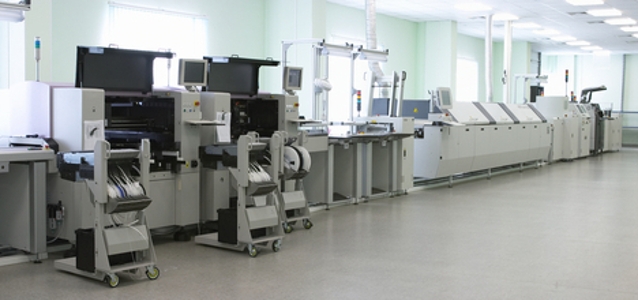
© dimitry romanchuck dreamstime.com
Components |
Electronic component counterfeit incidents continue record pace
Reported incidents of counterfeit electronic component parts this year are maintaining the record pace set in 2011, highlighting the need for continued vigilance and improved detection and avoidance measures at a time when U.S. defense representatives are scheduled to update acquisition rules, according to IHS.
Counterfeit incident reports from the beginning of the year through the end of August averaged 107.3 per month, up slightly from 107.1 in 2011. As shown in the figure attached, on a sequential 12-month basis, a total of 1,336 separate verified counterfeit-part incidents have been made for transactions involving a minimum of 834,079 purchased parts.
These figures are considered conservative because purchased parts reflect only a subset of all reported incidents.
Counterfeit parts are an escalating global supply chain challenge where a single occurrence represents widespread risk to product cost and quality, human safety, and national security.
These new counterfeit report figures arrive at a time when the U.S. Department of Defense (DoD) is scheduled to update the Defense Federal Acquisition Regulation (DFAR) Supplement to the Federal Acquisition Regulation (FAR) on October 3, 2012. These updates are part of measures intended to regulate the detection and avoidance of counterfeit electronic parts as part of the National Defense Authorization Act (NDAA) of 2012.
“Counterfeit parts represent a serious and growing risk to the electronics supply chain in general and to the aerospace and defense industry in particular,” said Rory King, director, supply chain product marketing at IHS. “Each month that passes, more than a hundred counterfeit incidents comprised of thousands of suspect parts are reported. That’s why the spotlight is shining squarely on tighter policies and procedures aimed at counterfeit detection and avoidance. The good news from all this attention is that an increasing number of supply chain participant companies are joining credible anti-counterfeiting organizations like ERAI – exclusive partner to IHS and an organization that monitors, investigates, and reports on counterfeit electronic components – and filing a greater number of reports that then serve as proactive alerts to others in the supply chain of real counterfeits in circulation.”
Among all reporting entities in IHS figures, sources include the Government-Industry Data Exchange Program (GIDEP) and ERAI. Consistent with 2011, ERAI represents the significant majority of reports made – 88 percent of year-to-date 2012 totals.
As IHS recently noted, incidents of counterfeit parts have quadrupled since 2009. Counterfeit parts often are cheap substitutes or salvaged waste components that fail to meet quality requirements, leading to potential failures. However, each incident can include thousands of purchased parts. On average, more than 1.4 million purchased parts have been involved in suspect counterfeit and high-risk transactions during each year for the past decade.
Defense to step up use of known incident reports
Among other requirements, NDAA Section 818 seeks to significantly improve systems for the detection and avoidance of counterfeit electronic parts at all tiers in the supply chain, at the same time shifting the burden of costs associated with rework or corrective action for issues involving these parts back upon defense contractors. They specifically spell out new requirements for analyzing, assessing and acting on these reports of counterfeit electronic parts and suspect counterfeit electronic parts.
A clear example of the need for counterfeit detection and avoidance methods that leverage all counterfeit incidents reports available came in November 2006 when a critical component was first reported to ERAI as being victim of counterfeiting. The use of destructive and non-destructive techniques found that these components were very different, had evidence of remarking, and were potentially reconditioned. Information concerning the die size and date, as well as information received directly from the manufacturer, suggested the parts were counterfeit.
The part was later reported again to ERAI in November 2008 and March 2012. Later in March 2012, and six years since the first of three occurrences was reported to ERAI, it was again reported to GIDEP. That this single part was subject to four separate reports illustrates the complexity of detecting counterfeit parts that are pervasively circulated and re-circulated throughout the supply chain.
The scenario also speaks to the critical importance of increased use of counterfeit incidents reports. Many companies have specific screening processes for components with matches to instances of counterfeits reported to the marketplace, including everything from more stringent testing of the parts to avoiding the use of those parts altogether. Meanwhile, new NDAA regulations specifically spell out new requirements for analyzing, assessing and acting on reports of counterfeit electronic parts and suspect counterfeit electronic parts.
“Industry’s ability to take advantage of counterfeit incidents reports is a huge risk mitigation and cost avoidance opportunity for any company, while also playing a vital role in counterfeit detection and avoidance compliance with new NDAA regulations,” King noted. “For instance, a critical component was first shared with ERAI members in 2006 before again being reported two more times to the organization and once six years later to GIDEP. It’s easy to see how early awareness to all counterfeit incidents involving active and discontinued components that are continually re-circulated throughout the supply chain is a critical element of proactive risk assessment.”
Significant avoidable expense of counterfeits
As reported previously by IHS, the expense to resolve a single such counterfeit incident can be massive. Testimony given at a November 2011 hearing of the Senate Armed Services Committee revealed how the U.S. Missile Defense Agency learned that mission computers for Terminal High Altitude Area Defense (THAAD) missiles contained suspect counterfeit devices that could have led to an entire system failure. The cost of that fix was nearly $2.7 million.
All told, the hearing exposed the complexity of keeping pace with the ongoing and increased sophistication of counterfeiters—something that access to more counterfeit incidents reports can help keep pace with.
Defense companies must act now
To help combat the counterfeit problem, President Obama in December 2011, signed the fiscal year 2012 U.S. National Defense Authorization Act (NDAA), which added regulations for counterfeit part detection and avoidance. The pending October 3, 2012 updates to the DFAR supplement will implement portions of section 818 of NDAA that must add definitions specific to counterfeit parts, define contractors' responsibilities, and clarify the government's role.
In March 2012, the undersecretary of defense for acquisition, technology and logistics Frank Kendall issued a Department of Defense Memorandum, ‘Overarching DoD Counterfeit Prevention Guidance.’ In the memo, the department laid out an actionable definition of counterfeit material and also emphasized the importance of taking immediate action to apply existing policy and procedures, prior to establishing new DoD policy and procedures or waiting for forthcoming changes to the Defense Federal Acquisition Regulation Supplement (DFARS).
Risk assessment a priority
According to IHS, a typical bill of materials (BOM) or parts list for a military application system can have anywhere from a few hundred to more than tens of thousands of purchased parts, of which between 0.5 to 5.0 percent typically match reported incidents of counterfeit parts. This is in addition to entirely different risks that exists such as part obsolescence or sole source supply issues. By implementing new capabilities that make use of real counterfeit incident reports, electronics makers can avoid risk, while cutting costs and complying with the NDAA.