A practical showcase of the machine’s fun. Creating a new product usually takes anything from a couple to over a dozen months. The last stage of designing and batch production relies on tests to confirm the quality and reliability of the electronic components which comprise the device. What are In-Circuit Tests (ICT) and Function Tests (FCT)? How are they carried out and why should they be applied? Find out about the 7 key reasons and see how we run tests in the Comarch IoT Plant!
Here in Comarch IoT Plant – a cutting edge manufacturing laboratory located in Kraków – we offer high quality services in the area of fast prototyping, assembly and post production quality control of electronic devices (EMS). For us, testing is a crucial part of production services. We conduct a wide array of tests daily, including FLYING PROBE, ICSP and FCT, which are some of the most effective methods of checking the quality of electronic components. Why is it so and what exactly should these tests be used for?
Image 1. Production hall Comarch IoT Plant
FLYING PROBE TESTS
Flying Probe (FP) tests are used predominantly during prototyping and small batch production of electronic devices (EMS). The concept of Flying Probe is based on a system of measurement probes moving in 3 axes which enables dynamic and on-going access to the selected test points.
This allows potential assembly defects to be detected (e.g. breaks or short circuits). FP tests make it possible to actually measure the value of the components after SMT or THT assembly, as well as to check the quality of printed circuit boards (PCB).
The basic FP tests include:
- PCB connection tests
- PCB insulation tests
- electrical resistance tests
- electrical capacitance tests
- Zener diode tests
- transistor tests
- electrical reactance tests
- capacitor polarity tests
- connector assembly tests
The Comarch Technologies IoT Plant utilizes a system consisting of 8 heads, each equipped with 8 measurement probes, 2 capacitance probes and 2 feed probes. Notably, access to the printed circuits takes place from both sides of the board simultaneously. The vertical positioning of the input module reduces bending of the board which allows for precise access to most of the test points as well as pads, spacers or other signal terminals on the PCB.
Some of the key advantages of this system are short testing time, flexibility of the system’s software and a resulting decrease in the cost of launching prototype or small batch production runs, which is extremely important from the perspective of the profitability of the project. Building tests based on permanent fixtures is time-consuming and expensive, which makes it altogether impractical for prototype batches.
Image 2. Flying Probe machine in Comarch IoT Plant
THE FUTURE OF TESTING
Progress made in the area of Flying Probe tests shows how much potential there is in a wider application of this solution. The choice of test for prototype or small batch production is made at an early stage of programming the tester. Featured modules enable us to control the duration of testing depending on the production volume. A wide array of optimization options depending on the production requirements allows for a significant reduction in the time necessary for programming and testing.
Using the Flying Probe also allows us to access the connector nodes on the PCB and perform measurements of the particular components separately. This in turn makes it possible to check whether the given node is located in the right place and whether it has the appropriate value and polarity. Elements may also be identified on the PCB by means of parameters such as resistance, capacitance or inductance measured between two points. That is because the tests use a real electric signal. Additionally, the use of advanced algorithms for generating tests automates the programming of the particular stages of the process.
Owing to this, the Flying Probe makes it possible to conduct a truly comprehensive PCB test and confirm that the given circuit was produced properly and in accordance with the relevant specification. Notably, the system is also equipped with an external feeder which enables operation in the small batch production mode.
In conclusion, the use of Flying Probe tests brings the following advantages:
- Reduced time and cost in comparison to permanent test fixtures,
- Less time necessary for developing test programs, easy integration of changes in the project,
- Flexible process and easy introduction of changes,
- Access to the circuits even without dedicated test points – makes it easier to select and design tests and to optimize them at a later stage,
- Controlled pressure of the probes sensor, programmable for any type of PCB board which enables precise adjustment and protection against damage to the circuits,
- Various testing solutions and strategies integrated in one system allowing for shorter testing and programming times – especially with prototype batches,
- An in-built, precise system of positioning and measurement which enables accurate positioning of the probes in real-time – a feature which is unavailable with the use of permanent fixtures (e.g. in the case of changes to the PCB design).
ICSP (In-Circuit Serial Programming) and FCT tests
One of the applications of the FP machine developed in the Comarch IoT Plant is device programming over serial interfaces. At the moment it is possible to program ARM Cortex-M circuits with the use of the SWD interface. Specialized functional tests are currently being developed, including for example measurement of power consumption for devices with low energy requirements or testing the operation of key elements of the circuit. Owing to the possibility of conducting ICT tests and functional tests on one machine, the test results can be compiled in a single report.
ICT and FCT tests are among the most important stages of prototyping electronics in the production cycle. They are an integral part of the cycle as they allow for the verification of design and assembly. They make it possible to detect errors at a very early stage, as well as later on in the production batches. They are an essential tool in the creation of small and reliable devices of the highest quality.
“Here in Comarch IoT Plant production quality is our number one priority. This is why we adopted a holistic approach to testing and examine both the product’s safety, manufacturing quality, functionality as well as performance and effectiveness. We are among the few companies in Poland with a comprehensive strategy of production at every stage – from designing and prototyping to production and final testing,” recounts Mr. Piotr Kołtun, responsible for the Comarch IoT Plant solutions.
Image 3. FP tests at Comarch IoT Plant
Image4. FP tests at Comarch IoT Plant
THE KEY TO EFFECTIVENESS
In electronics contract manufacturing, ICT, Flying Probe or FCT tests determine the quality of products which arises from their proven effectiveness and reliability. They also guarantee proper, fault-free operation, which is why they are the key to an effective manufacturing process.
If you are interested in the process of programming and testing, be sure to watch the video showing production of the specialized NB IoT gateways which we conducted for one of the water supply companies in the United Arab Emirates in February 2019.
Author: Tomasz Jaje
ABOUT COMARCH
Comarch is a leading Central European IT business solutions provider specializing in forging business relationships that maximize customer profitability while optimizing business and operational processes.
Comarch Technologies draws from a wide expertise Comarch has accumulated during 25 years of its business activity in the field of delivering comprehensive IT solutions. Its main concern is to provide the customers with the most reliable and secure solutions that consist of advanced software along with innovative hardware infrastructure supported by professional services.
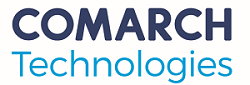
More information:
Piotr Kołtun
Business Development Manager
Phone: +48 12 621 51 92