Sponsored content by Mek (Marantz Electronics)
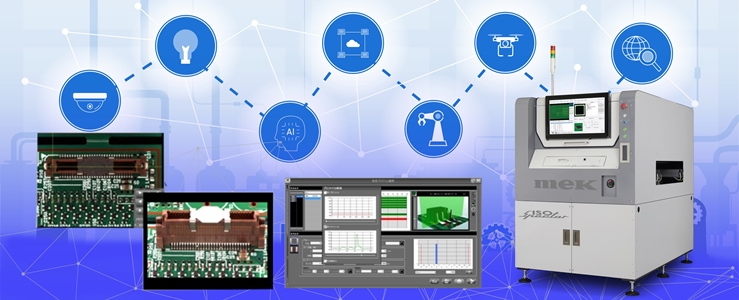
3D AOI connectivity is exceptionally important, but what about inspection quality?
3D automated optical inspection (AOI) systems have become a critical component of production lines in electronics manufacturing Smart Factories as the hubs for quality control, giving valuable feedback to the production machines. But Smart Factories with AOI can only work if the AOI results are reliable…
Read more
Of all the systems in a SMT/THT assembly line, automated optical inspection systems have the most scope for development and improvement as they are the least mature technologically, the most complex, very software oriented and highly dependent on computer processing power.
Since the emergence of Smart Factory 4.0 concepts and the intense focus on connectivity and data exchange, focus on the technical capabilities of connected systems has diminished. However, this connectivity is only useful when the data provided is accurate. AOI systems, and more specifically AOI systems with 3D measurement capability, are a key component in a Smart Factory environment as they are the hubs for quality control, giving valuable feedback to the production machines. Mistakes made by an AOI, like false positives (escapes), are typically not discovered directly, and in the case of false negatives (pseudo defects), connected systems get backlogged with incorrect suggestions. Smart Factories with AOI can only work if the AOI results are reliable.
Being such important hubs, 3D AOI’s need increased focus on their technical capabilities. As the industry agrees that the technical specifications of an AOI system do not explain its capabilities, for prospective buyers it is probably the most difficult equipment to choose. Typically, evaluation engineers need to base their choices on just a few hours of system assessment. Depending on how thorough an evaluation is, most decisions end up being based on emotions and what others are using. This results in new, technologically advanced solutions not getting the attention they deserve.
Established in 1997 and now with over 8,000 worldwide installations, Mek (Marantz Electronics Ltd.), is a well known manufacturer of AOI and SPI systems who continues to invest in innovation, research and development. In the headquarters in Japan, a large engineering team concentrates on developing the connectivity capabilities of the system, but a still larger team is working on improving inspection.
The latest addition to the wide range of products is the Mek ISO-Spector M1 full 3D AOI with Artificial Intelligence. A true, full range, no compromises, fast to program 3D AOI system.
The Mek ISO-Spector M1 took several years to develop and is designed using the very latest that modern technology has to offer in terms of both hardware and software. The result is a self-learning, high specification, high accuracy system that is easy to program with programmer independent inspection results. The fact that it is self-learning with Artificial Intelligence is what makes this unit particularly special.
Camera – FoV
For self-learning AOI to be possible, the initial measurement results need to be accurate and reliable. At the heart of the ISO-Spector M1 is a 25 mega pixel sensor with the industry’s fastest data transmission interface and most accurate data per pixel. The high number of pixels is necessary to create as large a field of view as possible so that larger components, like connectors, can be captured while maintaining resolution for the small solder joints in the same view. Inspection speed is also increased as the camera makes fewer movements. The field of view is a massive 69mm x 69mm which is currently the industry’s largest for a 3D AOI.
Projectors
To make height measurement possible for volumetric calculations of components and solder joints, active projection of light is required. The Mek ISO-Spector M1 features 4x multi frequency Moiré fringe projectors that are the equivalent of 16x projectors. The projection is from an impressive angle of 80 degrees and eliminates almost all shadow effects caused by tall components and other objects. Skipping 3D measurement of certain components is a thing of the past. Multi-frequency projectors mean that different Moiré fringe patterns can be projected to measure a higher range while maintaining the Z (height) step resolution in the critical ranges. The max. measurable height is 25mm. Components with uneven surfaces can still be measured, even when that surface is reflective.
The ability to measure such heights (25mm) is of great importance for reliable solder joints measurement. Obviously, there are no solder joints in that height range, but the body height measurement is always necessary. One of the biggest advantages of 3D measurement is the accurate determination of component body position and rotation. As components can shift and/or rotate during the production process, the positions where solder joints need to be measured shift and/or rotate too. If component surface height measurement is ignored because it is out of range, then the “3D” AOI will need to use 2D image algorithms to detect the position and rotation of the component body. Most 3D AOI systems are limited to only 5mm height measurement while the Mek ISO-Spector M1 measures up to 25 mm by default.
Read more
Why doesn’t every 3D AOI measure up to 25mm?
Not every manufacturer uses multi-frequency projectors and thus increase the measurable height range because of the complexity and the hardware restraints. The projected patterns need to cover the whole area of the field of view from a certain distance and angle. Measurement reliability and accuracy strongly depend on the parallelism of the projected pattern. It is an optical challenge to overcome the parallax effect of the projected pattern due to the projection angle. The ISO-Spector M1 optical unit is engineered with the latest Japanese optical technologies which, even from such a steep angle of 80 degrees, manage to project perfect patterns across the massive 69mm x 69mm field of view. Another challenge is the focal depth of the lens used. Telecentric lenses, which are used in 3D AOI’s, have the issue of a shorter focal depth compared to conventional macro lenses. Projected patterns need to be seen by the capturing sensor with the same sharpness and brilliance level at the PCB surface as at the highest measurable point. Without an extended focal depth, projected patterns become blurry on the higher surfaces compared to the lower surfaces.
2D aspects
Even with a full 3D AOI system, some aspects of inspection still require 2D algorithms. Colors, fiducial marks, some type of polarity marks, text, some foreign materials and some solder bridges are typical examples. Ingenious 2D lighting projections are then as important as the Moiré projectors for a 100% inspection. The ISO-Spector features 2x stage RGB lighting from 2x different heights and angles. With 24 lighting combinations, including additive and subtractive lighting, there is always a combination (or single lighting) that emphasizes the 2D test point for perfect inspection. Text inspection can be a challenging task for an AOI due to varying print quality. For example, lasered text on small diodes or small transistors can be barely visible, even completely invisible, under normal lighting conditions. The Mek ISO-Spector M1 with two stage RGB lighting and numerous combinations overcomes this issue and can make virtually every challenging text type visible. Once the text becomes visible the system can use OCR (Optical Character Recognition) algorithms or OCV (Optical Character Verification) to inspect the components’ type.
Further articles in this series will delve more deeply into Programmability, the wide variety of inspection scenarios that the M1 can accommodate, and vertical and horizontal “connectivity.”
Read more
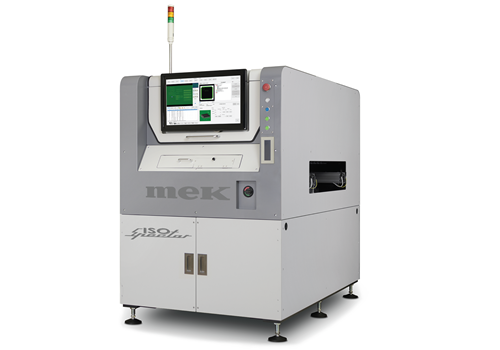