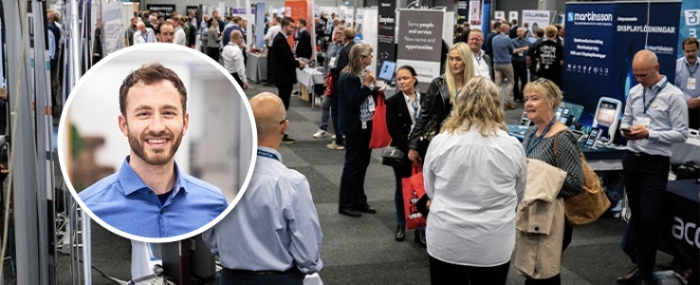
A digital supply chain approach
At the Evertiq Expo in Gothenburg this September, I had the opportunity to sit down with Lukas Zimmermann, Sales Executive at Luminovo, to dive into the evolving landscape of digital supply chains and the role of Luminovo in transforming how electronic designers, manufacturers and suppliers manage their operations.
What is a digital supply chain, and why should we care?
Zimmermann explained, “It’s about putting all the different stakeholders — every participant in the process — at the same table. The aim is to ensure that all the information needed is equally visible, accessible, and understood by everyone.”
The simplicity of this explanation touches on the essence of Luminovo’s solution, where clarity and accessibility across the supply chain drive efficiency and collaboration.
But the question remains — why is there a need for this new approach when the existing systems have served the industry well enough to support its growth thus far: Why go digital?
Zimmermann broke it down into three key reasons:
Speed: Digital systems reduce manual tasks, streamline procurement processes, and accelerate overall operations. “You’re just much faster,” Zimmermann noted, which translates into competitive advantages, particularly in winning new business deals.
Cost and time savings: Replacing manual processes like sorting through Excel files to identify the best deals saves time and reduces errors. By automating these tasks, companies can focus on higher-value activities.
Stronger partnerships: A digital system fosters collaboration, making it easier and quicker for stakeholders to work together, thus strengthening relationships across the supply chain.
Risk mitigation and visibility
When asked about risk mitigation — such as being alerted when a supplier faces disruptions — Zimmermann acknowledged that Luminovo’s platform doesn’t yet cover logistics-related incidents, such as a sudden production halt at a supplier. However, it excels in managing the complexity of sourcing and procurement in the electronics industry. “Luminovo helps reduce the complexity of quoting, sourcing, and monitoring changes in the PCBA,” he said, emphasising its ability to track and warn against availability, compliance, and lifecycle changes.
“We want to offer our customers a comprehensive workflow — one complete solution where they have everything. What we often see is that many rely on Excel and a few other tools, but these tools often don't cover everything and don’t communicate with each other enough. As a result, you are working with multiple tools that are not really well connected.”
Expanding globally while keeping an eye on Europe
Luminovo, which started in Germany, has grown significantly across Europe, and Zimmermann highlighted the company’s presence in other regions like Asia and the U.S. Although these markets are still in their early stages for the company, Zimmermann acknowledged their importance.
“We have customers in Asia and the U.S., but not so many yet. Obviously, we want to increase that presence, especially with big EMS players in Thailand, Malaysia, and the U.S.”
However, expanding beyond Europe brings unique challenges, particularly due to cultural and business differences. Zimmermann pointed out that having people on-site in different regions will be essential as they scale.
Although Luminovo is expanding, Zimmermann revealed that there is still significant growth potential in their home market.
As Luminovo continues to evolve, Zimmermann hinted at upcoming developments: “We’re planning to release a new module in the next one to two months that will help with strategic negotiations, which will be interesting for all OEMs and EMS companies with significant electronics purchasing needs.”
With its focus on providing an integrated, seamless digital workflow, Luminovo is positioning itself as a key player in the digital transformation of the electronics manufacturing industry – setting the stage for a more efficient, collaborative, and resilient supply chain.