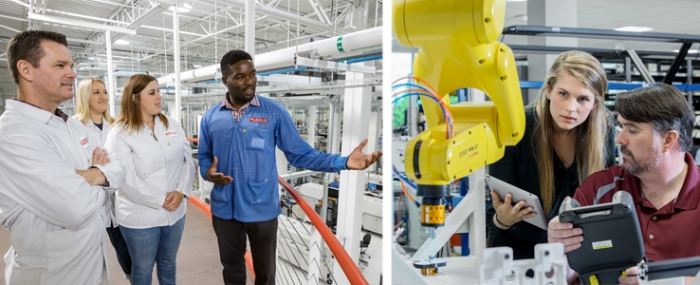
© Plexus
Electronics Production |
Autor: Jürgen Seibert, Vice President, Business Development - EMEA at Plexus.
A waste-free supply chain
Developing a Lean Six Sigma culture is not just about the tools and techniques. More importantly, it is about deciding on focus areas for improvement and involving everyone to help drive the change.
In the face of continual customer pressure for cost reduction, performance improvement and to maintain competitive advantage, these principles can continuously improve the business performance of electronics manufacturers. The majority of today’s global electronics industry faces tremendous pressure to lower costs and reduce time to market, while following the rapid pace of innovation. Short lead-times can be critical to success and management teams have to keep focus on minimizing the time it takes to introduce new concepts to the market. How that process is managed is essential for an efficient product development and launch, with particular focus on the importance of a waste-free supply chain. Waste and variation are everywhere: existing in every process and every interaction between humans, systems and functions. They create performance issues, soak up resources and affect customer satisfaction. They also threaten health and safety and, potentially, even job security. The Opportunity of Lean Six Sigma The application of Lean Six Sigma principles to production process, as we know it today, started with the development of the Toyota Production System (TPS) in the 1940s and promised continuous improvement into every area of business performance. In general, Lean is focused on identifying value in the eyes of the customer (what they are prepared to pay for) and removal of waste (what they are not willing to pay for). Whereas Six Sigma takes a structured approach to reducing variation in processes to ensure products are manufactured without defects. During the last 30 years, many manufacturing companies tried to replicate Toyota’s approach and spent millions of dollars to implement both principles throughout the entire organization and the product life cycle with the ultimate objective to be more efficient and reduce operating costs. However, it has been found that Lean Six Sigma improvements within the manufacturing area do not typically present as big an opportunity as initially thought compared to those that are found in the rest of the value stream. Priority #1: Zero Defects Within the electronics manufacturing arena improvement focus areas ultimately differ, depending upon the dynamics of the business. For example, reducing the cycle time of a product by one second in a low mix high volume environment will produce a significant benefit. Conversely, in a high mix low volume environment the same approach will produce minimal benefit and the focus will be more around driving optimization of equipment changeovers. One major aspect in mature Lean Six Sigma manufacturing operations, however, is the achievement of zero defects – creating products that can be manufactured on processes that are engineered to run at an optimal capability level and produce little, if no, variation. This is especially important in highly regulated industries, such as aerospace and healthcare, where even the most minor variation can prove catastrophic. Here, the regulations are as demanding as ever, while the time from conception to production is continually being pushed down and products are increasingly pure electronics. In light of extremely stringent regulations, designing and manufacturing in these industries needs close tracking of every element and every stage in a product’s developement. Impact on the whole Supply Chain The focus on defect-free products via Lean Six Sigma also emphasizes the quality within, and the control of, the supply chain. The knock-on effect of this change is that equipment suppliers also have to develop processes and deliver components that match this quality level. Any electronics manufacturer that still employs inspection and testing, on receipt of purchased products, as a means of protecting the customer from receiving poor quality goods, should review its whole supplier development strategy from a Lean Six Sigma perspective. Today the emphasis has to be to drive improvement back into the supply base and engineer-in the quality of supplied product. If these tactics are employed effectively, the consequence is a significant reduction in the requirement to inspect and test. Lean Six Sigma development of the supply chain can lead to significant benefits in many areas as well as a significant improvement in delivery performance. There will also be an inventory reduction, which decreases the inventory holding space needed. The consequence: less working capital required with subsequent cash cycle improvement and higher operating margins. It’s a Team Effort No matter the focus area of Lean Six Sigma principles, manufactures cannot afford to rely on just replicating Toyota’s lean principles. Too often they dismiss a critical success factor: the psychological impacts, such as implementing new working methods, and convincing the dominant leader or leaders to gain executive sponsorship. In many cases, this has led to failure. The success of the implementation of a Lean Six Sigma operating philosophy depends on how these changes are introduced and managed. And the change of organizational culture differs by the dominant leader/leadership style, national/local culture, business size/demographics, existing business practices and type of products or services. Sustainability can only be achieved by creating a culture of employee engagement where people at every level of the organization embrace and believe in the change. This not only involves employees participating in Kaizen activity. It is also about job satisfaction, variety and relevance, understanding of business vision and strategy, personal development, reward and recognition, but most importantly, listening and acting upon the voice of the employee. Introducing cultural awareness programs for executives, change leaders and managers can create understanding and competence in this area. These approaches take a significant amount of time and, to be successful, require an understanding of change psychology and the human reaction to change. There is still room for further improvement of the Lean Six Sigma application within electronics manufacturing. After over 70 years of lean at Toyota, the company still believes it has a long way to way to go to remove waste entirely from its value streams.Jürgen Seibert © Plexus
Autor: Jürgen Seibert, Vice President, Business Development - EMEA at Plexus.