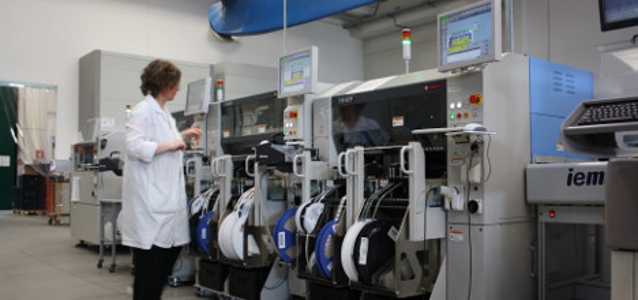
© yamaha
Electronics Production |
Italian CO-EL sees return on equipment investment
Investing at the right time, the right place and with the right specs makes a huge difference, no body denies this. But investing is never an easy decision, especially when economic conditions are uncertain.
In 2014, CO-EL S.rl, a CEM based in Mozzate north of Milan, decided the time was right to upgrade its 3'500 square-meter facility with three new surface-mount lines from Yamaha. It was a big decision at a time when important markets were recovering only tentatively after the recent recession.
Difficult periods are the best times to invest, to be ready to move forward when conditions start to become better,” founder and co-owner Lorenzo Colombo explains. “We seized the opportunity to work with Yamaha, and this has allowed us to achieve dramatic gains in capabilities, productivity and quality.” The decision to move forward with Yamaha involved replacing all existing surface-mount automation with three complete new Yamaha lines populated by the latest YS24, YS24X and YS12 mounters and YSi-V inspection stations. The three lines are fed by two new Yamaha YSP printers, which are capable of performing 100% paste-on-pad inspection in real-time and so help verify perfect process control. “The printer is critical to the performance of the line,” comments Lorenzo. “It not only launches the entire process and delivers two-in-one flexibility, but also performs 100% paste-on-pad inspection in real-time. This allows us to be certain we have the best possible foundation for the other production processes downstream.” Lorenzo believes the time operators spend dealing with quality-control issues is about 70% lower since the new assembly lines went live. “Automatic Optical Inspection (AOI) used to be vital for spotting defects and preventing sub-standard boards escaping the factory,” he adds. “Now, our new Yamaha lines produce work to such a consistently high standard that AOI has become mostly about confirming each board is correctly assembled. We have recently produced a double-sided board with about 450 components per assembly, and achieved a defect rate of four or five per 1ä000 boards, or about 10ppm.” The investment has yielded several improvements for CO-EL, such as higher speed, streamlined setup, improved placement accuracy and reduced quality-control workload, and Lorenzo estimates that it has helped to boost the company's productivity by as much as 35%. The next step is to upgrade the company’s second factory in Romania, which was opened in 2007 and has one surface-mount line.© Yamaha