What drives the cost of a circuit board?
The majority of the cost – 80-90%- is built into the product in the early stages of the design phase –before either the PCB supplier or EMS company has sight of the design. We have also found that many of the cost drivers directly impact all aspects in producing and delivering a more sustainable product.
To avoid large cost drivers we have developed a tool that can support you.
Download it for free here.
NCAB has divided the cost drivers into two categories, the ‘hard costs’ and the ‘soft costs.’ The hard cost drivers are covering aspects that relate to the physical printed circuit board itself. Examples being copper weights and build complexity. In these cases the impacts on sustainability are more tangible. The soft cost drivers are those elements that unless considered can lead to delays in engineering, lost time and mis-specified demands that only serve to either drive cost upwards or fail to identify what is needed to achieve the desired quality or long-term reliability – this is not sustainable PCB production in our eyes. Many times these factors are a little less quantifiable, but can certainly have just as much of an impact on cost and sustainability.
Example of a PCB cost driver:
Via treatments
When designs become more complex we often have requirements for via in pad or via treatment to ease assembly, we refer to IPC 4761, to avoid via related problems in the future. With multiple solutions offered by this specification, each has a different cost driver. Knowing what you really need for assembly can ensure the 4 Via treatments most cost-effective solution is utilized.
The figures below are average based upon a cross section of factories. As such these figures shall only be considered as a guide or point of reference.
Soldermask covered (Tented) +0% Soldermask plug +1–5%
Type VI +5–10%
Type VII Nonconductive resin +7–12%
Type VII Conductive resin 20+%, subject to material MOV
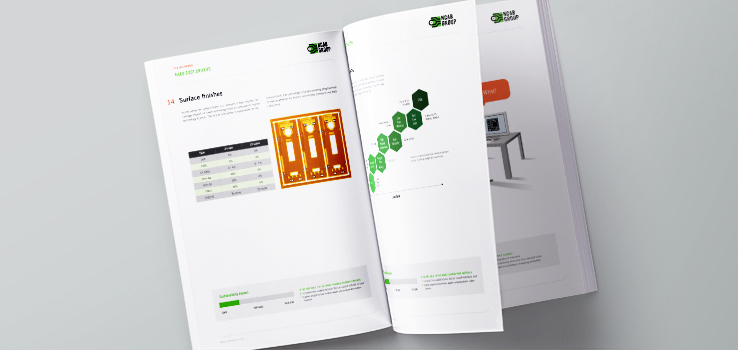