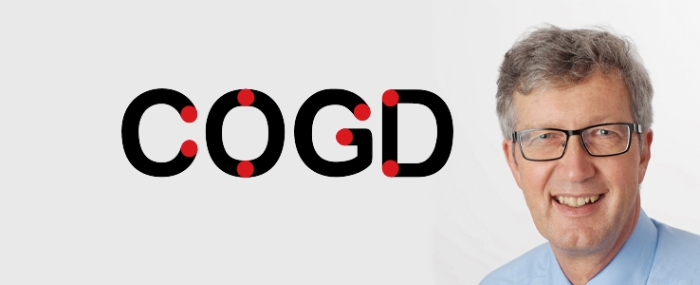
An unavoidable issue getting too little attention
Obsolescence is unavoidable, it can happen at any stage of the supply chain, and if there are no tools or strategies to handle it in place – it can be very costly.
During Evertiq Expo Berlin, one of the driving spirits in shining light on the topic of obsolescence management, Dr. Ing. Wolfgang Heinbach, chairman of the COGD and former president of the IIOM, hosted a session on supply chain resilience via strategic and proactive obsolescence management.
Some key takeaways from the session are that the issue of obsolescence is in fact unavoidable and that it simply isn’t restricted to components; materials, software, data, and human knowhow is also affected.
According to Dr. Heinbach there are only two ways to approach the issue, reactively or proactively. Either you act in the case of an event, which can be costly and risky; or you set up a series of preventive actions which assists you in detecting and avoiding risk factors and also saves you the human resources that otherwise would need to be spent on solving the issue. And that is according to Dr. Heinbach one of the biggest problems – wasting human brain power on dull manual tasks that can be digitised.
Plan for obsolescence and design to minimise obsolescence
Dr. Heinbach provided an illustrative example of how a reactive and proactive approach might differ. With the major difference actually being awareness and planning.
Reactive | Strategic and Proactive |
Sit and wait | Digitised life cycle management and PCN/PDN management |
Read PCN/PDN* | Obsolescence management policy, plan and organisation in place |
Manual processing of PCN/PDN | Obsolescence management is fully integrated into company’s business processes and organisation |
*PCN/PDN is product change- and product discontinuance notices.
The elements of proactive obsolescence management always contain efforts on PCN/PDN management as well as the life cycle management of components and products. But besides that, a continuous evaluation of the business’ supply chain risks should be in place. In thought, it is actually quite simple, but the reality does require some time spent on setting up a process supported by IT systems – but better in the early stages than later, when fixing the issue becomes both problematic and risky. Plan ahead and consider the expected life cycle of components; establish multiple sources; also, whenever possible have multiple designs qualified.
With obsolescence actually being unavoidable, why do you think that obsolescence management still is relatively unknown as a concept?
“Because many people think it’s just bad luck. That obsolescence is something that’s made up by the market,” Dr. Heinbach tells Evertiq in an interview following his presentation. “Many don’t know where to start when setting up a strategy but there is a willingness to set up a process in many cases. Please keep in mind, that in general also the manufacturers are heavily hit by obsolescence on their materials and production machines – it is everywhere in the supply chain”
How would you suggest that companies approach obsolescence management – with respect to available resources?
“It’s three parts. Develop a strategy for how to actually deal with it in your business. Implement both life cycle management and PCN/PDN management. And most importantly, have a plan on how to do it – and don’t approach it with day by day decision making under stress and time pressure. Use the tools that are available and don’t waste resources doing stupid work.”
In a nutshell, a proper PCN/PDN management strategy could help mitigate product design, production and maintenance risks early; assist in avoiding manufacturing shutdowns, product redesigns and surplus inventory.
This is part of the mission of the COGD, to demonstrate the benefits of proactive obsolescence management and to develop strategies, methods and procedures for pro-active obsolescence management.