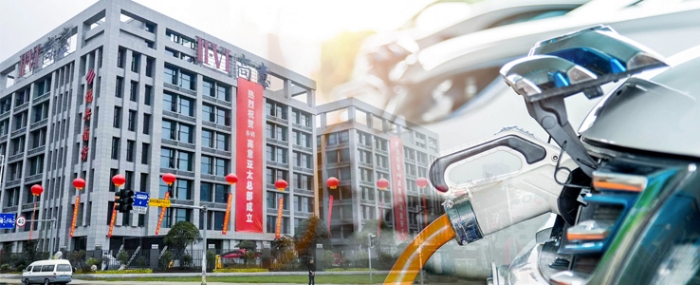
© II-VI
Business |
II-VI expands its silicon carbide manufacturing footprint
II-VI Incorporated says it has expanded its silicon carbide (SiC) wafer finishing manufacturing footprint in China to serve the largest worldwide market for electric vehicles (EVs) and for clean energy applications.
Spurred by increasing regulatory requirements for lower emissions of greenhouse gases and the decreasing cost of lithium-ion batteries, the market for EVs is growing rapidly and driving the demand for power electronics that are based on silicon carbide. To meet the market demand in Asia, II-VI has established a backend processing line for conductive SiC substrates, in over 50'000 square feet of new cleanroom space, at the company's Asia regional headquarters in Fuzhou, China.
“According to recent industry reports, China is expected to continue to be the world’s largest electric car market at over 40% of global sales,” says Sohail Khan, Executive Vice President, New Ventures & Wide-Bandgap Electronics Technologies Business Unit, in a press release.
“We are planning to substantially increase our global production capacity for SiC boules and substrates in the U.S. over the next 5 to 10 years to address the accelerating power electronics market, including for electric vehicles and clean energy applications. These investments will be supported by our global sales force and a SiC platform built by our innovations of the last 20 years, including the world’s first 200 mm conductive substrates in 2015. We are excited about our prospects to lead in one of the most promising markets of our generation,” Sohail Khan continues.
In addition to EVs, power electronics based on SiC enable high efficiency in inverters for solar and wind energy generation, as well as in smart-grid power switching, due to reduced switching losses, high power density, better heat dissipation, and increased bandwidth capability, compared with existing devices based on silicon.
The backend SiC wafer processing performed at II-VI’s new SiC facility in Fuzhou includes edge grinding, chemical-mechanical polishing, cleaning, and inspection, all performed in Class 100 and 1000 cleanrooms. The facility is part of the company's already announced plan to ramp its SiC substrate manufacturing capacity by five to ten times over five years, including with 200 mm diameter substrates.