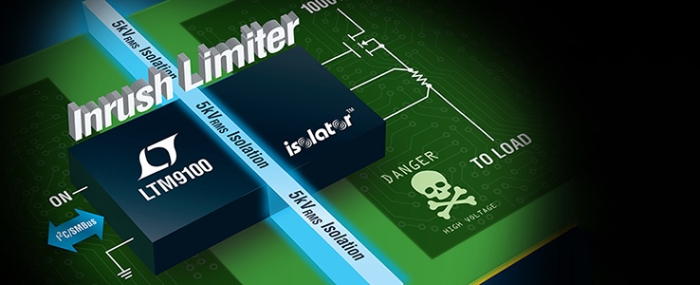
© Linear Technology
Application Notes |
Switching & Monitoring High Voltage DC Power Supplies up to 1000V
DC power supplies in the hundreds of volts are not as uncommon as one might think. An application that may first come to mind is electric vehicles where Li-Ion battery stack voltages range up to 400V.
This is a product release announcement by Linear Technology (now part of Analog Devices). The issuer is solely responsible for its content.
But some lesser known high voltage applications are in modern fighter aircraft, such as the F-22 Raptor and the F-35 Lightning II, which are primarily powered from 270V DC for faster and precise performance. Large solar arrays can output 600V or higher, while rectifying AC voltages in industrial motor drives yield DC voltages ranging from 170V to 680V. And for many years, there has been research and development to move power distribution within a data center from AC to high voltage DC (380V or ±190V), lowering power conversion steps, facility footprint and operational costs while easing integration with renewable energy such as solar.
Distributing power at higher voltages lowers current levels, reducing resistive losses (I2•R), which can be used to reduce cabling weight. All of these high voltage supplies need to be switched on or off and soft-started into loads. For energy monitoring and optimization, it is essential to digitally monitor the voltage and current flowing on these high voltage buses. Any circuit controlling these supplies needs to be galvanically isolated for operator safety and to protect the low voltage electronics from the dangerously high voltage.
Figure 1. Inrush Control Limiters. (a) Negative Temperature Coefficient (NTC) Thermistor (b) Step Start Relay
Methods to Control Inrush Current & Monitor Power
When designing high voltage supplies, an important goal is to safely control the startup inrush current into the capacitive load, e.g., the DC bus capacitors following a typical bridge rectifier. A simple method to lower inrush current is by using negative temperature coefficient (NTC) thermistors, also known as inrush current limiters (ICL, Figure 1a). These thermistors start with a high resistance (e.g., few ohms) at room temperature before the supply or load is turned on; the high resistance limits the inrush current at turn-on. As current flows, the thermistor heats up and its resistance drops by one to two orders of magnitude (by 10x–100x to below an ohm).
These thermistors cost anywhere from $0.13 to $7 each, depending on current and resistance ratings. While simple to use, one problem is that a quick power cycling (on-off-on) may not limit inrush on the second power-up if the thermistor didn’t have sufficient time to cool down to the high resistance state. NTC thermistors suffer from wide tolerances (±25%), and since the inrush current is tied to the steady state current through the resistance drop ratio, the inrush cannot be flexibly adjusted to arbitrarily low levels. ICLs find applications in vacuum cleaners, fluorescent lamps, and switched-mode power supplies, reducing inrush to the bridge rectifier’s DC bus capacitors.
To overcome the NTC thermistor downside of no inrush limiting on a quick restart, a shorting relay is used in parallel with the resistor. This is known as a step start relay (Figure 1b). At turn-on, the parallel relay is open and inrush is limited by the resistor. A timer is also started; when it expires, the relay is shorted across the resistor. Load current now flows through the relay. On a quick restart, the step-start relay is able to provide inrush limiting. This technique requires the addition of a shorting relay and a timer to control its turn on. The increased complexity raises the solution cost into the $20–$30 range.
Other inrush current control techniques include zero crossing triacs, active power factor control circuits, and inductive input filtering with damping. Most of these are complicated, bulky, expensive, and applicable only to AC inputs.
One method for isolated current monitoring is by using an isolation amplifier across a current sense resistor and a differential-to-single ended conversion amplifier feeding an ADC. Another method is to use an isolated delta-sigma (ΔΣ) modulator with an external digital filter.
As seen, controlling, protecting, and monitoring high voltage DC supplies requires cobbling many components together and making them work safely and seamlessly. This is not a trivial task. These discrete solutions are large, component-intensive, expensive, and lack safety certifications. An integrated and certified solution is needed to shorten design time and certification effort from many months into a few weeks.
Figure 2. (a) LTM9100 AnysideTM High Voltage Isolated Switch Controller with Telemetry (b) LTM9100 soft-starting, a 270V Load with Controlled 200mA Inrush Current
Integrated Solution for High Voltage Power Control & Telemetry
The LTM9100 µModule® (micromodule) IC is a compact all-in-one solution for controlling, protecting, and monitoring high voltage power supplies up to 1000V DC (Figure 2a). A 5kVRMS isolation barrier separates the logic and digital interface from the switch controller driving an external N-channel MOSFET or IGBT switch. The isolation is needed for control circuit protection, operator safety, and breaking ground paths. The load is soft-started (Figure 2b) and the supply is protected from overload with a current-limited circuit breaker. Isolated 10-bit ADC measurements of load current and two voltage inputs are accessed via the I2C/SMBus interface, enabling power, energy and thermal monitoring of the high voltage bus.
Figure 3. Inside Peek at Linear Technology’s Isolator µModule® Technology The LTM9100 utilizes Linear Technology’s isolator μModule technology (Figure 3) to translate signals and power across an isolation barrier. Signals are encoded into pulses and passed across the isolation boundary using coreless transformers formed in the µModule substrate, resulting in an extremely robust bidirectional communication scheme. Uninterrupted communication is guaranteed for common mode transients of 50kV/µs. The isolated side is powered by a fully integrated DC/DC converter, including the transformer, eliminating the need for external components. To guarantee a robust isolation barrier, each LTM9100 controller is production-tested to 6kVRMS. The LTM9100 will be recognized by the UL 1577 standard, saving months of certification time for the end equipment manufacturer. High distance through-insulation translates to a high ±20kV ESD level across the barrier. The μModule package integrates several components and technologies to deliver a costeffective, advanced solution that minimizes board space and improves electrical and thermal performance.
Due to its isolated nature, the LTM9100 is easily configured for high side, low side (ground return) and floating applications (Figure 4). The LTM9100 is versatile enough to control inrush current not just in hot-swappable cards, but also in AC transformers, motor drives, and inductive loads. Adjustable undervoltage and overvoltage lockout thresholds ensure that the load operates only when the input supply is in its valid range. The 22mm x 9mm x 5.16mm BGA package provides 14.6mm of creepage distance between the logic side and the isolated side.
Figure 4. LTM9100 in a High Side or Low Side Switching Application
Conclusion
Traditionally, high voltage DC supplies are found in industrial environments, but other electronic systems are also moving towards higher voltages to lower costs and raise the efficiency of power distribution, especially in power-hungry systems. These supplies need a simple way to control inrush current, protect themselves and to monitor their usage. The first-of-its-kind LTM9100 delivers this simple and compact solution, beating discrete and relay based circuits by providing a certified ready-to-go solution, saving board area and multiple months of design time and certification effort. All the needed functionality, including digital telemetry and isolated power, is wrapped in a compact, surface mount, and low-profile BGA package.
Author: Pinkesh Sachdev, Product Marketing Engineer, Mixed Signal Products, © Linear Technology Corp. (now part of Analog Devices)
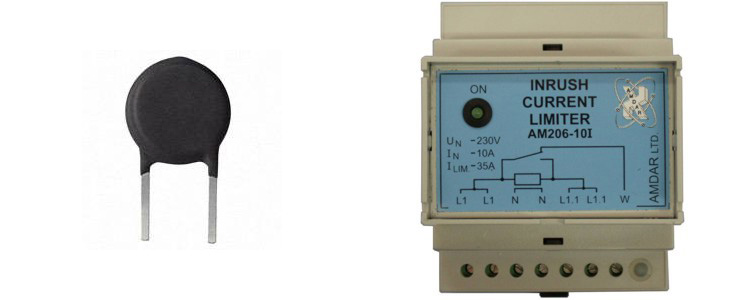
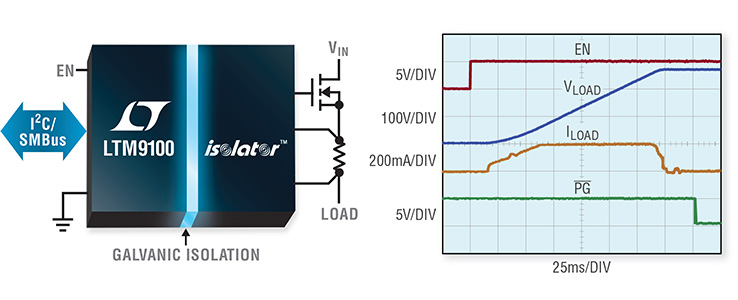
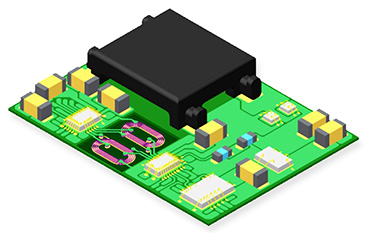
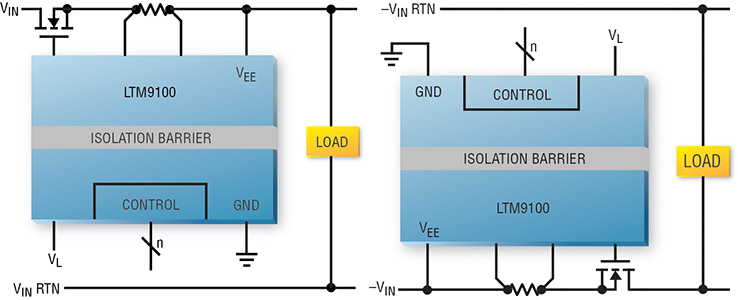
Author: Pinkesh Sachdev, Product Marketing Engineer, Mixed Signal Products, © Linear Technology Corp. (now part of Analog Devices)