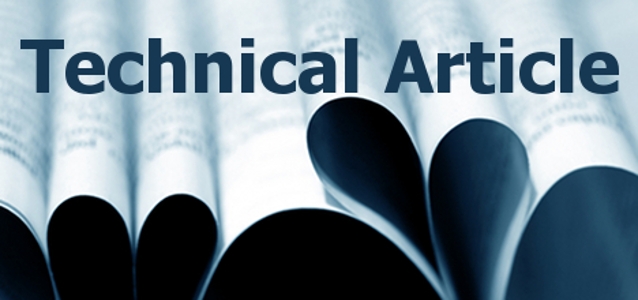
© janaka dharmasena / dreamstime.com
Application Notes |
A short history of hybrid & module technology
Why it continues as a packaging technology of choice for high reliability applications.
This is a product release announcement by Linear Technology. The issuer is solely responsible for its content.
Hybrid and module technology has been evolving for more than 50 years and now in the form of COTS (Commercial-Off-The-Shelf) modules is making major contributions to reducing design cycles, mitigating obsolescence and addressing SWaP (Size, Weight and Power) challenges. Let’s take a look back the history of the technology and explore some of the factors that are important to the aerospace and defence industry.
Early Hybrids
In the late 1950s, advances in computing using discrete transistors made huge strides forward, but circuit boards were becoming increasingly complex, sometimes with thousands of interconnected transistors, diodes, resistors and capacitors. A solution was needed to improve the density and reliability. Government agencies funded various hybrid circuit ideas.
The military was especially interested and active in this field. In 1958, the US Army funded RCA to develop their “micro-module” concept. This took the approach of uniform-sized cubes externally configured so that they could be clipped together. Internally, small wafers of the various discrete components were vertically stacked and interconnected at their edges. Component density by volume was more than doubled and reliability increased by a factor of six, which delighted the military who invested further over the coming few years. In 1962, according to an article in Electronic Engineering Times, a 10-component module cost $52, around 2.5 times the cost of a conventional discrete PCB solution.
Despite its cost, the RCA micro-module was very successful but short-lived and the birth of the integrated circuit (IC) no doubt contributed to its demise. At nine times the cost of a hybrid solution, early ICs were often the beneficiary of military or government funded programs and one notable 1962 project was the Raytheon-built Apollo Guidance Computer for NASA.
With the rapid evolution of ICs, their advantages over hybrids and modules were soon recognized. In that regard, it seems surprising that hybrid circuit technology survived at all. However, the military often had broader considerations, including product stability and long-term availability, reliability, utility versus innovation and complex operational requirements. These factors together with the specific technical advantages of hybrids and modules have undoubtedly contributed to their continued usage over the last 50 years.
Integration
In the timescale spanned by this article, ASIC technology has revolutionized the industry. Initially, gate arrays of a few hundred gates offered the military a route to improved digital integration and as gate densities rapidly advanced and development tools were refined, the days of the hybrid circuit looked numbered. In the late 1980s, military equipment designers recognizing the success of digital ASICs, attempted to apply the same techniques to mixed-signal circuits. Their motives were dominated by the need for miniaturization, as more and more complex systems were demanded by the military, which had big budgets at that time. But difficulties adapting full custom design tools for customer use and the complexity of analog design, meant that mixed-signal ASIC remained very resource intensive and highly reliant on semiconductor manufacturer design teams for, in effect, full-custom designs. While analog ASIC design tools and technology have made significant progress, the breadth of real-world analog problems are still difficult to implement with off-the-shelf semi-custom circuits. Thus, hybrid circuits have continued to offer a means of integrating various high-performance analog and signal-chain functions of differing process technologies into a single package when off-the-shelf products will not do the job.
Performance
Military and aerospace systems are generally designed on the basis of modular sub-systems. For example, line replaceable units (LRUs) simplify service and operational support. Interconnecting LRUs rely on standards such as the MIL-STD-1553 bus interface. Implementing these functions in hybrids, modules, ASIC macros or on standard format circuit boards has become the preferred approach and they are, in effect, application specific standard products (ASSPs) and building blocks.
This highlights two important factors. First, there is nothing to be gained by re-inventing the wheel and designers are more usefully employed focusing on the core intellectual property of the system. Secondly, the military and aerospace industry is a small user of semiconductors by today’s standards and developing solutions at the module or board level is a more realistic proposition than a monolithic IC-level ASSP.
Traditionally, the performance requirements of power supply modules has also aligned well with hybrid module technology where the use of hermetic metal can packaging supports the power density and thermal management needs of high-temperature, high-reliability military applications. With increasing power requirements from large FPGAs and microprocessors, the drive for more efficient power architectures and point-of-load (POL) regulation has given rise to new module solutions.
Applications such as radar have also long-relied on hybrids and modules for RF and microwave solutions. Only in recent years have there been monolithic IC products that begin to address some of these needs but now the integration needs of modern highly parallel phased array radars are again focusing attention on module solutions.
Security
Product obsolescence is an acute problem for the military. A 30- to 50-year program life is commonplace so military and aerospace equipment suppliers are continually looking for ways to mitigate risk. Hybrids and modules have been one approach to try and isolate the defense industry from the rapid pace of change in the semiconductor industry. Memory modules are a specific area of interest because of the particularly short lifecycle of DRAM and SRAM technology. The concept of a standard form factor and pin-out can be maintained, while the memory dice inside the module can be updated. This is a lot easier to write about than it is to do in practice, in part, due to continual advancements in access times, architectures and supply voltages. On another level, the use of standard format embedded processor cards provide an alternative higher-level approach where space permits. However, the notion of standard form factors is central to many obsolescence management strategies and has certainly been a major influencing factor in the long life of hybrid and module solutions.
Hybrids and modules is also benefit because a full-custom module can be used to conceal valuable intellectual property related to the hardware design, making it more difficult to reverse engineer. Simply looking at part numbers on packages will not be enough to decode the design hardware. Furthermore, some semiconductor dice are also not readily available on the open market.
From Full Custom to Modern Day COTS
The previous arguments for continued use of hybrids and modules in military systems remain valid. However, it is important to recognize that the commercial pressures on military equipment manufacturers are greater now than ever before, and in particular, costs and time to market.
Full custom hybrid designs are expensive and take a relatively long time to develop. More alternative monolithic IC solutions are becoming available every year. While new hybrid designs are still developed at major defence companies, there is a detectable trend towards out-sourcing manufacture as volumes decline.
The picture for COTS modules is quite different. There is definite momentum toward module-based solutions driven by both technical and commercial considerations. Switching power supplies and signal chains are two areas that are particularly well suited to module implementation as efficient designs need specialist knowledge that is a scarce commodity in today’s military design teams.
Enter μModule® Products
μModule products are an example of modern day COTS modules. Launched by Linear Technology in 2005, one of the first products provided a complete 12A DC/DC regulator in a 15mm square surface mount package (Figure 1).
Figure 1. The LTM4601AHV 12A μModule DC/DC Regulator
Subsequently, a complete family of μModule products have been developed, including a wide range of power, interface and signal chain products with recently released examples such as the LTM9100 (Figure 2) and ADAQ7980 (Figure 3).
Figure 2. The LTM9100, High Voltage Isolated Switch Controller with Telemetry
Figure 3. The ADAQ7980 16-bit 1Msps Data Acquisition Subsystem
COTS Module Package Styles
Resembling a surface mount IC, each μModule regulator includes a complete system-in-a-package solution that simplifies design and minimizes external components. Internally, the layout and design are optimized for electrical performance and thermal efficiency. Built to the industry’s highest standards, these μModule products offer outstanding reliability, approaching that of standard ICs. LGA (Land Grid Array) packaging with gold finish pads and BGA (Ball Grid Array) packaging with SAC305 or SnPb solders are available in various temperature grades.
Figure 4. Two μModule Regulators with LGA & BGA Package Styles
Where needed, military temperature range versions of μModule products provide guaranteed data sheet performance through 100% electrical testing at ̶55ºC and +125ºC.
Conclusions
Fifty years ago, hybrids and modules were a technology of choice to miniaturize electronic circuits and improve their reliability. As the semiconductor industry became commoditized and product lifecycles diverged from those of the defence industry, hybrids and modules found a new role in obsolescence mitigation. While ASIC became the preferred approach for integration of digital electronics, the hybrid module found a niche solving difficult analog problems.
Meanwhile COTS modules have emerged in the form of Application Specific Standard Products, notably for power supplies, processors, signal chains and interfaces. These have been widely adopted as military equipment providers react to a new competitive age and recognize the importance of focusing scarce design resources on core competencies.
Today, defense budget pressures and shorter design cycles may make full custom hybrids increasingly a legacy solution, but without a doubt, COTS modules are increasingly becoming a technology of choice for the military and aerospace industry.
Author: Steve Munns, Mil-Aero Marketing Manager © Analog Devices Inc. (previously Linear Technology)
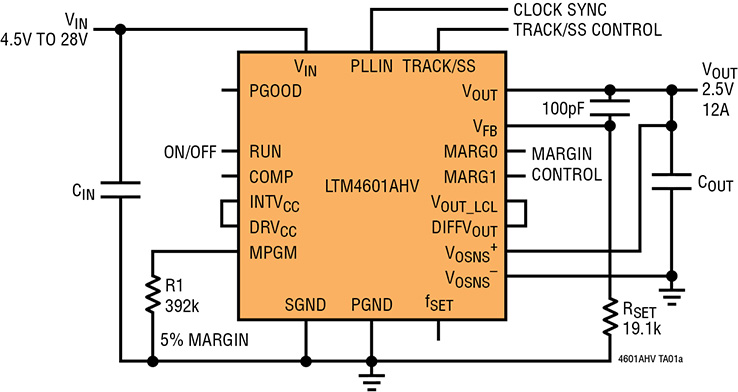
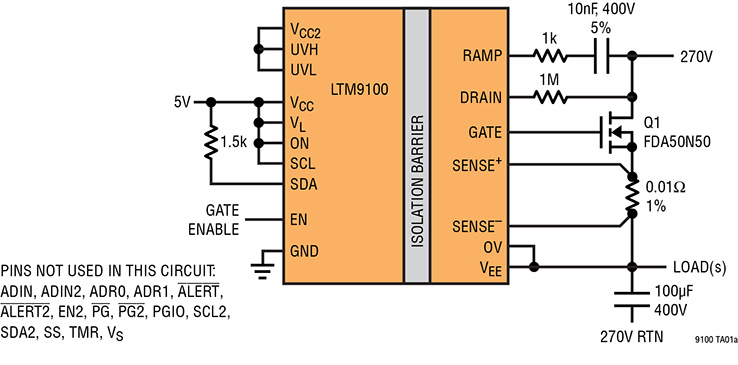
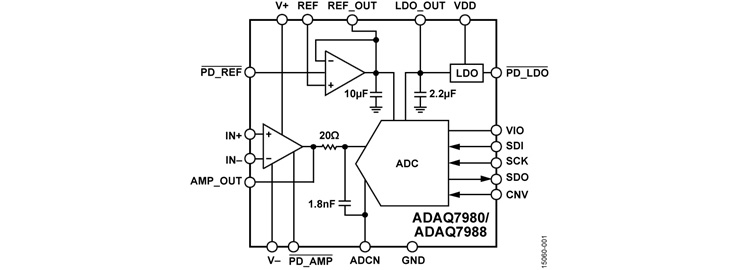
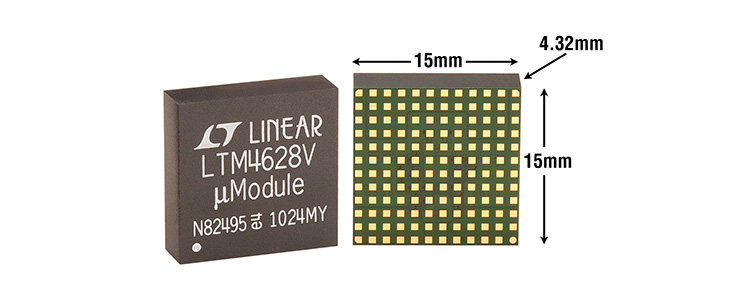
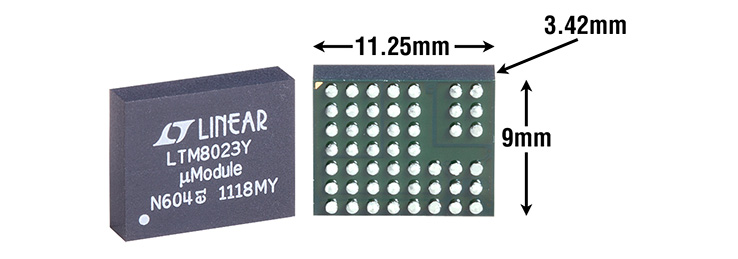
Author: Steve Munns, Mil-Aero Marketing Manager © Analog Devices Inc. (previously Linear Technology)