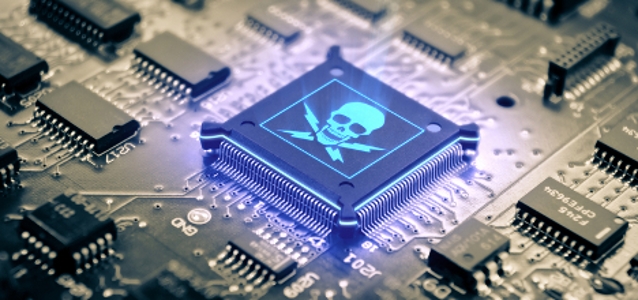
Avoiding the costs of obsolescence, in six steps
Obsolescence is something unavoidable. It’s in the nature of our industry to keep innovating and thus leaving the old behind. But component obsolescence should not mean product obsolescence.
The challenge requires planning and preparation, but facing the issue is for the better. Rochester Electronics, a lifecycle solutions provider, has developed six steps for both planning for and minimising obsolescence costs. During Evertiq Expo in Warsaw later this month, Rochester will share its expertise and best practices on how to minimise the impact of component obsolescence.
Firstly, realise that obsolescence management begins at the design and product definition phases.
In short, component selection during development is a decisive element in possible premature product redesigns and requalification. We have all heard stories of products being launched with obsolete components. This is especially important for companies that have extensive development and qualification cycles. Just as an example, the design and qualification phases for new cars, aeroplanes, or industrial controllers might last up to 5 years. And when adding 5 to 7 years of production and 7 to 10 years of after-sales service, it's not uncommon that one would need up to 20 years of component supply.
Therefore, picking the right component technology and supplier can have a dramatic impact on long-term availability. The general rule for this step is to ask for transparency – ask your supplier what their commitments are to long-term availability.
Secondly, understand the total costs of obsolescence.
One might think that this will be too costly to deal with before it’s even a potential issue. However, it is imperative to fully understand and model both the costs and risks associated with obsolescence. As Rochester points out, component obsolescence is never just a purchasing problem to be addressed as an afterthought.
Thirdly, plan for obsolescence and resource management
Component obsolescence will occur if your equipment has long qualification, production, or in-service lifespan. Manufacturers who are caught off guard by component obsolescence and see it as a minor annoyance to be dealt with will pay the price in interruptions, costs, and risks.
The best practice is therefore to devote skilled employees to obsolescence management. Purchasers, component engineers, designers, and programme managers can cut or eliminate cost and risk via proactive planning. The sudden obsolescence of a 1-cent transistor may potentially stop a programme in its tracks just as easily as the main microcontroller's obsolescence could.
Fourth, identify important Product Discontinuation Notices (PDNs) that may affect your business and monitor them.
Proactive monitoring of component lifecycles is essential for anticipating issues. Commercial tools are available to track lifecycle, lead times, and specification changes, triggering alerts for issued Product Discontinuation Notices (PDNs). Keep in mind that these tools use current market trackers to estimate remaining component life.
Generic management databases allow users to input (BOM) structures, highlighting any PDNs affecting specified products. As each manufacturer has a unique PDN format, manual assessment and logging of affected part numbers can be time-consuming, with some PDNs containing over 500 part numbers.
Fifth, Last Time Buy (LTB) – What to forecast?
Since forecasting is not an exact science, it is unavoidable that some forecasts will be off. It is difficult to foresee product needs years in advance or potential market disruptions.
Accurately estimating after-sales demands might be problematic if production forecasting is production forecasting is difficult, then predicting after-sales needs accurately can be challenging. Underestimating needs runs the danger of ending a product too soon and losing customers. Overestimating needs results in excessive stock holdings and storage expenses.
Additionally, if a redesign in the future is planned to limit the cost of the LTB, then the design, requalification, and opportunity costs of using engineering resources must also be considered.
While there are very few options beyond placing a traditional LTB order, engaging a supplier that has a defined EOL transition path provides the possibility of risk-free continuous authorised stock and production.
Six, purchase from 100% authorised sources
There is a common misconception that once the original manufacturer stops producing a component, unauthorised, or grey market sources are the only option. There are risk-free options; such as an authorised after-market supplier, which should always be the first choice.
The risks of counterfeit and poor-quality components from unauthorized sources represent a significant risk to production yields and Mean Time Between Failure Rates (MTBR) in the field.
Inadequate or substandard testing by unauthorised third parties provides a false veneer of confidence that authenticity can be tested. This testing is a poor partial replica of the original manufacturer's test techniques.
Component EOL/Obsolescence – how to extend product lifecycles?
Electronic component lifecycles between launch and obsolescence are shortening. Improvement in die manufacturing technology and increase in electronic components usage in new technologies and markets causing shortening of life cycles. AI (Artificial Intelligence), consumer electronics, limited fabrication capacity and changes in packages are driving faster change. Obsolescence is therefore affecting more companies, more frequently than ever before. During Evertiq Expo in Warsaw on October 26, 2022, Paul Mason, Global Technology Director at Rochester Electronics, will speak about the impact of obsolescence in Memory devices and how it can be managed.