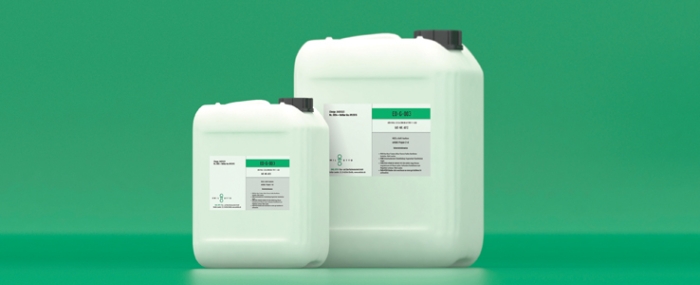
© Emil Otto
Products |
Emil Otto present new product range plus flux-concentrate
At this year’s productronica, Emil Otto will show their new product range for the first time to an international visitor group. The German flux producer already introduced those products at the national show SMT Hybrid Packaging 2017. The new product range includes alcohol-based, water-based and hybrid fluxes.
This is a product release announcement by EMIL OTTO Flux- u. Oberflächentechnik GmbH. The issuer is solely responsible for its content.
All new products are based on customers’ requests and were tested with the ‘Emil Otto in-house test’ based on the recommendations of the Fraunhofer Institute Oberpfaffenhofen. The trial series with all newly developed fluxes started early November 2016. The key development was based on new alcoholic-based multi-fluxes. All of the fluxes in the multi-flux assortment meet DIN EN 61 190-1-1 with L0 classification regarding corrosion behaviour, freedom from halogen, and surface resistivity of the uncleaned flux residues.
These multi-fluxes can be used for various soldering tasks. Manual and dip soldering are used at many companies in addition to the wave and selective soldering process. Emil Otto GmbH's alcohol-based fluxes are designed for this broad application spectrum. A flux that brings good soldering and performance properties to each individual application is needed, if the wave-soldering system run only on certain days of the month whereas in contrast hand soldering is conducted daily with different task assignments. The customer is not just able to minimize storage costs this way, but also avoids a potential source of error from unintentionally interchanging the fluxes.
Product variants A, B, and C were developed for the EO-B-001, EO-B-002 and EO-B-07 fluxes. The A variants generally have a low solids content of 1–2%. These variants were developed especially for full-tunnel-nitrogen applications. They feature a wide process window and great temperature stability to guarantee a better soldering result under full nitrogen. The B variants on the other hand represent the standard version with a solids content of 3%. The C variant, which exhibits a solids content of 4%, rounds out the spectrum. This was developed especially for power electronics, where large component bodies have to be soldered at low mounting densities.
In addition Emil Otto will show the new EO-B-006, EO-B-007, and EO-B-008 fluxes. EO-B-006 is a rosin-free flux. EO-B-007 is an economical alternative flux that can be used for wave, selective, and manual soldering. At 4%, EO-B-008 has a high solids content. EO-B-008 was specially developed for short wave-soldering systems, where the circuit board spends dwell time in the preheating phase.
Besides the alcoholic fluxes, Emil Otto will also present their new water-based Green Line-fluxes. EO-G-002 and EO-G-003 fluxes can be used during wave and selective soldering. Their water base renders these fluxes environmentally friendly and non-combustible. 'The solder-relevant properties of both fluxes are comparable to those of alcohol-based fluxes. This especially applies to soldering results in the areas of rise-through and wetting’, explains Markus Geßner, marketing and sales manager at Emil Otto GmbH.
The two fluxes differ in solids content and in their ingredients. Thus EO-G-002 exhibits a solids content of 3% whereas EO-G-003 has a 3.3% solids content. Furthermore, EO-G-002 contains synthetic resin, which clads of the residues on the circuit board. This cladding prevents the residues from being able to return to a solution during large temperature changes or elevated air humidity. Leakage currents and short circuits are thereby prevented if the circuit board is not cleaned after the soldering process.
Neither flux is combustible, so they are not classified as hazardous material and consequently have no legal restrictions on transport, storage, or subsequent handling in production. Therefore transport and storage costs diminish since storage in premises without explosion protection is possible. Use of the flux in production is likewise simplified, because neither special handling nor employee training with respect to the use of hazardous substances is necessary.
Last but not least, Emil Otto will also present their new hybrid flux. EO-Y-003 containing as little as 10% alcohol. So it's nearly a water-based flux already with very good soldering results and quite a clean circuit board. EO-Y-003 has almost all of the properties of water-based fluxes. It's economical, low-consumption, and easy to manage in terms of transport, storage, and handling. In contrast to water-based fluxes, it is low alcohol content renders it frost resistant enabling it to be transported and stored quite well in winter. EO-Y-003 exhibits a high 3.3% solids content. It was developed to be used in wave and selective soldering and thereby possesses a very broad range of uses. The soldering properties are very good, particularly with rise-through and circuit-board wetting. The process window is very broad with great thermal stability.
In addition to the newly introduced flux products, Emil Otto is also immediately offering selected fluxes as concentrate. The customer can self-prepare the EO-B-001, EO-B-002, EO-B-006, and EO-B-007 multifluxes. A complete package consists of granulate for the flux, and is designed for preparing 20 L of the respective flux. In addition to the multifluxes, the hybrid EO-Y-004 flux is also obtainable as a concentrate, where the complete package is designed for preparing 10 L of flux.
"Granulates have the advantage of being severely reduced in quantity and without hazardous-substance identification rendering them very attractive economically for transport over great distances. Flux can then be prepared on site with very manageable effort”, Geßner explains.
The name 'Emil Otto' has stood for the highest quality since 1901. As a privately owned company, Emil Otto has dedicated itself to developing and producing high quality fluxes. Both foreign and domestic market leaders have used the fluxes in particular for electronics production, strip tinning, and cooler construction as well as for galvanizing.
Reliable products and strong customer orientation have become our signboard over the years. Manufacturing is done according to the most modern standards; quality and environmental management have been certified for many years. Emil Otto deals flexibly with customer desires. Special products or product adaptations are developed and implemented in collaboration with systems manufacturers and institutes.