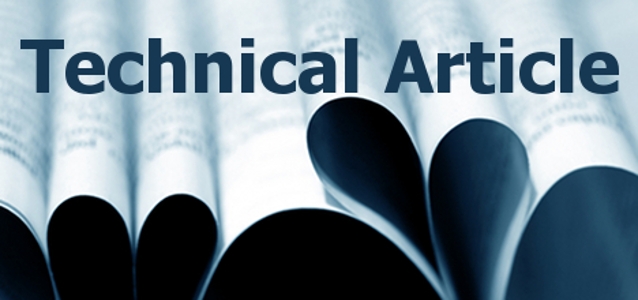
© janaka dharmasena dreamstime.com
Application Notes |
Part1: The Why and How of Industrial Ethernet Solutions
Ethernet in the Automation Industry, Part 1: The Why and How of Industrial Ethernet Solutions - Manufacturing plants around the world now depend on Ethernet solutions for the real-time performance and ruggedness required by industrial applications.
Compared to legacy fieldbuses, Ethernet offers faster speeds, better handling of large data volumes, and, ultimately, more savings via superior energy efficiency and more efficient equipment. It can also serve as the single networking technology connecting automation on the factory floor to the enterprise IT that controls the factory floor—simplifying overall network design while boosting performance.
Why and how does Ethernet work so well in manufacturing? There are many reasons behind its rise, but a few to note include:
References 1 “How to Avoid Collision in Ethernet Port.” Cisco Support Community, July, 2008. 2 Industrial Networking ICs. Innovasic. 3 Chantal Polsonetti. “Ethernet and Wireless Enable Manufacturing Internet of Things.” Automation World, July, 2013.
- Most industrial Ethernet now operates in full duplex to avoid collisions. While collisions are possible in half duplex, they may not be a problem until the ratio of collisions to frames passes a certain threshold. Still, full duplex provides complete collision avoidance.1
- Factories, like other popular settings for industrial Ethernet (such as wind farms and oil and natural gas refineries), are often subject to harsh environmental and operating conditions. Operators have to account for vibrations, particulate matter, and extreme temperatures, and they can do so by using industrial Ethernet cables and connectors in their automation and control systems.
- Industrial Ethernet offers a variety of options for topologies and protocols. Plants can move outside the star topologies that dominate commercial Ethernet and, for example, use ring topologies for redundancy and rapid recovery. Moreover, protocols such as EtherNet/IP® and EtherCAT® cover a wide range of use cases and system designs.
- This series on industrial Ethernet’s benefits for manufacturing will start off with a look at why Ethernet has become a viable option for in-plant automation. From there, we’ll consider how, going forward, both Ethernet and Wi-Fi can help factories move toward the Internet of Things and later discuss how a network built around something like EtherNet/IP could be implemented across the plant.
References 1 “How to Avoid Collision in Ethernet Port.” Cisco Support Community, July, 2008. 2 Industrial Networking ICs. Innovasic. 3 Chantal Polsonetti. “Ethernet and Wireless Enable Manufacturing Internet of Things.” Automation World, July, 2013.