particularly with single-batch runs for prototypes. The MC machines integrate with our MES software to improve manufacturing efficiency and perform tracking and tracing.”

