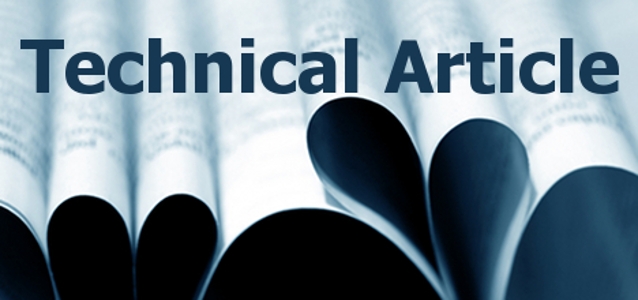
© janaka dharmasena dreamstime.com
Application Notes |
Part 2: EtherNet/IP in Plantwide Automation
Ethernet in the Automation Industry Part 2: EtherNet/IP in Plantwide Automation - We delved into Ethernet’s prominence in the automation industry in the first part of this series,1 covering many of its advantages over legacy fieldbuses.
For starters, Ethernet solutions offer superior bandwidth, energy efficiency, and options for devices, all stemming from the underlying technology’s flexibility, decades of development, and mature vendor community.
In this entry, we’ll look at EtherNet/IP® and examine how it might be implemented in plantwide automation and control systems. The standard is Ethernet-based and largely compatible with existing infrastructure, which makes it a prime candidate for enhancing plant performance while streamlining cost controls.
“A single system architecture, using open, industry-standard networking technologies, such as Ethernet, is paramount for achieving the flexibility, visibility, and efficiency required in a competitive manufacturing environment,” explained a 2011 joint publication from Cisco and Rockwell Automation.2
EtherNet/IP as the Basis for Automation: An Application-Layer Protocol for Both the Factory Floor and the Enterprise Network
A Control Engineering survey of 200 respondents, as part of its Mobility, Ethernet, and Wireless Study for November 2013, found that EtherNet/IP was the most widely used industrial protocol in this group, coming out comfortably ahead of the rest of the field.3 More than 70% of subjects reported using EtherNet/IP in their facilities.
The popularity of EtherNet/IP cuts across industries as diverse as mining and automobile manufacturing. In plantwide automation in particular, EtherNet/IP can support the convergence of numerous applications while ensuring real-time performance. Using Ethernet throughout the factory, EtherNet/IP connects industrial as well as office communications.
EtherNet/IP can be implemented in accordance with Cisco and Rockwell Automation’s Converged Plantwide Ethernet (CPwE), a reference architecture for industrial network design.4 Its aim is the integration of industrial automation and control system applications with the wider enterprise network, via standard network services running toward devices. EtherNet/IP enables this arrangement.
When implementing EtherNet/IP plantwide, the network will need to be structured, with the layer 2 and layer 3 multiswitch hierarchy, as well as zone segmentation based on the functionality of each device and what performance and availability requirements it may have. At the lowest level, one would have actuators, robots, and the like, with applications such as drive and batch control on the next level up and the enterprise network at the very top.
Digging into more granular features of this EtherNet/IP setup, VLANs can be used to segment industrial and nonindustrial traffic and, similarly, firewalls will be necessary for cordoning off the manufacturing and enterprise zones. Moreover, managed industrial Ethernet switches provide the essential resiliency, loop prevention, multicast management, diagnostics, and other services to the network. Gigabit fiber uplinks and redundant paths, alongside a logical topology modeled on the plant’s physical layout, support a resilient network.
What Converged Plantwide Ethernet via EtherNet/IP Achieves
Experienced plant operators have plenty of resources for setting up EtherNet/IP. Plus, the process is eased by EtherNet/IP’s utilization of standard, unmodified Ethernet technologies. But what does an EtherNet/IP implementation guide by CPwE produce for enterprises?
The fundamental benefits of utilizing an Ethernet-based protocol like EtherNet/IP come from the cost-effectiveness, flexibility, and evolution of Ethernet and IP technologies. Similar advantages also exist with modular standards that use existing technologies in enabling distributed automation. These benefits help solve problems such as:
References 1 “Ethernet in the Automation Industry Part 1: The Why and How of Industrial Ethernet Sensors.” Analog Devices, Inc., December, 2014. 2 “Top 10 Recommendations for Plantwide EtherNet/IP Deployments.” Cisco Systems, Inc. and Rockwell Automation, Inc., October, 2011. 3 “Most Used Ethernet Protocols.” Control Engineering, July, 2014. 4 Converged Plantwide Ethernet. Cisco.
- System maintenance: Ethernet is a good alternative to legacy-based automation and control systems, since it is easier to integrate with the enterprise and less costly to maintain. In addition, personnel and expertise on Ethernet and IP are more readily available.
- Data management: Using Ethernet-based protocols allows for better availability, as well as performance with real-time characteristics. Using a single network simplifies the management of data across many applications and systems.
- Integration with business processes: The link between the factory floor and enterprise systems facilitates more rapid decision making. Plant-specific design and extensive validation ensure reliability and sustainability.
References 1 “Ethernet in the Automation Industry Part 1: The Why and How of Industrial Ethernet Sensors.” Analog Devices, Inc., December, 2014. 2 “Top 10 Recommendations for Plantwide EtherNet/IP Deployments.” Cisco Systems, Inc. and Rockwell Automation, Inc., October, 2011. 3 “Most Used Ethernet Protocols.” Control Engineering, July, 2014. 4 Converged Plantwide Ethernet. Cisco.