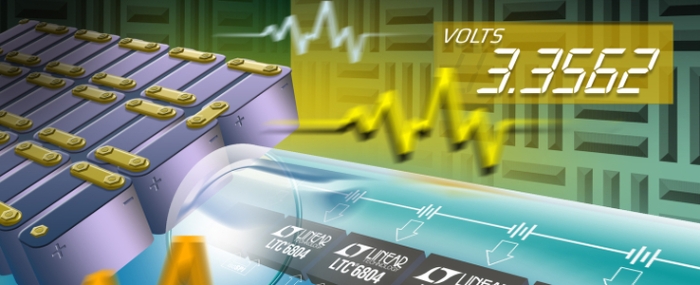
© linear technology
Application Notes |
The Commercialization of Space
There is a race to deliver a commercial broadband network in space that provides easily accessible, low cost Internet connectivity anywhere on earth.
The low earth orbit (LEO) constellation of 648+ satellites planned by OneWeb is facing potential competition from SpaceX, Google and Facebook. Meanwhile the existing medium earth orbit (MEO) O3B Networks constellation continues to expand. Other developments such as LeoSat’s constellation of 78+ satellites strive to offer point to point data networking that will provide industry and governments with commercially available data link capacity anywhere in the world.
Billions of dollars of investment are going into the industry and it is changing rapidly, with new commercial companies competing and collaborating with established space industry players. Add to this educational and experimental cubesats, scientific and earth imaging services such as Google’s Terra Bella and there is a sense that the industry is buzzing with new innovation and opportunity, overlaying the traditional space business of governments and space agencies.
From an equipment perspective, the major drivers for commercial space operations are to reduce the cost of satellites and launch vehicles, which can be achieved by making the satellites smaller and lighter while increasing their performance. This implies higher integration at the PC board level by using state-of-the-art, modern ICs and commercial rather than space-grade components.
While this sounds straightforward, the major risk comes from abandoning flight-proven, radiation-hardened ICs that have formed the backbone of space electronics for decades. Use of commercial components that were not designed for operation in space presents a challenge for satellite designers. Foremost is the safety and reliability of equipment when subjected to the effects of radiation and operation in a hostile environment. Failures can have serious implications from compromising performance to forcing premature de-orbiting and replacement, or worse still a loss of control with the potential risk of damaging other satellites and creating space debris.
Clearly there is a calculation to be made for large constellations. Is it cheaper to use standard commercial parts and accept that replacement satellites will be needed, or to develop an alternative approach to select products using a testing methodology to evaluate their suitability for space flight applications.
In reality up-screening components in this way is rarely simple and is best avoided unless there is no other option. Fortunately, new developments from the semiconductor industry provide options. Linear Technology is applying its know-how and experience from space-grade products to support new product grades aimed specifically at making modern, high-performance ICs available to space users.
One obstacle in use of commercial grade ICs is in the packaging. Traditionally, the space industry has resisted the use of non-hermetic plastic packaging, based on concerns of outgassing and other package-related issues. However, many new products have packages that have been developed specifically to enhance performance of the IC and cannot easily (or economically) be changed to a ceramic or metal package type.
So attention has now turned to how such products can be qualified and screened with tests that will provide confidence of reliability in space. AEC-Q100 qualification is frequently cited by OEMs as a requirement, but this relates to initial product qualification, not production screening, and does not confirm the suitability of a product for operation in space.
Returning to the topic of radiation performance, while many space-grade products are radiation hardened by a combination of process changes and design techniques, commercial products tend to exhibit differing responses that may vary from one wafer lot to the next. So each product type and production lot should be characterized by performing radiation testing.
But there are potential problems, as even a single date code of a product could contain silicon from different wafers or wafer lots. It is not normally possible to purchase commercial grade product from a specific date code or wafer lot, and not usually possible to have wafer level traceability without buying space- grade products. Furthermore, IC manufacturers invest millions of dollars in electrical test hardware and expertise, which would not be practical to replicate at the satellite OEM or radiation test lab.
So, for complex ICs, one approach that the OEM can take is to irradiate and test products at the PC board or sub-assembly level with the application criteria used to measure the performance degradation. The disadvantage with this ‘black box’ approach is that system-level parametric shifts may be difficult to attribute to component-level behavior and a root cause. Without the support of the IC manufacturer for lot traceability, process data and in-depth product know-how, it is difficult to determine if responses to radiation effects are representative and accurate. The time taken to identify problem components, redesign the circuit and repeat the radiation tests may have serious schedule consequences for the program in the race to space.
For these reasons, Linear Technology has developed new product grades to meet the needs of commercial space applications. For more demanding mission profiles a lot-based screening and qualification similar to that used for space grade ICs is utilized. Two examples of products that facilitate the development of smaller, lighter satellites are the LTC2378 20-bit analog-to-digital converter (ADC) and the LTC6804 Battery Stack Monitor. Both products provide significant improvements in performance and integration when compared with existing space-grade solutions where complex functions are often built up from op-amps, comparators, logic and transistors. This tried and tested method allows a high-level of confidence to be established regarding failure modes and radiation performance but cannot compete with a modern integrated circuit implementation on size, weight, and power. For example the LTC2378-20 is a low power SAR ADC that combines outstanding 104dB signal-to-noise ratio with best in class 0.5ppm integral non-linearity making it possible to design more sensitive sensor electronics with high dynamic range, faster sampling and lower power. In the case of the LTC6804, it can replace an entire PC board of components with each IC able to measure twelve series-connected battery cells with an accuracy of 0.04%. Cell balancing functionality optimizes the performance of the battery stack, ensuring all cells are safely charged to maximum capacity and could provide improved design margin and longer service life in addition to potential size and weight savings. ----- Author: Steve Munns, Mil-Aero Marketing, © Linear Technology CorporationFigure 1 – LTC2378, 20-bit SAR ADC -----
Figure 2 – LTC6804, Multicell Battery Monitor