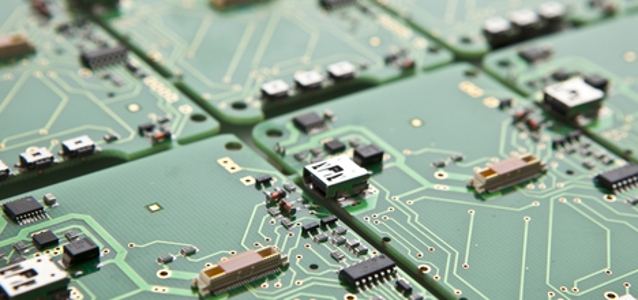
© eskymaks dreamstime.com
Components |
EV Group and Dynaloy cooperate
EV Group and Dynaloy jointly develop complete single-wafer cleaning solution for 3D-IC/TSV, Advanced Packaging, MEMS and compound semiconductor applications.
EV Group (EVG) and Dynaloy, LLC, wholly owned subsidiary of Eastman Chemical Company, introduced CoatsClean—an innovative single-wafer photoresist and residue removal technology designed to address thick films and difficult-to-remove material layers for the 3D-ICs/through-silicon vias (TSVs), advanced packaging, microelectromechanical systems (MEMS) and compound semiconductor markets.
CoatsClean provides a complete wafer cleaning solution that offers significant efficiency, performance and cost-of-ownership (CoO) advantages compared to traditional resist stripping and post-etch residue removal methods.
"Increasing wafer processing challenges associated with the adoption of new materials, device architectures and packaging schemes requires a new, holistic view of wafer cleaning, where the chemistry, process and equipment are all critically important and must be addressed in combination," stated Steven Dwyer, business director at Dynaloy. "We're pleased to be working with EV Group on developing and commercializing CoatsClean technology to meet the needs of our customers for a more cost-effective, flexible approach to thick-film resist removal."
CoatsClean incorporates a number of key features to boost performance and productivity, as well as reduce CoO, compared to wet bench and other traditional wafer cleaning approaches. The CoatsClean process and chemical formulation are engineered to perform at higher temperatures, resulting in faster stripping rates and cycle times. This enables CoatsClean to operate as a single-wafer process for thick resist films and difficult-to-remove resists—resulting in improved performance, consistency, reproducibility and repeatability. The engineered formulation also enables selective stripping of the resist.
CoatsClean is also unique in its ability to dispense a small amount of material on the top of the wafer, and then activate the material with direct heat. This direct utilization of the material and heat dramatically reduces the strip material used. CoatsClean uses fresh solution for each processed wafer compared to competing techniques that use an immersion bath—resulting in greater process efficiency and eliminating cross contamination. The highly selective application of resist strip material eliminates damage to the wafer backside. The entire CoatsClean process is performed in a single bowl, which reduces tool footprint.
"CoatsClean applies the right chemistry at the right process conditions to provide optimal cleaning results," stated Paul Lindner, EV Group's executive technology director. "By combining our respective strengths, EV Group and Dynaloy can now offer our customers a complete wafer cleaning solution that significantly reduces their CoO and achieves superior performance."
The CoatsClean tool series, which includes EV Group's EVG301RS and EVG320RS XT platforms, leverage EV Group's core competencies in controlled dispense, heating and temperature control, fluid rinse and wafer handling technologies. The EVG301RS system targets research and development, as well as low-volume production on substrates up to 300 mm in diameter, while the EVG320RS XT features up to eight process modules to address high-volume production requirements on substrates up to 300 mm in diameter. The systems are highly modular in design to allow for a wide range of configurations and combinations of chemicals.
EV Group will be responsible for selling the CoatsClean systems and providing customer support, while Dynaloy will be responsible for selling the CoatsClean resist stripping materials. CoatsClean systems have already been installed for customer demonstrations, and EVG and Dynaloy are now accepting orders for the systems and resist stripping materials.