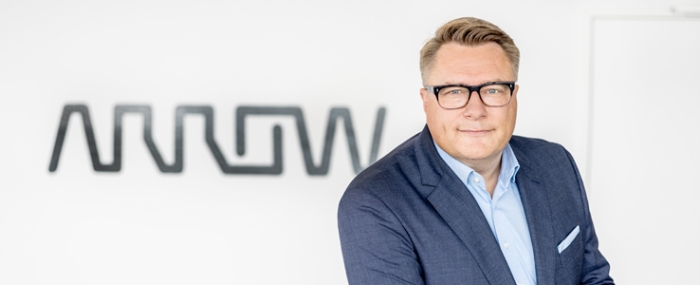
From a distributors point of view – Arrow Electronics
The current ongoing shortage of semiconductors has led to operations becoming more and more complex – and these supply issues are expected to continue through 2022. This have of course meant more business for suppliers and distributors – but a continued shortage on the customer side are two sides of the same coin.
In this article series, Evertiq has reached out to distributors and sourcing specialists of electronic components to see just how the experts are dealing with the current semiconductor shortage and what tools they have in place to cater to the needs of their clients. This time we contacted Jörg Strughold, vice president of sales for Arrow’s EMEA components business
Since the start of the pandemic the situation surrounding the supply of components have only gotten worse, how would you describe the past year in terms of operations?
”All market players in the industry, suppliers, distributors and customers alike dealt with the ongoing worldwide semiconductor and components supply shortage in 2021 as semiconductor production remains a complex process. The distribution industry dealt with an increased semiconductor demand during the pandemic, which created a huge backlog of orders. All this came along with price increases, also for raw and scarce materials. Another aspect is that companies have been and continue to be struggling with rising labor costs as a talent shortage continues. 2021 has been a good year for distributors but higher sales for suppliers and distributors and continued shortage on the customer side are two sides of the same medal,” Jörg Strughold explains to Evertiq.
In the past, during periods of component shortages, we’ve seen an increase of counterfeit components hitting the market – what kind of measures does Arrow have in place to catch these?
”Arrow has supply assurance programs in place to address this problem. These programs protect our customers from counterfeit products and materials by working directly with the original manufacturer to guarantee legitimacy. Counterfeit products often surface when a product reaches its end of life and as the need for the product continues trustful relationships are important. Arrow is among the biggest distributors worldwide and has an unparalleled lineup with franchised suppliers, including almost all well-known and renowned players. Arrow only sources products from its franchised suppliers.”
”Arrow also provides a certificate of compliance to protect customer end products from counterfeit products. As operations have been getting more complex and confusing during the pandemic and constrained supply chains, customers benefit from working with a distributor who is able to manage these challenges,” Mr. Strughold continues.
Which specific product group that has been the most affected by the shortage?
”Almost all product groups have been affected by the shortage. Even when certain products are more readily available, long lead times for high-end products like MCU’s, MPU’s, FPGA’s, high end analog products and power discrete /modules can create bottlenecks and manufacturing challenges.”
What are your feelings about the current market situation as we enter 2022?
”We are still being constrained by supply, and expect this to continue through 2022. Product is moving around based on demand, based on where the suppliers have constraints and attempt to keep everybody moving as far as their production goes. So there is a lot of “hand to mouth”. A lot of work is being done on behalf of our customers to make sure that they can continue to produce their products. Our first quarter forecast is still a supply forecast compared to a demand forecast.”
For 2022, what plans does Arrow have in store to further deal with the problem at hand?
”We work tirelessly to overcome the many challenges caused by the lack of supply in the face of an acute need for components, and we will continue to do so. We will do exactly the same as in the past two years, by working closely with our customers to plan their needs in the long term and ask them to report short-term needs as soon as possible,” Mr. Strughold says and continues.
”On top of this, Arrow is helping its customers to find alternative products, with re-design activities, or we help with design on behalf of the customers. Our redesign services combine Arrow’s market knowledge with our engineering expertise to offer companies alternative paths that could enable them to circumvent the most restrictive allocation issues and achieve more consistent and predictable manufacturing volumes. Overall, improving supply chain management and transparency will help companies to be more resilient and reduce impact from disruptions.”