Sponsored content by Electrolube
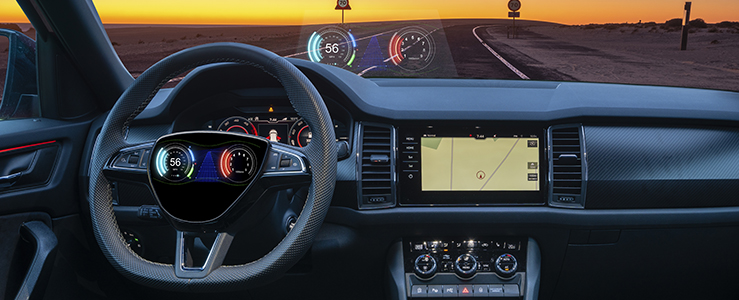
Maximising Performance and Reliability of Automotive Electronics with Conformal Coatings
Phil Kinner, Head of the Conformal Coatings Division at Electrolube, explains how modern, carefully formulated conformal coatings are helping automotive electronics manufacturers to deliver high-reliability, long-life products for a particularly demanding customer base.[b][/b]
While the value of the electronic systems in a modern vehicle typically exceeds 20% of the total vehicle cost, many estimate that this value will exceed 35% within the next 5 year period. With the increased adoption of electronic vehicles and the development of the Internet of Things, which has brought us driverless cars, the future of this industry is starkly different to that of the past.
The proliferation of automotive electronics has been enabled by the development of powerful networked controllers and low-cost sensors, as well as the development of low-cost, high reliability electronic systems that have seen engine management, infotainment, passenger comfort and safety applications becoming standard equipment in most modern automobiles.
It is not uncommon for modern new vehicles to be supplied with 5 and even 7 year warranties and this is challenging component suppliers to develop new designs that deliver long term reliability at an acceptable cost. Automotive electronic systems are subject to temperature extremes, high humidity and condensation, and are increasingly exposed to corrosive gases. And with the growth of electric vehicles, where much higher voltages are the norm, increased dielectric protection is required to enable designs to be sufficiently dense to meet size and weight constraints.
The increased sophistication of these electronic systems often means they are more sensitive to contamination and adverse external environmental conditions. Moreover, as automotive electronic systems rely increasingly on their interconnection, failure in one assembly can compromise the operation of another. Unlike aerospace applications where two or three layers of redundancy may be built into these systems, automotive designs typically must work first time, every time, throughout the life of the product.
Circuit protection using conformal coatings
Conformal coatings are thin, protective polymeric coatings that are often applied to electronic circuit boards or assemblies to provide the required environmental protection without excessive cost or weight penalties. For the automotive industry, conformal coating applications are either ‘in-cabin’ (electronics systems located within the passenger compartment) or ‘under-hood’ (electronics in close proximity to the engine). Such distinct categories make it convenient to discuss the main requirements of each; however, with increased sophistication and the move towards multi-function assemblies, these traditional environments continue to merge, while the drive to higher power electronics in electric cars blurs the lines still further.
Electronic sensors and systems situated in the passenger cabin essentially occupy the same space as the vehicle occupants. In the winter, that can mean extreme cold and the tendency towards a condensing atmosphere, while in the summer, the tendency is towards a warm and humid atmosphere. Both condensation and high humidity challenge the reliability of electronics as they promote corrosion. In addition, electronics may be exposed to atmospheric pollutants such as cleaning solutions, liquid splashes and so on, and any one of these factors may pose a potential reliability risk, especially in association with humidity and condensation.
Corrosion is a complicated electro-chemical process, with a variety of potential mechanisms and causes, and any detailed description is beyond the scope of this article. However, in the vast majority of cases, there are three conditions that must be met in order for corrosion to take place:
Intrinsically electrochemically dissimilar metals (e.g. gold/silver and nickel/tin) are present or an anode and cathode are created by application of applied bias.
The presence of an ionic species (usually salts, halides, hydroxides, etc).
Mono-layers of condensed water are present that dissolve the ionic species, resulting in an electrolyte solution.
In order to prevent the possibility of corrosion, it is necessary to remove one of the pre-requisite conditions.
The choice of metals is limited to those used in the solder and solder finish chemistries, which are dissimilar, and there will always be areas of potential difference due to the nature of an electronic assembly. Cleaning can help remove ionic species, but cannot prevent the re-deposition of ionic species from the operating environment.
Conformal coatings help prevent the formation of electrolytic solutions by acting as moisture barriers. The coating needs to be a good barrier against moisture and must have good adhesion to the substrate to prevent delamination. Once the coating is delaminated, moisture can eventually collect in this ‘pocket’ and form an electrolytic solution with any pre-existing ionic contamination. This is why cleaning prior to conformal coating is recommended to provide a powerful synergistic elimination of two of the three pre-requisite conditions for corrosion.
Given the relatively benign operating environments experienced by 'in cabin' electronics, acrylic conformal coatings have historically dominated this segment, offering good all round properties, especially against high humidity and spills and splashes.
Under-hood electronics, by dint of their location, face greater environmental challenges than ‘in cabin’ electronics. This environment is much less controlled, with higher maximum operating temperatures and far more opportunities for contamination by fuels, oils, cleaning fluids, corrosive gases, metal particulates and salt-water slush spray from treated road surfaces. Clearly, 'under-hood' and other non-cabin electronic assemblies suffer much tougher environmental conditions and thus require the greater levels of protection provided by a new type of conformal coating.
Protective coatings: the next generation
Coatings for electronic assemblies destined for under-hood and other non-cabin applications are required to be extremely resistant to wet conditions, have excellent chemical resistance, be highly flexible to survive thermal excursions and thermal shock, and be able to survive the much higher operating temperatures.
To counter these challenges, Electrolube has developed a new range of highly durable, solvent-free, modified polyurethane conformal coatings.
These coatings have been thoroughly tested for:
Moisture resistance
Thermal shock resistance
Salt-mist resistance
To read more about this testing, please view the full article on the Electrolube website here.
Summary
These materials have demonstrated significant performance improvements on model PCB test assemblies, in terms of resistance to thermal shock, condensing and salt-mist environments, over that of traditional conformal coatings, ultra-thin coatings or even UV curable materials.
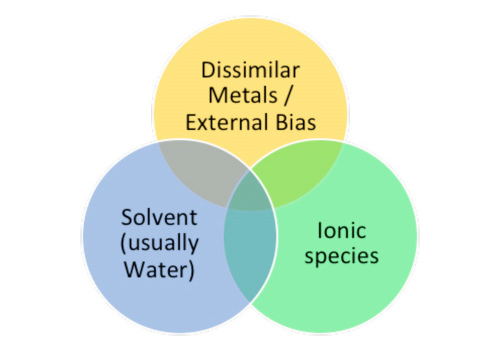