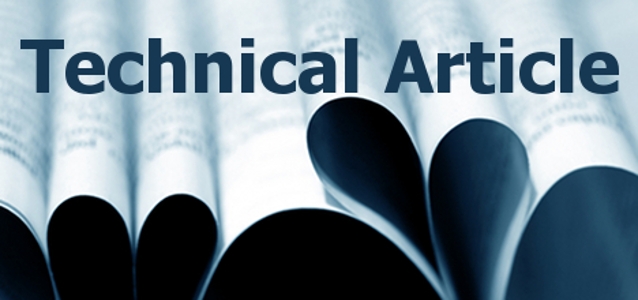
© janaka dharmasena dreamstime.com
Application Notes |
Part 3: Modbus TCP and PROFINET
Ethernet in the Automation Industry Part 3: Modbus TCP and PROFINET - In the first part of this series, we examined Ethernet’s numerous advantages over fieldbuses within industrial automation and control.
Ethernet solutions offer superior bandwidth and lower equipment costs, as well as the ability to be extended across the entire plant as single networks linking the factory floor with enterprise IT. With that third characteristic in mind, we also began, in the second part, to delve into converged plant-wide Ethernet (CPwE), the reference architecture jointly developed by Rockwell Automation and Cisco to encourage the modernization of IAC systems through the use of standard Ethernet in tandem with the IP suite.1
CPwE Overview and Wrap-Up
CPwE is, at its heart, an attempt to help manufacturers move past the complexity of disparate legacy serial networks and achieve the service integration, straightforward maintenance, and high availability that they need to prime their plants for use cases, such as the Industrial Internet of Things. By bringing IT and control engineers—and the respective systems they oversee—under the same tent, CPwE ideally optimizes industrial operations to make the most of raw materials and ensure on-time product and service delivery.
EtherNet/IP® has been the primary vehicle for CPwE, since it serves as a link between Cisco’s Ethernet-to-the-factory framework (which includes security and network architectures) and Rockwell Automation’s integrated architecture with its Logix Control and FactoryTalk platforms. Industrial Ethernet switches within CPwE implementations have common industrial protocol integration via their native EtherNet/IP support.
EtherNet/IP uses standard, unmodified Ethernet technologies to enable this comprehensive end-to-end network integration that is unachievable through purpose-built fieldbuses. The Cisco-Rockwell partnership has also streamlined overall CPwE implementation through support for WLANs predicated on IEEE 802.11 Wi-Fi. These WLANs have granular quality of service and traffic prioritization features to help overcome the interference and coverage impairments that often beset industrial wireless networks.2
The standards-based designs of EtherNet/IP, Modbus® TCP, and some forms of PROFINET® allow for interaction through CPwE.
This time around we will look beyond EtherNet/IP at other industrial Ethernet protocols that support standard networking to one degree or another. After all, part of CPwE’s value proposition is the ability to facilitate interconnectivity and interoperability between IAC networks that communicate mostly within a layer 2 LAN model. The standards-based designs of EtherNet/IP, Modbus TCP, and some forms of PROFINET all allow for this level of interaction through CPwE. Ethernet, IP, and TCP/UDP can be used at layers 2, 3, and 4, respectively, for communications between network devices running standard protocols.
Modbus TCP and PROFINET for Interoperable and Interconnected Networks
Let’s look at the two Ethernet-based solutions—Modbus TCP and a few versions of PROFINET—that can interact with EtherNet/IP and other protocols (for example, HTTP, FTP, Telnet, etc.) without requiring the implementation of nonstandard network interface cards and/or switching infrastructure. Both of these standards are popular, with PROFINET accounting for 8% of all industrial networks as of January 2015, and Modbus TCP holds 3% of the same market.
Modbus TCP
Modbus TCP is a variant of the widely used, vendor-neutral Modbus protocol that was originally introduced by Schneider Electric in 1979. Where Modbus utilizes serial connections, Modbus TCP uses Ethernet as its physical network, with support for the TCP/IP stack for data exchange over IP networks. Modbus TCP was standardized in 1999 and can now be implemented on any device with TCP/IP sockets.3
The open, standardized design of Modbus TCP makes it an excellent choice for interoperable environments. It can be run using regular PC Ethernet cards, plus it is future-proof as a result of having Ethernet port 502 specifically assigned to it. Now managed by the Modbus Organization (since 2004), following its initial development by Schneider, Modbus is an open project with a broad vendor community working on increasingly cost-effective solutions.
The use of TCP/IP, rather than UDP, enables a large number of concurrent connections in Modbus TCP, along with low maintenance control of data transactions. In this way, Modbus TCP diverges from the stateless transactions of its Modbus family predecessors and emulates the minimalism of the World Wide Web.
“The main reason [for using TCP/IP in Modbus TCP] is to keep control of an individual ‘transaction’ by enclosing it in a connection which can be identified, supervised, and canceled without requiring specific action on the part of the client and server applications,” explained a real-time automation guide to Modbus TCP.4 “This gives the mechanism a wide tolerance to network performance changes, and allows security features such as firewalls and proxies to be easily added.”
PROFINET
Having covered PROFINET in several other entries here,5 we won’t do a deep dive into all of the protocol’s features. However, it is worth noting that its design—with support for standard TCP/IP, as well as a special stack that bypasses TCP/IP for transmission of real-time data in PROFINET I/O and IRT—is particularly amenable to balancing the convenience of office Ethernet with the demands of industrial networking.
Like Modbus TCP, PROFINET is mainly used for industrial automation process control. Its support for streamlined cabling (for example, through Siemens’ FastConnect system), deterministic performance over WLAN, and compatibility with star, tree, and ring topologies (in addition to the linear layouts of fieldbuses) have made it a popular choice for simplifying the layout and boosting the performance of modern IAC systems.6 Moreover, the ability to easily transition from PROFIBUS—the most popular fieldbus and industrial network in current use—makes PROFINET integration an easy decision for many manufacturers.
PROFINET, Modbus TCP, and EtherNet/IP are all good examples of how ubiquitous technologies such as Ethernet can be used as the basis for exacting, scalable, and industrial automation. The benefits of Ethernet in factories have always been its familiarity and flexibility—it can unify the industrial and offices networks while going beyond fieldbuses in key areas such as bandwidth and straightforward support for TCP/IP. Architectures like CPwE and the ongoing development of projects such as time sensitive networking (TSN) will only extend Ethernet’s reach in the automation industry in the years ahead and contribute to more efficient plants both now and in the future.
References 1 “Converged Plantwide Ethernet (CPwE) Design and Implementation Guide.” Cisco Inc. 2 “Deploying 802.11 Wireless LAN Technology within a Converged Plantwide Ethernet Architecture.” Cisco, Inc., November, 2014. 3 Modbus FAQ: About the Modbus Organization 4 Modbus TCP/IP Unplugged—An introduction to Modbus TCP/IP Addressing, Function Codes and Modbus TCP/IP Networking. RTA Automation. 5 “From PROFIBUS to PROFINET, Part 2.” Analog Devices, Inc., March, 2015. 6 Advantage with PROFINET. Siemens.
References 1 “Converged Plantwide Ethernet (CPwE) Design and Implementation Guide.” Cisco Inc. 2 “Deploying 802.11 Wireless LAN Technology within a Converged Plantwide Ethernet Architecture.” Cisco, Inc., November, 2014. 3 Modbus FAQ: About the Modbus Organization 4 Modbus TCP/IP Unplugged—An introduction to Modbus TCP/IP Addressing, Function Codes and Modbus TCP/IP Networking. RTA Automation. 5 “From PROFIBUS to PROFINET, Part 2.” Analog Devices, Inc., March, 2015. 6 Advantage with PROFINET. Siemens.