Sponsored content by CML
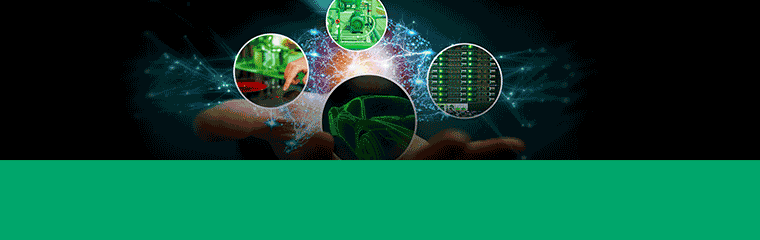
CML putting the drive into e-mobility
As the global demand and trend for e-mobility grows, we understand that customers are looking for products with better performance, stricter tolerance, increased reliability and cost effectiveness. This means your PCB provider must understand the challenge you are facing, be able to support you throughout the whole process – from the first technical questions to the end of life.
CML has been delivering reliable PCBs to some of the biggest global automotive brands since 2001. With our experience and commitment to quality, we generate almost 80% of our revenue in the competitive and highly quality demanding automotive industry. You can rely on our PCB experts, who can provide you with solid technical know-how and advice at every step of the PCB process.
With our well-established manufacturing and sourcing infrastructure, we can provide high quality and flexible solutions for your needs.
CML has completed several e-mobility projects for some of the biggest worldwide automobile manufacturers. For these applications our PCBs are summited to very hard technical and environment challenges. Our global engineering team provided their best knowledge, customized and cost-effective solutions to help our customers overcome the challenges.
Automotive on Board Charger Applications
The main challenge in this application was fitting a huge number of boards and combine classic FR4 boards with insulated metal substrates (IMS) inside of a tight volume. We proposed the following to our customer: a KANBAN delivery flow and some connectors redesign, alternative cost-effective surface finishes and eliminate wave soldering in some of the boards. We also further developed a special IMS material to withstand high voltage requirements with higher thermal conductivity (5kV after PCB processing and 7W.m.k-1). Using IMS boards in the charger allow our customer to eliminate costly ceramic boards, carry more power than standard PCBs and decrease charging time for the e-cars. We also developed a high voltage test methodology to guarantee consistent quality and speed up incoming inspection in customer factories.
Automotive Inverters Application
Inverters are the “brains” of hybrid and electric cars. They contain the drivers and power modules, components responsible for the control of all power going from the batteries to the electrical motors, allowing the driver to start his car and drive! There is a consequent amount of heat and some high voltage constraints to be managed. The original circuits are a mix of some high voltage boards and High-Density Interconnection (HDI) applications to be able to assembly the processors to control the engine. HDI is a consequence of the increasing number of functions and decrease in space.
Together with one of our partners, our engineers developed a FR4 base material capable to compete with best in class Japanese brands and capable to achieve top rated performance (e.g. Insulation resistance, Voltage breakdown and CAF Test). The final material has an important cost advantage and equivalent quality level. Our important efforts helping customers to validate their design through integrated prototyping under mass production conditions, using the exact same set of materials and manufacturing lines resulted in significantly shorter time to market and R&D costs.
Battery Management System (BMS) Application
The BMS is responsible for controlling how the battery pack operates in hybrid/electric vehicle (light cars or buses). This system is also responsible for deciding how the cells in the battery pack should be charged to maximize vehicle driving range and battery life time. Our solution for this application combines different boards to be able to scale up the system in function of vehicle embedded power without the need of high cost circuit redesign. We also integrate cabling through flex PCB to connect the modules aiming for increased reliability and reduced costs. Standard base materials for the PCBs were tested, complete understanding of their capability was achieved and replaced high cost references after some redesign during the R&D phase. These PCBs are also summited to very tight warping tolerance. Another example of good collaboration between our engineers and customers’ team.
To learn more about our e-mobility know-how and services, please feel free to get in touch with us. It will be a pleasure to come and help you to build the future of people mobility!
About CML
CML are the leaders in printed circuit board (PCB) manufacturing and sourcing solutions. CML’s mission “We care about reliable connections,” places paramount importance on the relationship between all stakeholders from customers to suppliers to the CML Team. These reliable connections deliver convenience and reliability, provides a wide product and service portfolio for all markets. CML has a global network, located across 16 international cities and a local presence with a multilingual and culturally diverse team.
For more information please visit our website: LINK
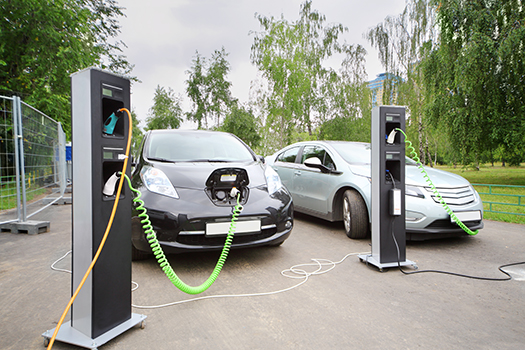
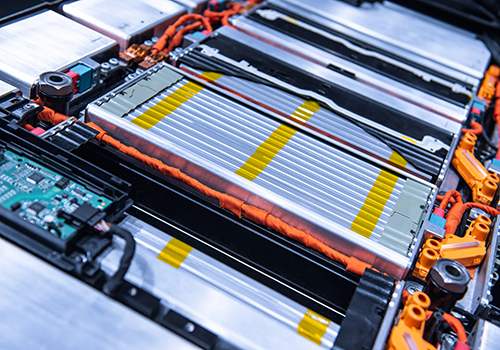