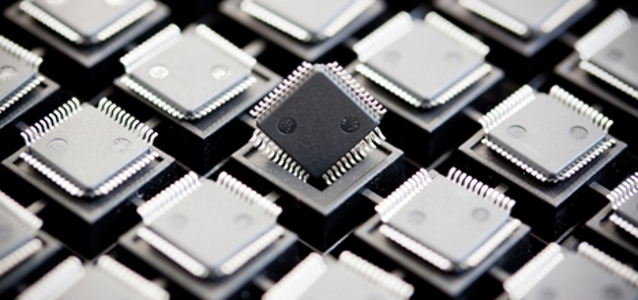
Obsolescence: navigating challenges in an ever-evolving industry
Component obsolescence is a topic that is not talked about frequently enough. It is after all an inevitable aspect of our industry driven by constant innovation – but that doesn't have to mean product obsolescence.
Reacting to obsolescence events can be costly and risky, whereas proactive measures can help detect and mitigate risks, saving both time and resources. These are really the only two choices – plan ahead or react after the fact.
But let's just straighten out a few question marks before we continue. Electronic components become obsolete when they're no longer available from the original manufacturer to the original specification. This often necessitates costly redesigns and new testing (qualification) before being able to put the product out on the market again.
This is not a new problem; it has long existed within our industry. However, electronic component life cycles between launch and obsolescence are shortening. Consumer electronics, a market with increasingly short product life cycles, accounts for a major portion of global electronic component demand. This means that obsolescence is affecting more companies, more regularly than ever before.
Instances like the recent pandemic have highlighted the need for strategies to manage sudden shifts in supply. Rochester Electronics, for instance, provides a bridge to fill gaps left by discontinued components, sometimes supplying for decades after discontinuation. They acquire End-of-Life (EOL) device inventory from Original Component Manufacturers (OCMs), re-manufacturing EOL parts (mostly using original known-good-die) with full authorization.
In industries with longer lifecycles like military, aerospace, and automotive, ensuring a stable supply becomes even more critical. While a proactive approach to obsolescence management is preferred, unforeseen events can disrupt supply chains, underscoring the need for contingency planning – evident by the recent pandemic.
Communication and transparency are vital in minimizing obsolescence risks. Understanding product lifecycles allows for informed decision-making and the development of contingency plans.
During several Evertiq Expos – in Berlin, Germany and Malmö, Sweden – Rochester will share expertise on minimizing the impact of semiconductor shortages and discontinuations.