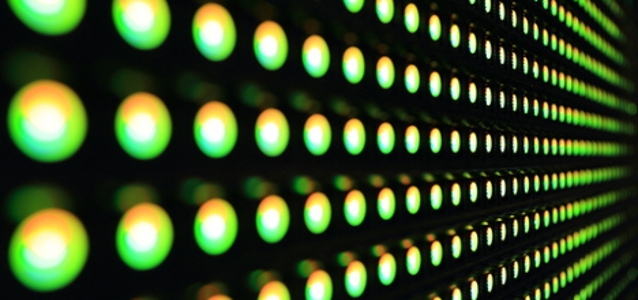
© ngweikeong dreamstime.com
Components |
SMI implements Centipede's massively parallel test for MEMS
Silicon Microstructures, Inc. (SMI) announces test-in-tray for parallel testing of MEMS based pressure sensors in volume production.
SMI has put test-in-tray processing into production for automated handling and testing. Pressure, temperature and calibration tests are performed on an array of devices held in the tray. The automated test-in-tray handler, supplied by Centipede Systems, provides rapid thermal conditioning over any computer controlled profile between -55°C. and +150°C. Independently controlled pressure ports allow dynamic leak testing over the full range of temperatures and pressures for effective screening of latent defects.
“Calibration and testing of MEMS pressure sensors over a full combination of pressures and temperatures allows us to provide sensors with better accuracy and reliability to our customers,” states Mr. Rainer Cholewa, President and CEO of SMI. “I am delighted with the inherent efficiency of test-in-tray processing so that we can supply high performance MEMS pressure sensors to our customers cost-effectively.”
“The test-in-tray format greatly simplifies handling and thermal management of MEMS devices under test,” says Dr. Tom Di Stefano, President of Centipede Systems. “A full tray of devices is indexed into the test position, where a mini-chamber encloses the tray of devices in a thermally controlled environment. The temperature and pressure stimuli are computer controlled to test and calibrate the parts rapidly through any combination of test conditions.” Di Stefano adds, “The test-in-tray format allows unlimited parallelism for added productivity in the future.”
Accurate testing of pressure sensors is complicated by thermally induced interactions and leaks. Testing a tray of devices in a mini-chamber facilitates the testing process. “Testing in a tray format has increased throughput many times over,” claims Mr. Holger Doering, COO at SMI. “Only the mini-chamber must be heated and cooled during the test, greatly speeding up the process of thermal testing. Also, since thermal, electrical and pressure connections are faster and more reliable when done in the tray format, the process is more easily automated.”
Di Stefano claims “SMI is a leader in adopting test-in-tray for MEMS device testing, and I am pleased with the cooperation between our companies in introducing test-in-tray methods into production.” He further asserts, “the test-in-tray paradigm offers a solution to the parallelism bottleneck and provides a standard handling format for automation of the semiconductor entire back end process.”