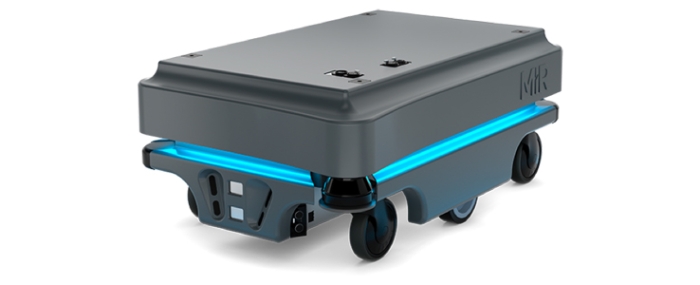
© Mobile Industrial Robots
Business |
Panasonic eyes multi-use potential for PanaCIM
Panasonic, in their push more deeply into smart manufacturing solutions, has partnered with MiR and Inovaxe to develop a handy helper: the PanaCIM Solutions Ecosystem.
The proof-of-concept for the autonomous delivery system, unveiled at IPC APEX EXPO 2020 in early February, aims to decrease labor and material inventory costs while reducing errors by automating the material delivery process. Moreover, the system will deliver materials only as needed, to multiple stops along a programmed route before returning to its base for more.
“Today, electronic manufacturers are striving for ‘Factory of the Future’ capability. Adding autonomous robotics into our ecosystem of total solutions offerings is another example of how integrating third party hardware with PanaCIM is a seamless and easy process,” said Faisal Pandit, president of Panasonic System Solutions Company of North America, in a press release immediately following APEX. “The evolution of our software to include an autonomous component delivers this capability. With a wide and expanding range of partner solutions, we will continue to evolve our offerings of Smart Factory Solutions into the market regardless of their mix or volume.”
After a demo on the show floor at APEX and subsequent correspondence with Evertiq, Panasonic Senior Business Development Manager Shawn Robinson agreed to provide a better understanding of how the system was developed and where it’s headed.
What was the overall scope of R&D time, from early stages to launching of the PanaCIM system?
“This initiative was defined as one of our department’s – and the PanaCIM team’s – main objectives for 2019’s roadmap. We started dialogue with our 3P partners (MiR and Inovaxe) in the summer of 2019. It took less than nine months to go from internal concept to delivering a functional solution at APEX.
“The company specifies that key contributors to hitting this timeline included the commitment and collaboration between MiR, Inovaxe and Panasonic, but also the fact that the PanaCIM software had already laid most of the groundwork with its material control capabilities and standardized interfaces to material management systems.
What was the R&D investment in terms of engineering manpower?
“For the Proof of Concept development, it took about two months of combined man hours of BDM (business development manager) team resources.”
What has the feedback from potential customers been like? Any commitments?
“As this concept of tying Smart Material Management and autonomous material delivery was new to the market, we wanted to gauge feedback at APEX before committing to customers. The solution was well received, and we are now vetting beta customers and productizing ADS to launch to the market in the summer of 2020. Our intention is to sell this solution globally as a part of our solutions business.”
Do you see a use for PanaCIM outside of the electronics manufacturing industry?
“Yes, this solution could be used for other deliveries outside of the electronics market space. The key to that is that MiR is a global supplier/partner, Inovaxe is an innovative and nimble partner, and PanaCIM is agile and can adapt to any environment. I expect the opportunities to be boundless.”
Robinson continued to explain that the company has customers that have already deployed MiR and other autonomous mobile robots (AMR) solutions in their environment through their own “homegrown” efforts, but some significant differences exist between those efforts and the PanaCIM.
“What distinguishes our solution to these homegrown systems is the fact that we have visibility to the actual location and consumption status of their production lines. For instance, homegrown systems also deliver a stack of material which relies on the user at the particular location to hunt and peck to find out what material is relative to them as the AMR systems delivers it throughout their operation. In our case, the Inovaxe system provides improved efficiency by immediately identifying that the delivery is ready for pick up (audible alarm), which side of the cart the material relevant to them is located (through a visual indicator), and through light per inventory location on the cart which material is to be picked. Through this process, we greatly improve operational efficiency.”
What would be some of the most likely scenarios/industries that might benefit from the overall solution?
“Within our market space, the use-case we highlighted at APEX was material delivery from the warehouse to the production floor, but there are several other use-cases for delivery – from receiving to warehouse, delivery from warehouse to kitting areas, magazines of product from area to area – to just name a few.”